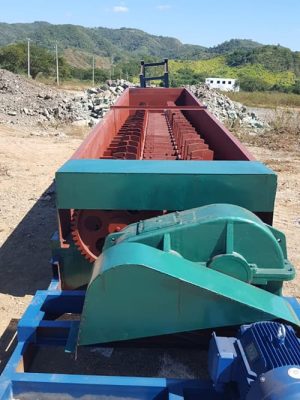
Turnkey Solutions
Manganese Ore Processing Plant
Manganese is an important metal widely distributed in the natural world, and it exists in almost all types of ores and silicate rocks. Manganese is widely used in various fields of modern industry.
The common manganese ore type are oxide manganese and manganese carbonate.
Oxide manganese ore: It is secondary manganese oxide ore from weathered ore deposits. Oxide manganese usually adopts washing and gravity separation solutions for beneficiation. Weathering-type manganese oxide ore often contains a large amount of mud and powder ore, so it needs to be washed by trommel washer and then separated the manganese by a jig separator or shaking table to obtain manganese concentrate.
Manganese carbonate ore: In sedimentary manganese carbonate ore, the manganese minerals consist of rhodochrosite, calcium rhodochrosite, manganese containing calcite, and rhodochrosite. The embedded particle size of manganese minerals is about a few micrometers, which is difficult to dissociate and makes it difficult to obtain higher concentrate grades.
Process Description
Gravity separation
Ore washing>- screening>- crushing>-jig separator for separating particles size larger than 2mm/shaking table or spiral chute for separating particles under 2mm.
The gravity separation solution is only suitable for processing manganese ores with coarse embedded particles with simple structures, especially for dense oxidized ores. When using gravity separation solutions to treat oxidized manganese ore, crush the rock ore to around 6-10mm and separate the minerals. The coarse grade separation will use a jig separator. The fine-grade separation process will use a shaking table or spiral chute. It usually uses a 6s-type shaking table.
Gravity and magnetic separation
Manganese minerals belong to weak magnetic minerals, and using a strong-magnetic separator will improve the grade of manganese ore by 4% -10%. The magnetic separator will improve the manganese concentrate’s grade by 24% -25%. It has the advantages of easy control, simple operation, strong adaptability, and strong magnetic separation. Based on this, it is suitable for separating various manganese ores. Therefore, in recent years, strong-magnetic separation has occupied an important position in manganese ore beneficiation.
The combining magnetic and gravity separation is widely used for manganese oxide ore beneficiation. The crushed and qualified manganese ore enters a magnetic separator for strong magnetic separation to obtain weak magnetic separation tailings and strong-magnetic manganese concentrate. The tailings are transported to a strong-magnetic separator to separate the concentrate and tailings. After the concentrate goes through gravity separation to get manganese concentrate and tailings.
Related Case
JXSC company has built a 50T/H Manganese Ore Processing Plant in Kenya.
Details include below:
Mining & beneficiation solution consultation at the beginning.
Design processing flowchart.
Providing complete set processing equipment.
Providing foundation drawing after order
Providing technical guidance for plant installation.
Manganese ore conditions:
The manganese ore is rock type with clay, maximum input size 100mm, manganese concentrates size is 0-25mm, the Mn grade in raw ore is around 18%, Fe2O3 accounts for 10% to 15%, SiO2 accounts for 25% to 35%. So it needs to wash and screen out over 25mm materials to crush to smaller than 25mm, then use the gravity separation and magnetic separation method to remove Fe and Si from raw ore to improve Mn grade and meet the customer’s requirement.
Therefore, JXSC company has designed the most effective beneficiation flowchart according to these ore conditions.
The process is as follows:
The wheel loader feeds raw ore to the hopper, through a vibrating feeder evenly sends the ore to a belt conveyor, then to a trommel scrubber for washing clay and screening out materials over 25mm, 0-5mm, 5-25mm.
Over 25mm materials go to the jaw crusher to crush to a smaller size, then go to a vibrating screen for sieving out 0-5mm,5-25mm, and above 25mm material go back to the jaw crusher for crushing. The 5-25mm material goes to a jig machine for gravity separation and separates Mn concentrate. For 0-5mm material, it will be sent to another jig for gravity separation out of Mn concentrate by a slurry pump.
0-5mm and 5-25mm materials of trommel scrubber separately go to different jig machines for gravity separation out Mn concentrate.
The 0-5mm Mn concentrate from the jig machine enters a magnetic separator to remove impurities. The MN concentrate finally goes to a dewatering screen for dehydration.