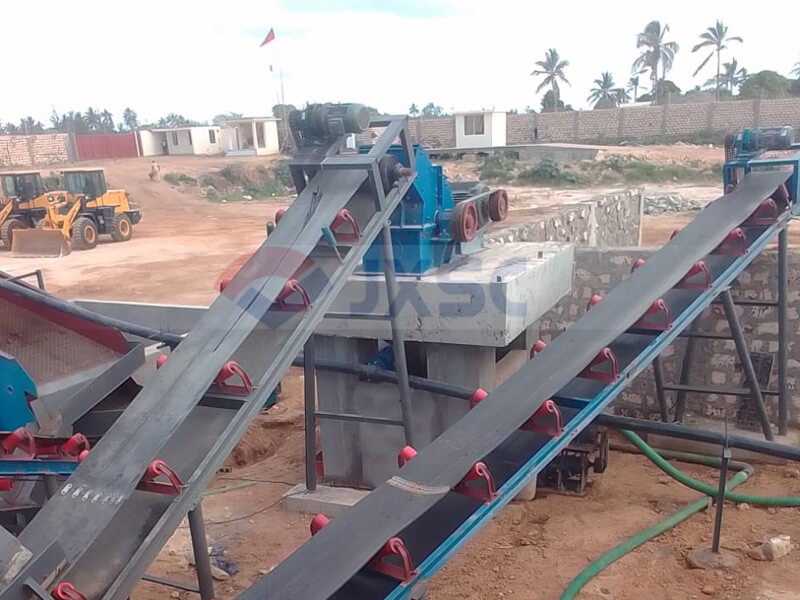
Are you struggling to set up an efficient manganese processing plant? We know how challenging it can be to start a manganese processing plant. The process involves many steps and requires careful planning. Many companies face delays, budget overruns, and inefficient setups because they miss key details. With the explosive growth of electric vehicles and renewable energy, manganese is a key component of lithium battery cathode materials. The global demand for new energy batteries has skyrocketed, and 90% of manganese ore eventually flows to the industry. How can we build an efficient manganese processing plant? The following five steps can help you solve it!
To set up a successful manganese processing plant, follow these five steps: mineral testing, process design, equipment selection, plant layout, and production commissioning. Each step is not only to avoid risks, but also to maximize efficient and cost-effective operations.
Table of Contents
Manganese Processing Plant Steps
1. First Step Of Manganese Plant: Mineral Testing
Mineral testing provides critical data on ore grade, mineral composition, and impurities. Before investing in infrastructure or equipment, thorough testing helps you understand the ore’s chemical composition, manganese content (grade), and the presence of impurities such as iron, silica, or phosphorus. Advanced techniques like X-ray fluorescence (XRF), chemical analysis, and metallurgical testing are employed to evaluate the ore’s suitability for processing. This data informs decisions on ore beneficiation methods, equipment selection, and plant design, ensuring optimal recovery rates and minimizing waste.
Skipping this step risks inefficiencies, higher operational costs, and potential project failure. By prioritizing mineral testing, you lay the groundwork for a cost-effective, sustainable, and profitable manganese processing operation.
Mineral Testing Key Processes
Test Type | Purpose |
Chemical Analysis | Determines manganese content and impurities |
Density Analysis | Measures ore density for gravity concentration |
Magnetic Properties | Checks if magnetic separation is possible |
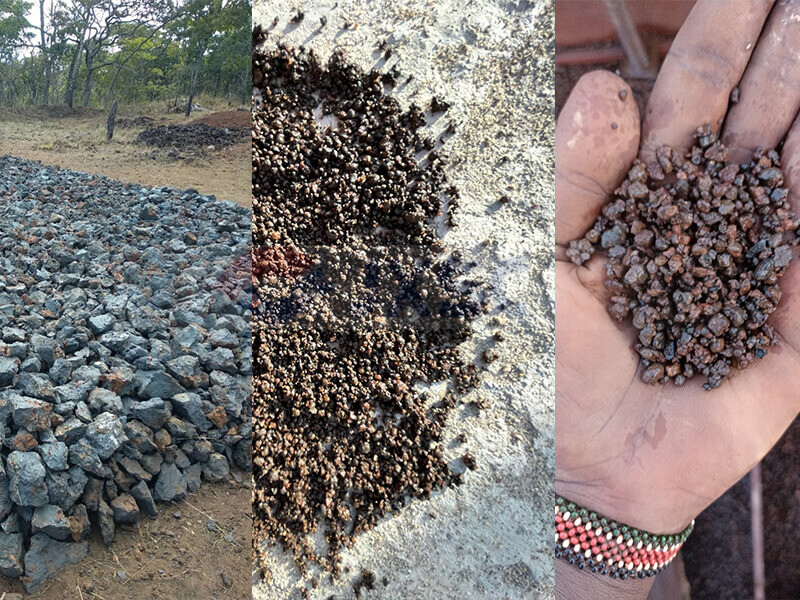
Without accurate test results, your plant design may fail to process the ore properly. Always work with a reliable lab for your mineral testing. Specific mineral processing testing services can be customized based on your ore information and needs. If you need more details, please contact professional engineers.
2. Second step of Manganese Plant: design right process flow
The processing flow determines how your plant will operate. A good design ensures high recovery rates and low operating costs. Once mineral testing confirms the viability of the manganese ore, the next critical stage is to design an efficient process flow. This step transforms the raw data from the testing into a customized production line. A well-designed process flow ensures optimal resource utilization and maximizes manganese recovery. The ideal manganese processing flow includes crushing, screening, washing, gravity separation, and magnetic separation. A poorly designed process flow can lead to inefficiency, increased costs, waste of resources, or failure to meet quality standards. JXSC will do this by prioritizing customized, data-driven process design, with each stage tailored to your specific ore type.
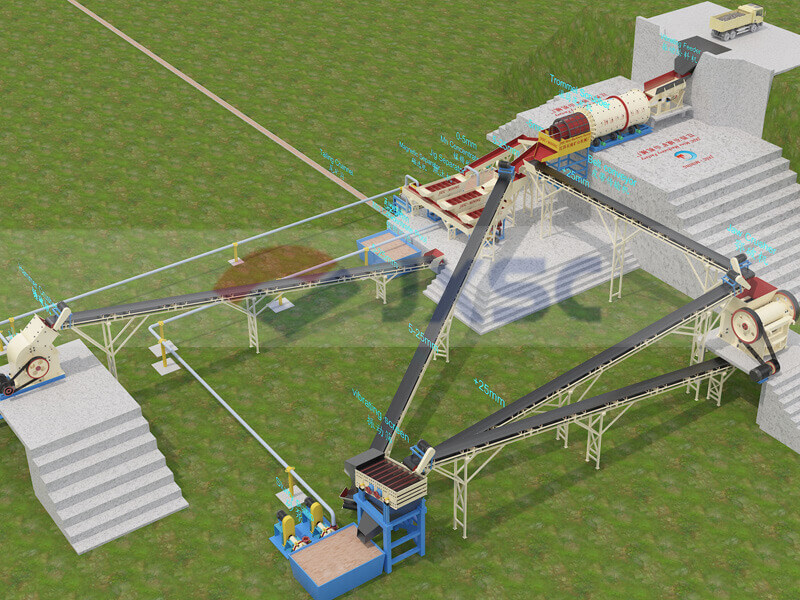
Your ore type will affect your process design. Some ores need additional steps like gravity concentration or flotation. Always consult a mineral processing expert before finalizing your design.
3. Third Step Of Manganese Plant: Select equipment
After determining a clear manganese ore process flow, the next critical step is to select the right equipment based on your manganese ore characteristics and processing goals. The efficiency, durability and cost-effectiveness of your plant all depend on this decision.
- Crushing and grinding machinery: jaw crushers, cone crushers, ball mills, etc.
- Screening systems: vibrating screen (customizable mesh size, vibration intensity).
- Beneficiation machine: magnetic separators, flotation cells, etc.
- Dewatering machine: dewatering screen, filter press, etc.
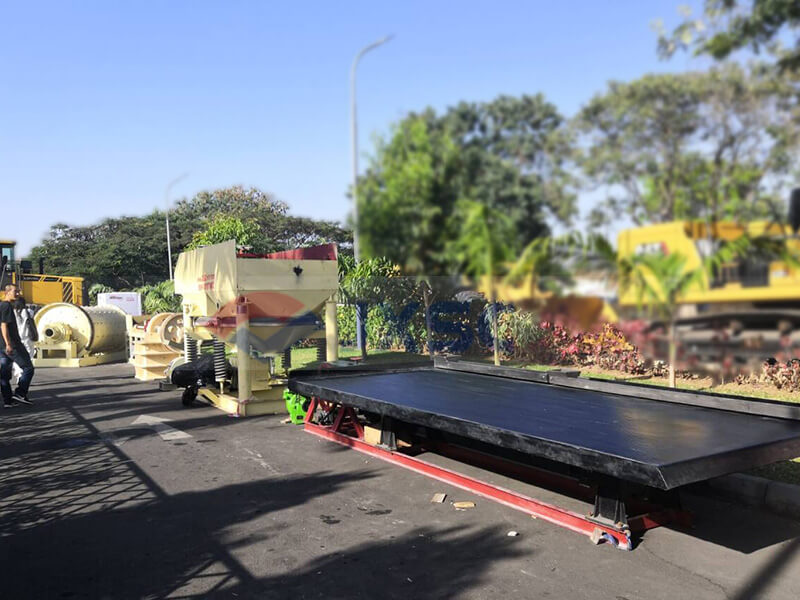
Consider the following factors:
-Production scale: Choose the right equipment size based on the target output to avoid underutilization or bottlenecks.
-Energy efficiency and automation: Modern energy-saving technologies can reduce operating costs and improve precision.
-Maintenance and spare parts: Give priority to machinery that is rugged, easy to maintain, and backed by reliable suppliers.
Ignoring this step can result in machinery mismatch, production delays, or inflated operating expenses. High-quality equipment reduces downtime and increases productivity. Always choose reliable brands with good after-sales support. By strategically selecting equipment, you can ensure seamless integration into your plant’s workflow, laying the foundation for stable output, minimal downtime, and long-term profitability.
4. Fourth Step Of Manganese Plant: Plant Layout
The plant layout is the cornerstone of efficient operation of manganese processing plants, directly affecting production fluency, safety and cost control. It is necessary to coordinate space, logistics and functional zoning based on process flow and equipment characteristics.
- Process orientation: Arrange equipment in a straight line or U-shape according to the processing sequence (washing → crushing → grinding → sorting → smelting) to shorten the material transportation distance. For example, placing the ball mill close to the downstream of the crusher to avoid complicated and circuitous belt conveyors can reduce energy consumption by 10%-15%.
- Functional zoning: Divide the raw material yard, production area (including wet/fire process workshop), storage area, wastewater treatment area and office area to ensure that dangerous operations (such as high-temperature smelting) are away from crowded areas, and emergency passages are reserved.
- Logistics route: Design a one-way logistics route to avoid cross-interference of forklifts and conveyor belts; the height and capacity of the silo must match the equipment processing capacity to prevent blockage or empty load.
- Expansion reservation: reserve space for fire passages and equipment maintenance, and reserve 20%-30% space for future capacity increase or process upgrade, such as adding a new flotation group or tailings pond expansion area.
Unreasonable layout can easily lead to storage areas far away from production lines, safety hazards and surge in transformation costs. Scientific planning requires the coordination of production processes, logistics routes, field surveys and expansion needs to avoid resource waste and operational risks, ensure efficient coordination of people, machines and materials, and provide the greatest convenience and benefits for stable production and long-term development.
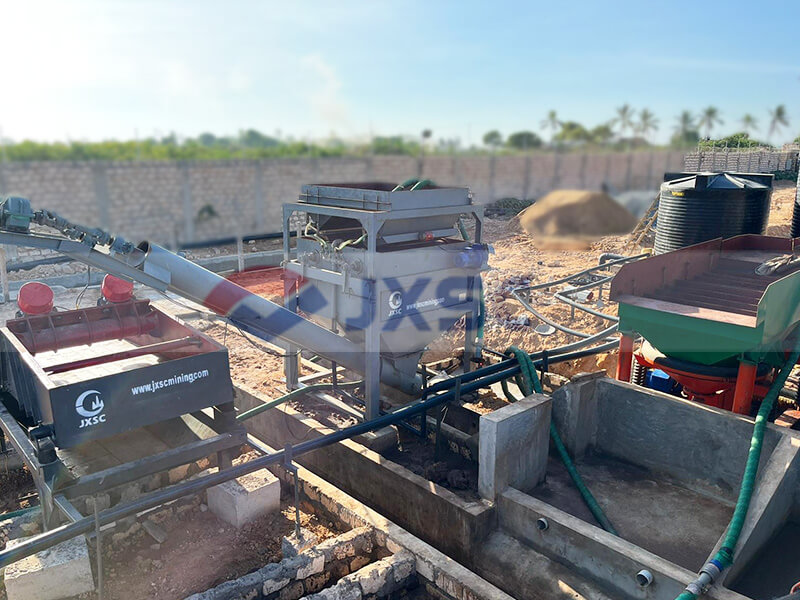
5. Fourth Step Of Manganese Plant: Production Commissioning
After completing the equipment selection and process layout, production commissioning aims to verify the synergy of equipment, process and control to ensure stable operation of the entire process.
- Single machine no-load test: Start the equipment one by one (such as crusher, ball mill, magnetic separator), check the motor direction, bearing temperature, vibration and other parameters, and eliminate installation errors.
- Linkage no-load operation: Connect the equipment in series according to the process flow, test the interlocking control of the conveyor belt, valve, and sensor, and ensure that the start and stop sequence is correct.
- Material test run: Feed in batches (gradually increase from low load to full load) to monitor the matching degree between the processing capacity of each link and the actual working conditions. For example, verify whether the particle size of the ball mill discharge meets the standard, or whether the reaction time of the leaching tank is reasonable.
- Process parameter optimization: According to the trial production data (such as manganese recovery rate, energy consumption, impurity content), fine-tune the equipment parameters (speed, reagent addition, temperature) until the output meets the target specifications.
Before commissioning, it is necessary to complete safety training for all employees, equip emergency equipment such as fire extinguishers and eye washers, and formulate emergency shutdown plans for sudden failures to ensure safe operation to the greatest extent. If the problems exposed during the debugging phase are not resolved, frequent shutdowns or quality fluctuations will occur after the official launch. Systematic debugging can shorten the production cycle, reduce long-term operation and maintenance costs, and lay the foundation for efficient production.
This stage requires systematic management, technical optimization, and risk prevention to avoid shutdowns, delays, or quality fluctuations and ensure stable output of production capacity and benefits.
Conclusion
The above five steps are to set up an efficient manganese processing plant. Start with mineral testing, then design your process flow, select the right equipment, plan the layout, and production commissioning. Mineral testing lays the data foundation for the project, process design and equipment selection ensure technical feasibility, and plant layout and production commissioning open up the last step from blueprint to actual production capacity. This approach will save time and money while ensuring long-term success. JXSC has a 40+ years technical team that will help you set up a manganese processing plant with maximum recovery rate.