Spiral Chute
Applicable materials: Iron, manganese, tin, tungsten, tantalum, niobium, chromium ore, lead-zinc, copper ore, zircon sand, coal mine, monazite, rutile, Seaside sand, silica sand, and other metal and non-metal minerals with sufficient specific gravity difference.
Description
Spiral chute is mainly used to select fine particles with a particle size of 0-2 mm. The spiral chute blades are mainly made of fiberglass, and the inner surface is coated with a wear-resistant lining, usually polyurethane wear-resistant glue or epoxy resin mixed with emery, which is more wear-resistant and has high sorting efficiency. There is a wet pulp distributor above the spiral chute, and an ore receiving chute at the end of the chute to intercept fine, medium, and tailings respectively. When using the equipment, it needs to be set up and fixed to the ground with a rack. The screw unit is divided into single-head, double-head, three-head, and four-head structures. The blade diameters are 400, 600, 900, 1200, 1500, etc. to meet the needs of different processing volumes.
Advantages
- The mineral processing process requires no power and saves energy.
- No need to add washing water and low water consumption.
- The structure is simple and easy to maintain and manage.
- It has good processing effect on fine-grained mineral materials and large processing capacity.
Principle
Use a sand pump to transport the ore sand to the ore feed port at the upper end of the spiral chute, and add supplementary water at the same time to adjust the slurry concentration. The slurry swirls from the inclined surface of the spiral chute. During the process, it is washed by the water flow and its own centrifugal force. Mineral sands of different densities, particle sizes, and shapes are separated on the inclined surface. The heavier minerals swirl close to the inner wall with the water flow. It flows down, and finally, the concentrate flows into the concentrate tank and is connected through a pipe. The lighter minerals swirl in the middle and outside of the blade and enter the middle ore and tailing tank.
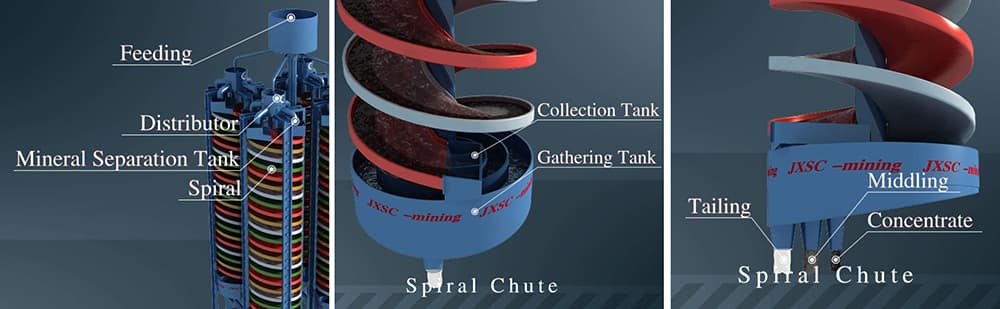
Specification
Model | 5LL-2000 | 5LL-1500 | 5LL-1200 | 5LL-900 | 5LL-600 | 5LL-400 | |
Outside dia (mm) | 2000 | 1500 | 1200 | 900 | 600 | 400 | |
pitch(mm) | 1200 | 900, 675 | 900, 720, 540 | 675, 540, 405 | 450, 360, 270 | 240, 180 | |
Pitch Dia Ratio | 0.6 | 0.48, 0.36 | 0.75, 0.6, 0.45 | 0.75, 0.6, 0.45 | 0.75, 0.6, 0.45 | 0.6, 0.45 | |
Lateral slope | 9° | 9° | 9° | 9° | 9° | 9° | |
Number of installed spiral heads | 2 | 2-4 | 2-4 | 2-4 | 2 | 2 | |
Feeding Size (mm) | 2~0.04 | 2~0.04 | 2~0.04 | 2~0.04 | 2~0.04 | 2~0.04 | |
Feeding Density(%) | 30~55 | 30 ~55 | 25 ~55 | 25 ~55 | 25 ~55 | 25 ~55 | |
Capacity(t/h) | 7~10 | 3~5 | 3~4 | 2~3 | 0.8~1.2 | 0.15~0.2 | |
Boundary Dimension | Length(mm) | 2120 | 1600 | 1360 | 1060 | 700 | 460 |
Width(mm) | 2120 | 1600 | 1360 | 1060 | 700 | 460 | |
Height(mm) | 5600 | 5300 | 5230 | 4000 | 2600 | 1500 | |
Weight(kg) | 1200 | 800 | 600 | 400 | 150 | 50 |