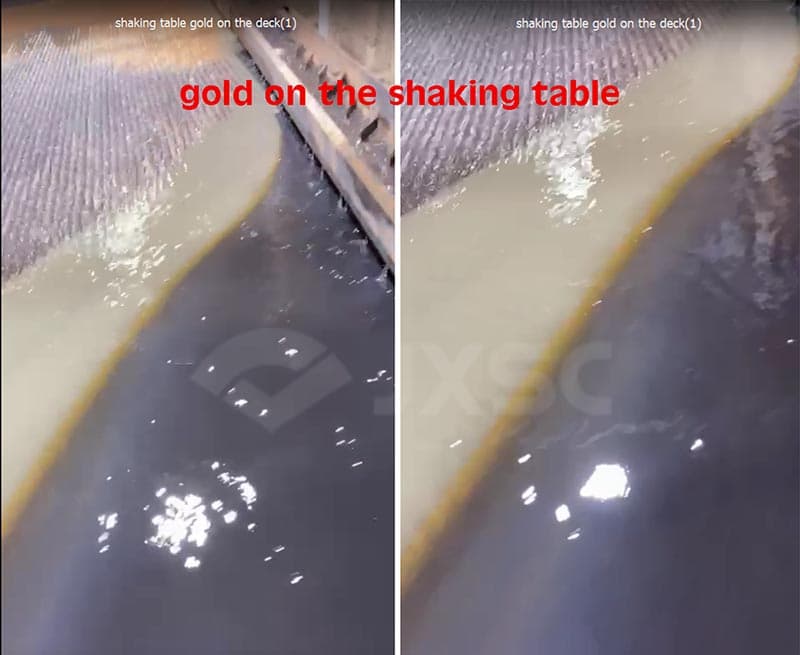
The shaker table is a gravity separation device that separates target minerals by taking advantage of the density differences of different minerals. The shaker table can be used for both roughing and concentrating minerals. It is a mineral processing device with a simple structure and low cost. During the mineral processing process, only water needs to be added, causing no pollution to the environment, making it highly environmentally friendly. It is widely used in the separation of gold, tin, tungsten, zinc, tantalum, niobium, iron, manganese, titanium iron, coal, etc.
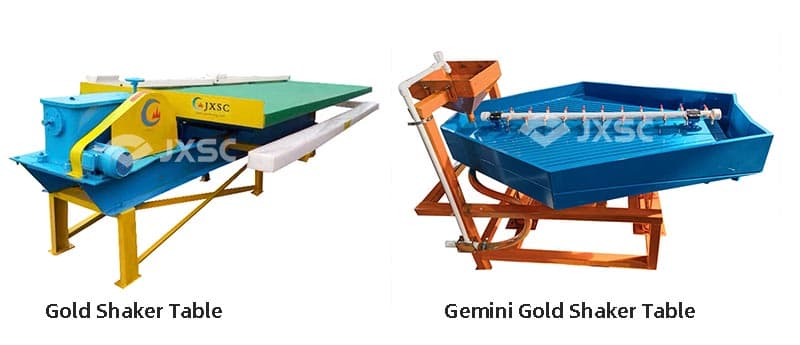
Several common types of gold mining shaker tables
1. 6S Gold Shaker Table
The structural form of the 6S gold shaker table in mineral processing evolved from the early Wilfley shaker table and has been improved. It features an eccentric connecting rod type headstock and a fixed-axis slope adjustment mechanism. The supporting device and slope adjustment mechanism of the tabletop are both installed on the frame. The tabletop is supported by four plate-shaped rockers. This type of support enables the tabletop to perform an arc-shaped reciprocating motion in the vertical plane, accompanied by a slight vibration. When the rocker is slightly inclined towards the headstock end by approximately 4 – 5 degrees, the transportation and loosening effects of the particle groups on the tabletop are enhanced. Therefore, this shaker table is more suitable for processing coarse-grained ore sands. Depending on the groove pattern of the tabletop, it can be classified into coarse sand (46 grooves and 60 grooves), fine sand (90 grooves and 110 grooves), and slime (120 grooves and 138 grooves) types. The tabletop can be single-wave, double-curved wave, or table flotation types, made of fiberglass-reinforced plastic, and the frame can be selected from large or small channel steels.
2. Gemini Gold Shaker Table
The advantage of the gemini shaker table is that it can separate higher grade gold ores. Different from ordinary shaker tables, the washing water of the gemini shaker table flows onto the tabletop from the middle water pipe.
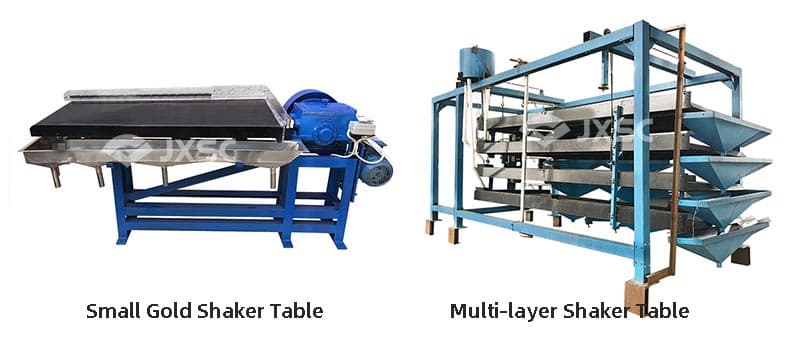
3. Small Gold Shaker Table / Lab Shaker Table
The laboratory shaker table is a small-scale shaker table. The overall size of the machine is smaller than that of the 6S shaker table, making it suitable for indoor use or for mineral processing tests. Although the tabletop is smaller, its mineral processing efficiency is comparable to that of ordinary shaker tables.
4. Multi-layer Shaker Table
To overcome the drawbacks of large floor space and low processing capacity of shaker tables, the multi-layer shaker table was developed. It is used for the separation of fine-grained coal. The transmission device and the tabletop are respectively suspended by steel wires on the metal support or the precast hooks of the building. The inertial force of the headstock is transmitted to the shaker table frame through a ball socket connector, enabling the tabletop and the headstock to move in tandem. The multi-layer shaker table increases the processing capacity of a single device and reduces the floor space occupied. It is an improved device based on ordinary shaker tables.
Working principle of gold mining shaker table
During the shaking table sorting process, washing water is fed into the water trough to form a thin layer of water flow on the inclined bed surface, and the slurry flows to the bed surface through the ore feeding trough. The slurry forms a fan-shaped distribution under the vibration and gravity of the shaking table. At this time, particles of different densities are stratified under the turbulent disturbance caused by the vibration: high-density minerals sink to the bottom layer of the bed surface, and low-density minerals are suspended on the surface. Subsequently, the water flow gradient generated by the lateral inclination of the table surface and the longitudinal asymmetric vibration form a synergistic effect-when the stratified mineral particles move to the tailings end, the slurry raw water from the ore feeding trough and the washing water added to the side of the table surface jointly form a lateral flushing water flow, which peels off the surface light minerals layer by layer from top to bottom.
As the outward inclination angle of the table surface gradually increases from the top to the bottom, the peeling strength of the lateral water flow increases synchronously: when approaching the top, only loose particles on the surface are taken away, while when approaching the end, it can penetrate deeper materials. Finally, after multi-level stratification and continuous flushing, only a single layer of dense heavy mineral particles remains at the end of the table, and the concentrate is collected in an extremely thin layer (about 1-2 particles thick), and the remaining low-grade minerals are discharged with the water to form tailings.
Heavy minerals have a smaller lateral velocity and a larger longitudinal velocity, and light minerals have a larger lateral velocity and a smaller longitudinal velocity. Applying the parallelogram law to synthesize the longitudinal and lateral velocities, it can be seen that the combined velocity of heavy minerals is biased toward the concentrate discharge end of the shaker, and the light minerals are biased toward the tailings side of the shaker. Medium-density particles are located between the two. This process is called “transportation zoning”.
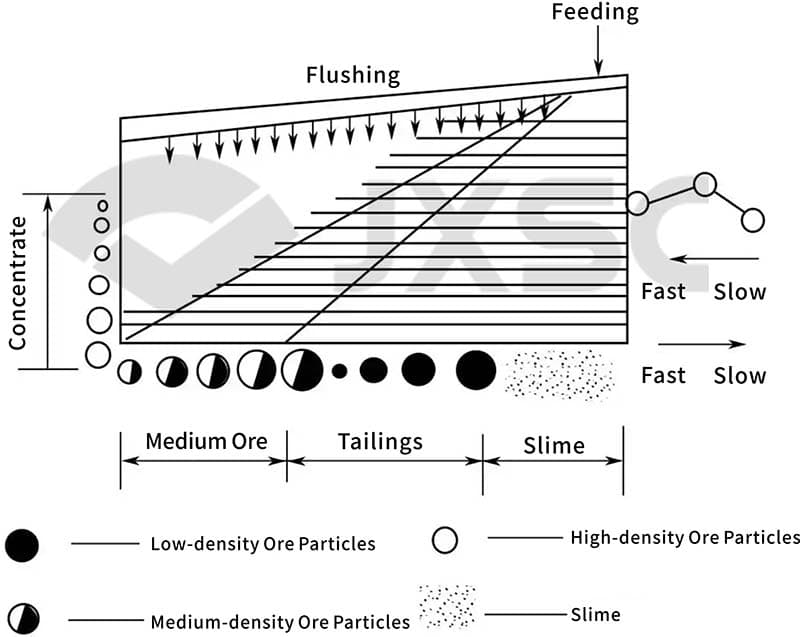
Notes on use
he efficiency of the shaker depends on many factors, including the characteristics of the slurry, the speed of the shaker, the inclination, and the amount of flushing water. By adjusting these parameters, the gold recovery rate can be improved.
1. Accurate control of feeding parameters
Feeding concentration: The optimal range is 15%~30%. The concentration of coarse-grained ore (such as wolframite) can be appropriately increased (25%~30%), and the concentration of fine-grained ore needs to be reduced (15%~20%). Too high a concentration will lead to poor slurry fluidity and difficulty in stratification; too low a concentration will cause the fine-grained concentrate to be easily lost.
Feeding particle size: pre-classification, uniform packaging particle size. However, when the feed particle size range is too large or exceeds the processing particle size of the shaking table, it is easy to lose concentrate or mix too many impurities in the gold ore.
2. Stable feeding
It is very important to ensure the stability of the feed amount during the operation of the shaking table. When the feed amount is reduced, gold may be mistakenly discharged to the tailings end; excessive feeding will cause impurities to mix into the concentrate. Stable water-solid ratio (such as 25%~30%) and bed thickness are the key to achieving efficient stratification. Feed fluctuations will change the bed thickness distribution, destroy the synergistic effect of water flow flushing, and reduce the separation accuracy of gold particles and impurities.
3. Optimal matching of stroke and frequency
Coarse-grained ore: large stroke (16~30mm) combined with low frequency (200~250 times/min) to enhance the looseness of the bed.
Fine-grained ore: small stroke (8~10mm) combined with high frequency (250~300 times/min) to improve sorting accuracy.
The stroke frequency can be changed by adjusting the toggle plate position of the transmission mechanism or the motor pulley. For example, the YS type shaking table can change the T-head position by adjusting the screw rod to ensure that the ore particles are fully layered and the longitudinal movement is stable.
4. Slope selection
When handling materials of different particle sizes, the slope of the bed surface is the key. When handling fine-grained materials, a large slope will cause the concentrate to be discharged into the tailings. Therefore, when handling fine-grained materials, the slope is suitable to be smaller (1°~2°). Similarly, when handling coarse-grained ore particles, the slope is suitable to be larger (3°~4°). The slope and water addition need to be adjusted in reverse: a large slope reduces the amount of water, and a small slope increases the amount of water. Use the slope adjustment hand wheel to adjust the horizontal slope, and adjust the flushing water distribution through the water diversion valve to ensure that the water flow evenly covers the bed surface to avoid insufficient or excessive local flushing.
5. Equipment maintenance
Maintenance points: Regularly replace worn springs and pull rods, check whether the bed surface is scaled or oxidized, and use resin fillers to repair damaged surfaces.
Rinse the bed surface thoroughly during shutdown to prevent impurities from depositing.
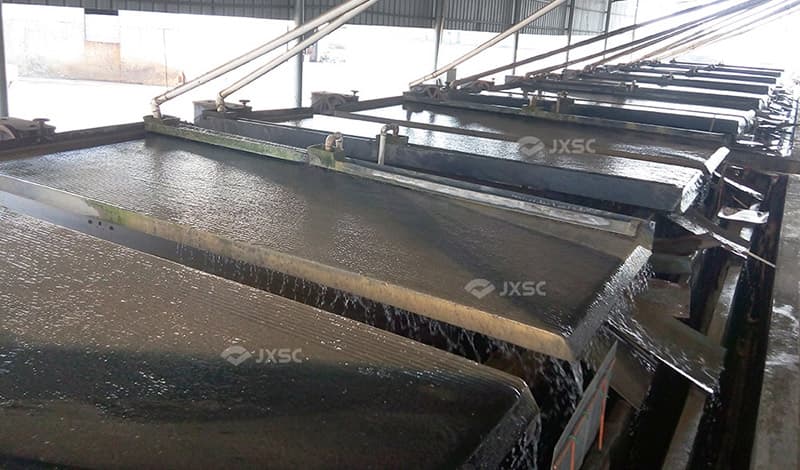
FAQ
1. Dry spots appear on the table surface
Answer: Use your hands or a brush to guide the water flow to a dry area; use a degreasing detergent for deep cleaning to eliminate grease deposits.
2. Impurity minerals are mixed into the concentrate collection tank
Answer: Increase the flushing water flow and simultaneously reduce the vibration intensity of the shaking table; calibrate the longitudinal horizontality of the equipment base.
3. Suspension of flake precious metals leads to tailings loss
Answer: Comprehensively check the tightness of the equipment support structure; Adjust the opening of the front water supply valve to reduce the overflow water volume; Reduce the feeding speed; Re-check the reciprocating motion parameter configuration.
4. Uneven distribution of slurry
Answer: Check the vertical alignment between the discharge port and the table; dilute the slurry with water.
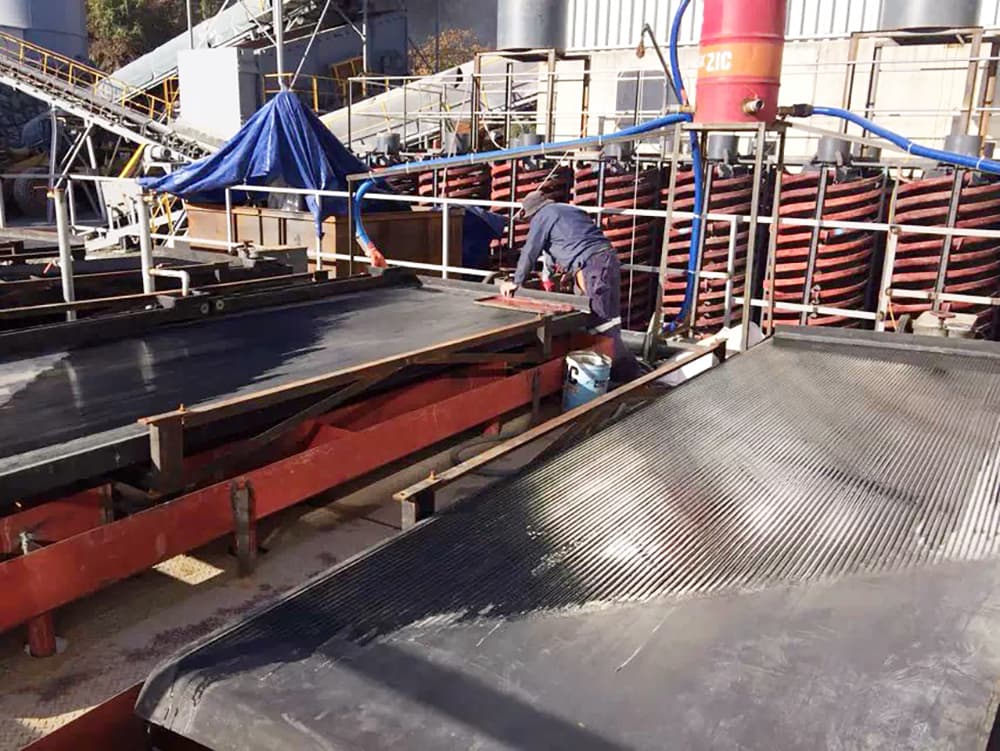
JXSC has 38 years of experience in the mining industry, and many experienced engineers provide professional technical support to customers. We focus on providing turnkey solutions and full equipment sales services for mining. Over the years, we have served hundreds of customers at home and abroad. Please send us your mining information. JXSC can provide more accurate suggestions based on your specific situation.
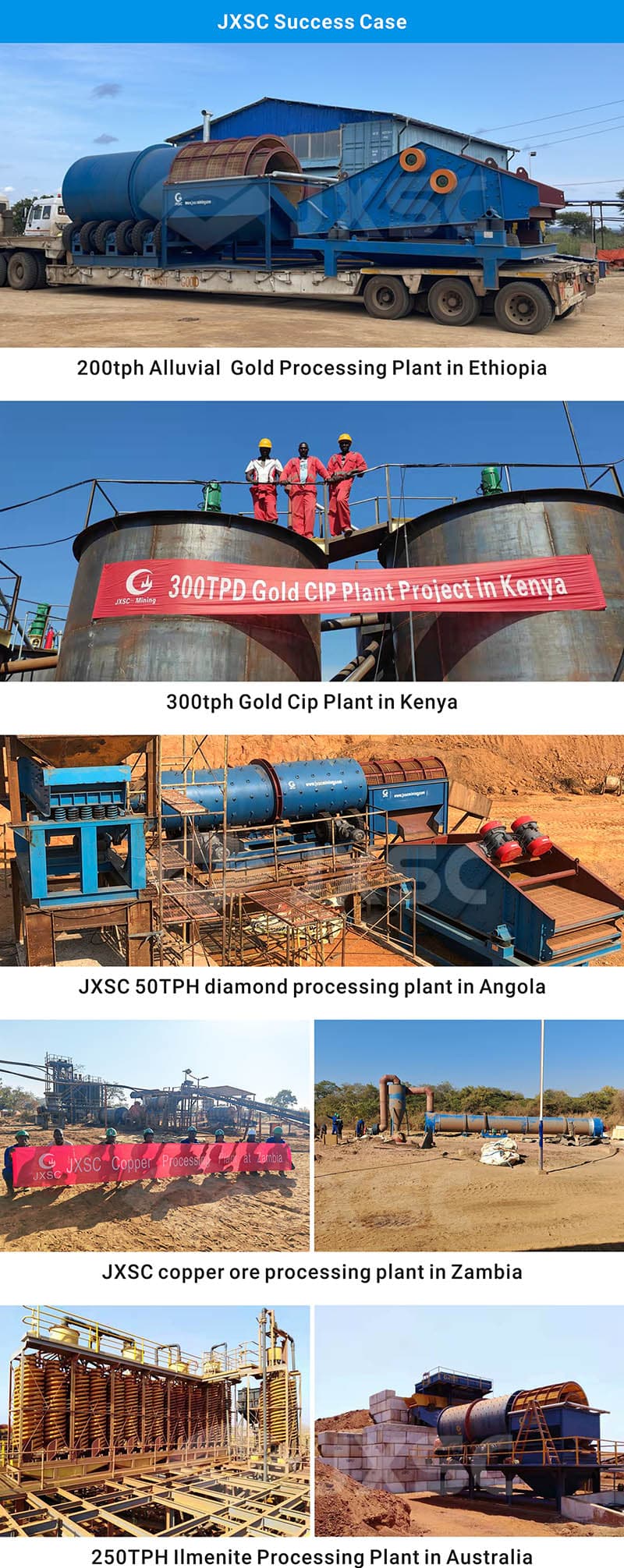