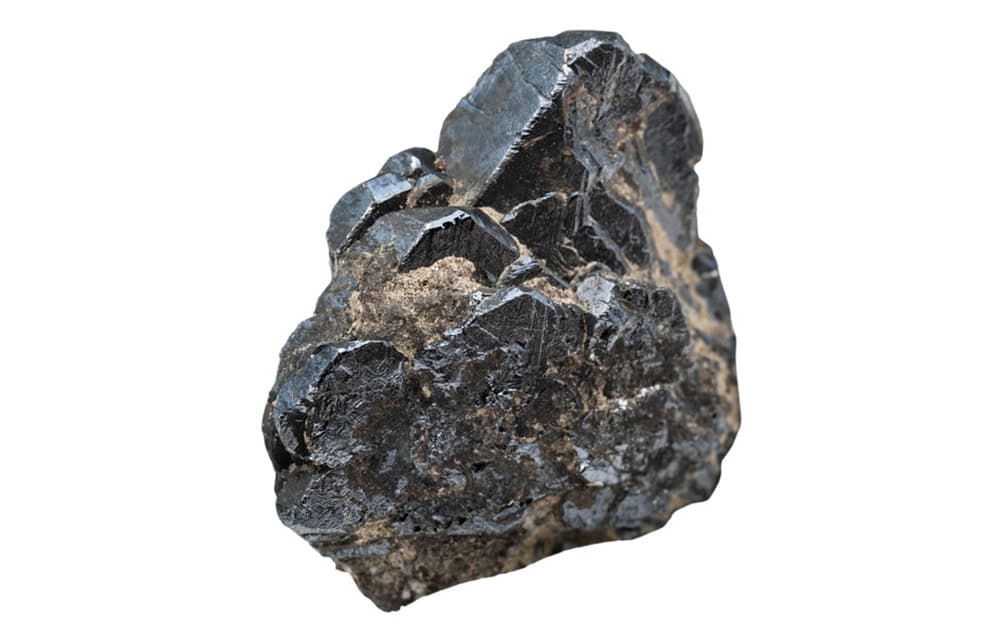
Iron ore is a key raw material for refining iron and is widely used in steel production. Ilmenite is an important source ore of iron.
The main components of ilmenite are titanium oxide (TiO₂) and iron oxide (FeO), and its chemical formula is FeTiO₃. The ore is usually black or dark gray, has a metallic luster, and is relatively hard. Ilmenite has a large density, usually between 4.5-5.0 g/cm³, and has good high temperature resistance, which makes it perform well in high-temperature smelting processes.
Ilmenite mostly exists in the form of sedimentary rocks and is common in igneous rocks and metamorphic rocks. It often appears with other minerals such as zircon, feldspar and quartz, which brings many challenges to the beneficiation of ilmenite.
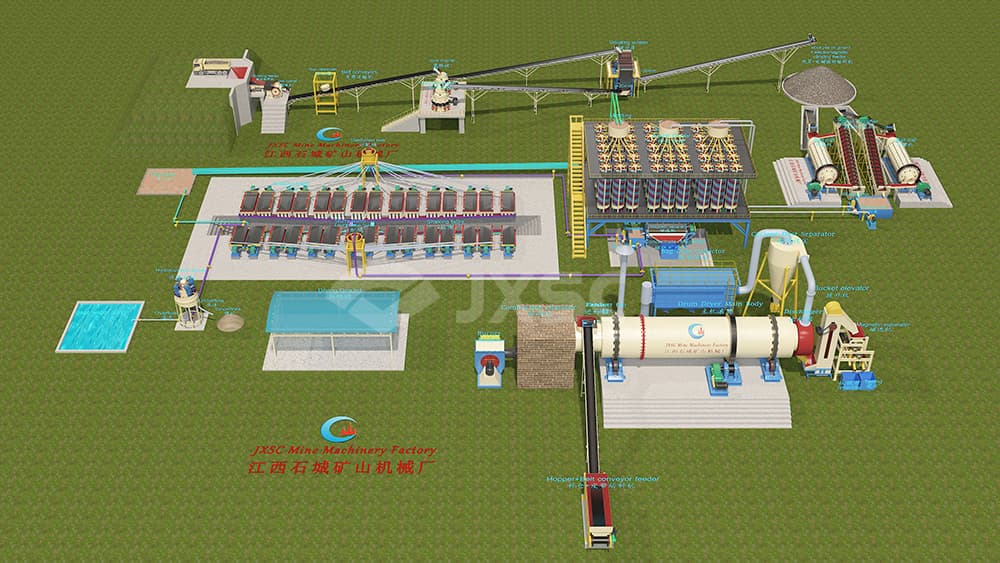
Overview of the Ilmenite Processing Plant
The 100TPH Ilmenite Processing Plant is designed for efficient rock ilmenite ore processing. It includes a series of stages: raw material feeding, primary crushing, fine crushing, screening, ball mill grinding, gravity separation, wet magnetic separation, hydro cyclone, drying, and dry magnetic separation. This comprehensive setup ensures the effective separation and upgrading of ilmenite concentrate.
Raw Material Feeding
The ilmenite ore is fed to the primary jaw crusher using a vibration feeder. This feeder allows for smooth and even feeding of rock ore, equipped with a grizzly bar that screens out oversized material before directing it to the primary jaw crusher.
Iron Ore Crushing
The primary jaw crusher reduces the size of the rock ore. The output material is then sent to a cone crusher, which crushes the ore to below 20 mm. Oversized material larger than 20 mm is screened out and sent back for further crushing. The crushed material (0-20 mm) is stored before proceeding to the next stage.
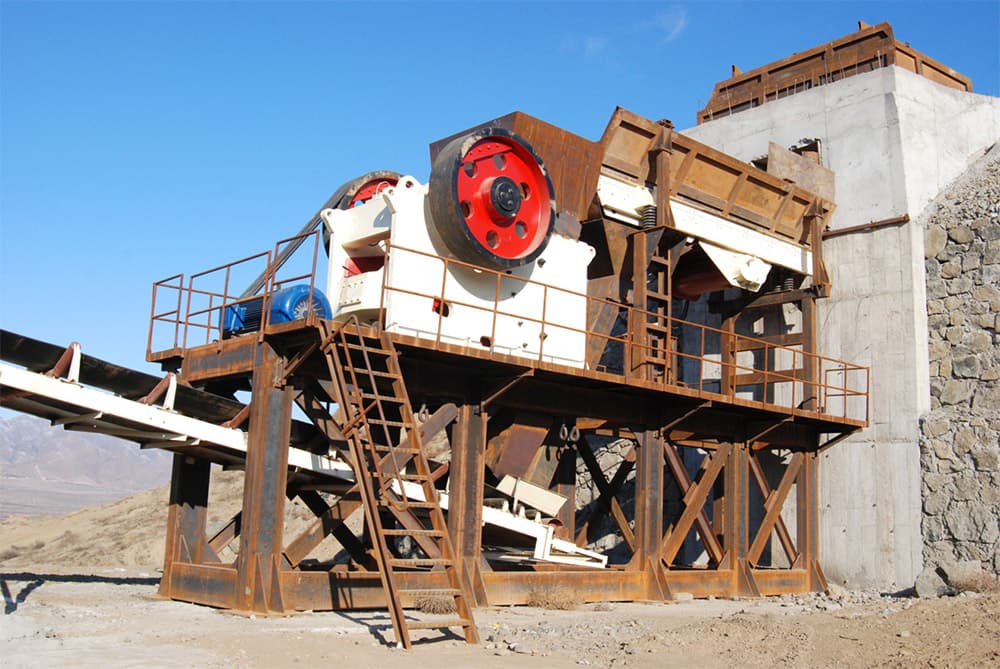
Gravity Separation
The 200 mesh slurry is pumped to a gravity separation machine, which includes a spiral chute and shaking table. The spiral chute performs primary concentration, and to maximize titanium recovery, a two-stage spiral chute separation is employed. Middling material from the first stage is sent to the second stage for further recovery.
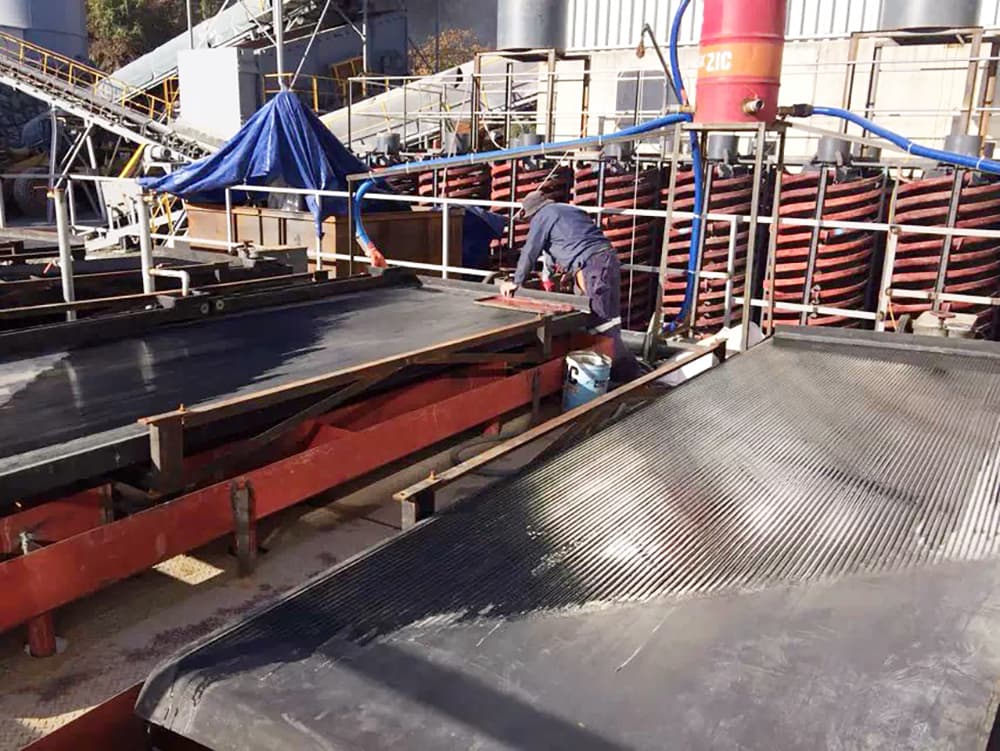
Wet Magnetic Separation
All heavy concentrate ore from both stages of the spiral group is directed to a wet magnetic separator. This step removes magnetite and mechanical iron, improving the quality of the concentrate.
Concentration and Dewatering
The concentrate from the wet magnetic separator is then sent to a shaking table for additional concentration. The resulting concentrate is pumped to a hydrocyclone for dewatering before proceeding to the drying stage.
Drying and Magnetic Separation
The dried ilmenite concentrate is processed through a dry magnetic separator to achieve the highest possible grade of ilmenite concentrate.
In summary, the iron ore dressing line is a complex and systematic project. Through the coordinated operation of various links, iron ore can be processed into high-quality iron ore concentrate, providing strong support for the development of the steel industry. At the same time, reasonable tailings treatment also helps to achieve sustainable utilization of resources and environmental protection.
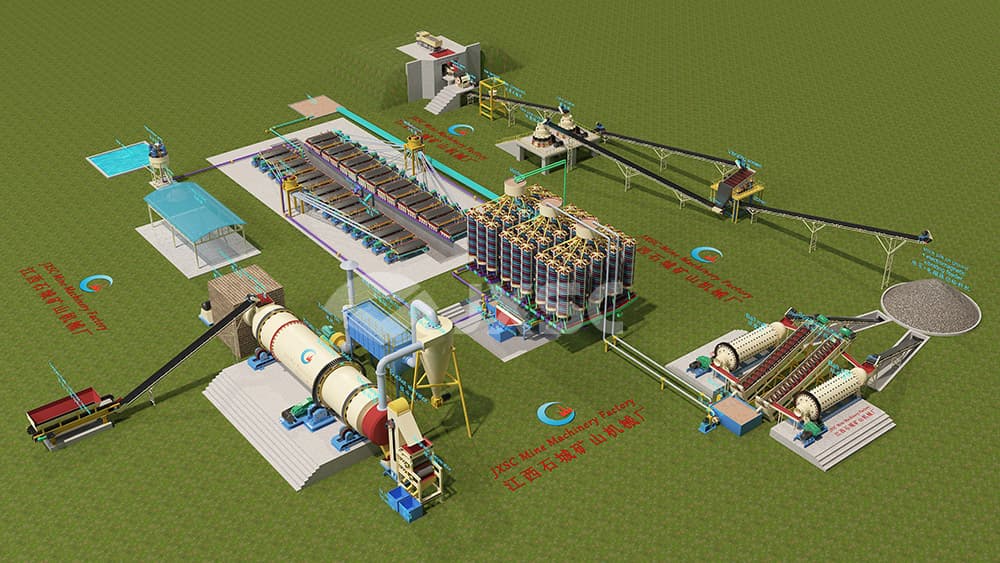
JXSC has 38 years of experience in the mining industry, and many experienced engineers provide professional technical support to customers. We focus on providing turnkey solutions and full equipment sales services for mining. Over the years, we have served hundreds of customers at home and abroad. Please send us your mining information. JXSC can provide more accurate suggestions based on your specific situation.
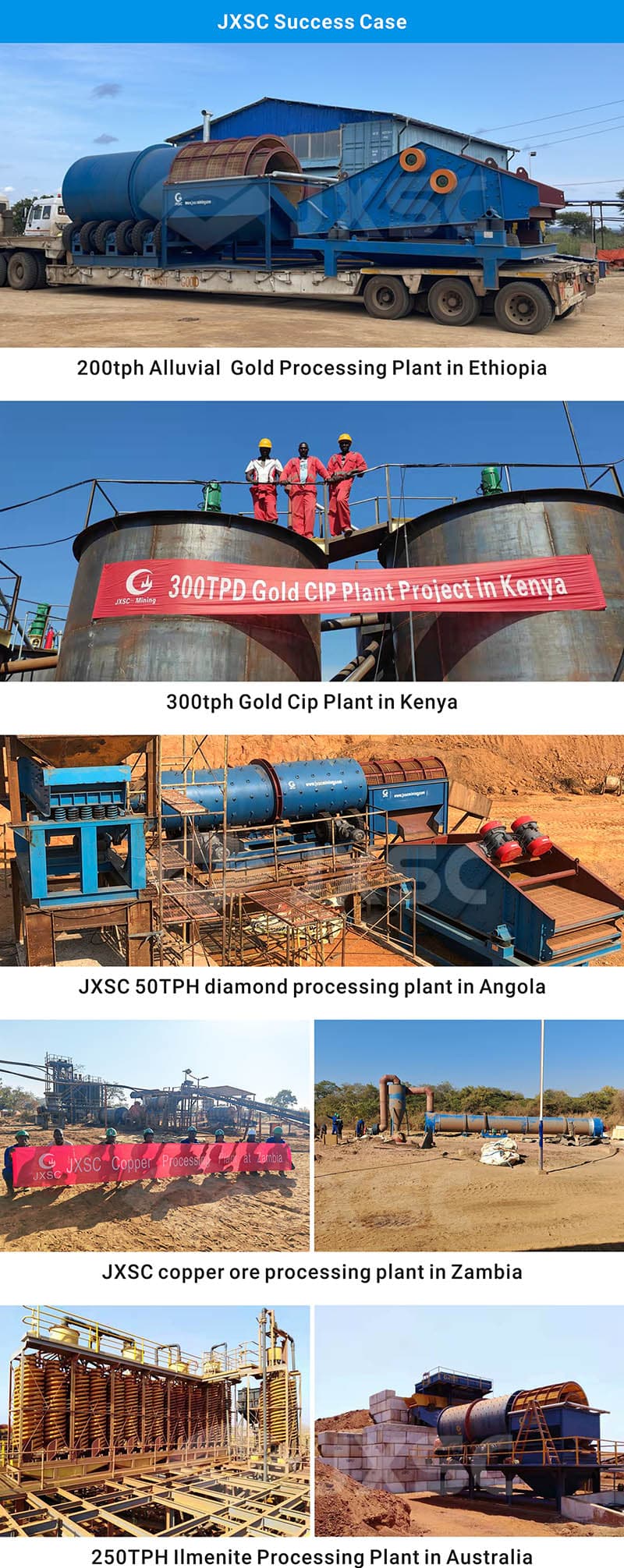