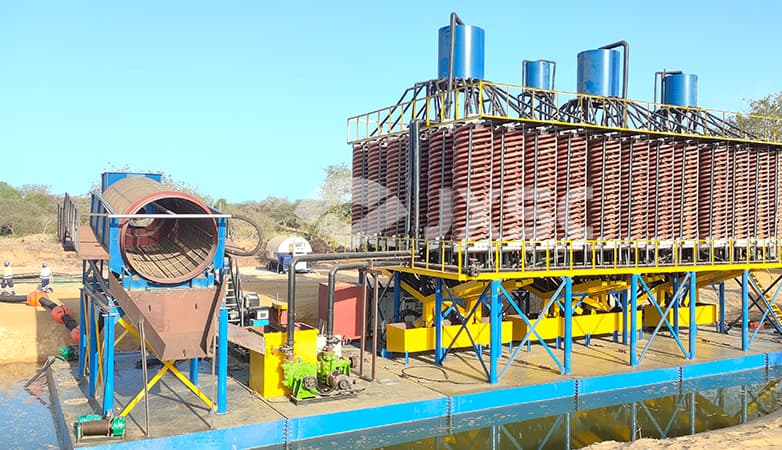
Beach sand deposits, rich in strategic minerals such as ilmenite, zircon, rutile, and rare-earth minerals (e.g., monazite), serve as critical raw materials for modern industries. However, the complex mineral composition and significant variations in physical properties pose substantial challenges to beneficiation processes. This article systematically analyzes the beneficiation methods and technological optimization strategies for beach sand, focusing on mineral characteristics and separation challenges.
1. Mineral Characteristics and Separation Challenges of Beach Sand
Typical beach sand contains 40–60% ilmenite, 5–15% zircon, 2–8% rutile, and associated rare-earth minerals like monazite and xenotime. The particle size of these minerals predominantly ranges from 0.1–0.3 mm, with a liberation degree exceeding 85%, which favors gravity separation. However, significant differences in physical properties complicate the process:
- Density variations: Ilmenite (4.7 g/cm³) contrasts sharply with quartz (2.65 g/cm³).
- Magnetic susceptibility gradients: Ilmenite has a specific magnetic susceptibility of 38×10⁻⁶ cm³/g, while monazite reaches 180×10⁻⁶ cm³/g.
Key separation challenges include:
- Fine-particle slime loss: Particles smaller than 0.1 mm tend to slime, reducing recovery rates.
- Magnetic overlap interference: Minerals like monazite and ilmenite exhibit overlapping magnetic susceptibility ranges, hindering selective magnetic separation.
- Complex rare-earth mineral associations: Monazite often coexists with ilmenite and displays variable magnetic properties, necessitating multi-stage separation for high-grade concentrates.
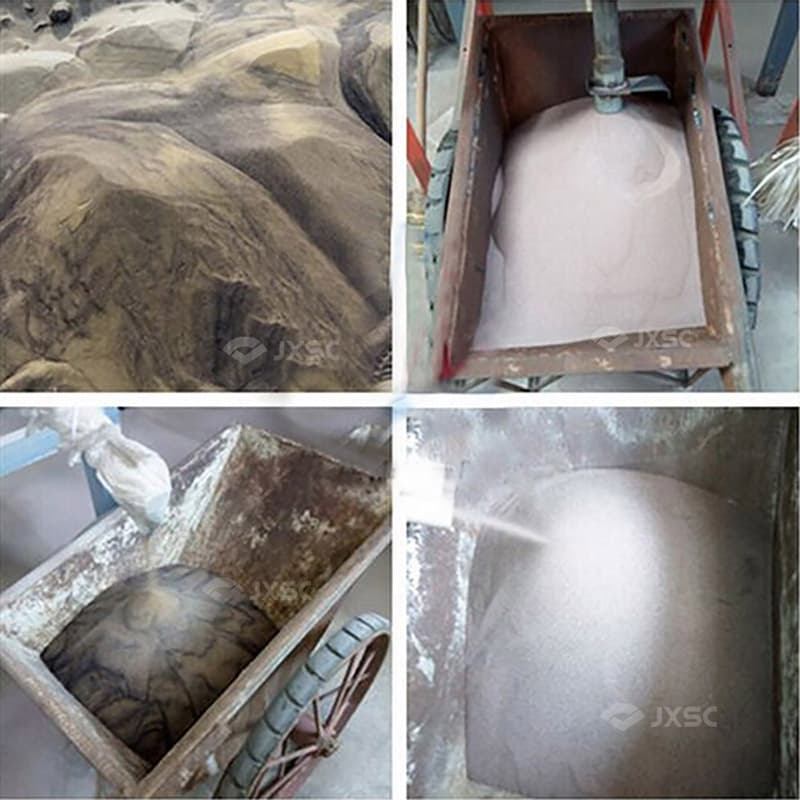
2. Core Advantages of Gravity-Magnetic Combined Processes
To address these challenges, the Gravity-Magnetic Combined Process has emerged as a mainstream solution, leveraging stepwise utilization of mineral property differences. The workflow comprises:
- Gravity Pre-concentration Stage
Spiral chutes or trapezoidal jigs exploit density differences for coarse particle enrichment. For example, a beach titanium sand operation achieved a TiO₂ grade increase from 4.2% to 12.3% using jigging, with a processing capacity of 5–8 tons per hour per unit. - Gradient Magnetic Separation Stage
- Low-intensity magnetic separation (0.3–0.5 T): Recovers strongly magnetic minerals (e.g., magnetite).
- Medium-intensity magnetic separation (0.8–1.2 T): Targets moderately magnetic minerals like ilmenite.
- High-intensity magnetic separation (>1.5 T): Captures weakly magnetic rare-earth minerals (e.g., monazite).
By adjusting magnetic field intensities, interference between minerals is minimized. In one case, this process yielded a titanium concentrate with 48.6% TiO₂ (82.3% recovery) and a zircon concentrate with 65.2% ZrO₂.
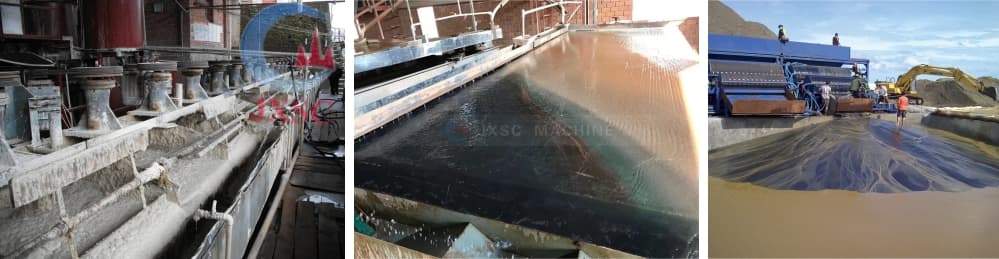
3. Process Optimization and Critical Control Parameters
Efficiency relies on precise control of key parameters:
- Grinding fineness: Maintain 60–65% passing 200 mesh to avoid over-grinding and slime formation.
- Feed pulp density: Optimize to 25–30% during gravity separation to ensure effective particle stratification.
- Magnetic separator gap adjustment: Dynamically adjust gaps (0.5–2 mm) to accommodate varying particle sizes.
Sustainable practices include:
- Water management: A closed-loop “sedimentation-filtration-reuse” system achieves >85% water recycling.
- Tailings utilization: Graded tailings are repurposed for construction materials, reducing environmental impact.
4. Challenges and Solutions for Rare-Earth Mineral Separation
Monazite recovery remains a critical challenge due to its overlapping magnetic and density properties with ilmenite. Conventional methods yield low-grade concentrates (70–75% recovery). Enhanced strategies include:
- Electrostatic separation: Separates conductive minerals (e.g., rutile) from non-conductive ones (e.g., zircon).
- Froth flotation: Uses selective reagents to enrich monazite or zircon, improving rare-earth recovery.
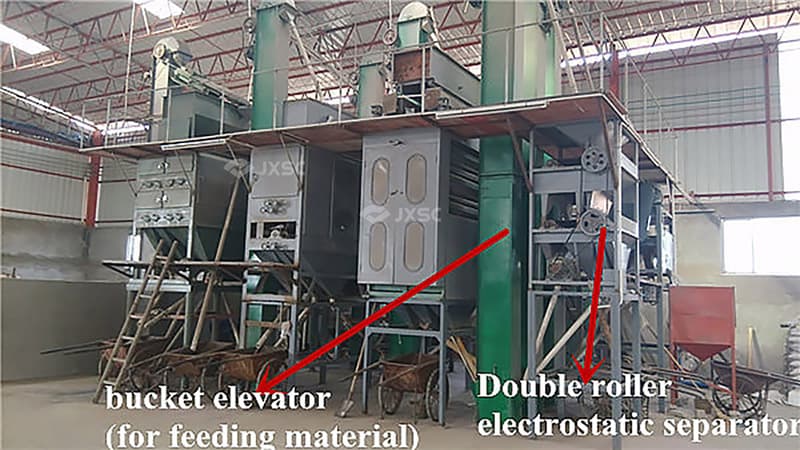
5. Environmental and Sustainability Considerations
Beach sand mining must balance resource extraction with ecological preservation:
- Water stewardship: Implement closed-loop systems and sedimentation ponds to minimize freshwater use and pollution.
- Tailings rehabilitation: Convert tailings into construction materials or restore vegetation cover.
- Regulatory compliance: Adhere to Environmental Impact Assessments (EIA), water management laws, and land rehabilitation requirements.
Beach sand beneficiation has evolved from single-process operations to integrated multi-technique workflows. The Gravity-Magnetic Combined Process, supplemented by electrostatic and flotation methods, enables efficient extraction of titanium, zircon, and rare-earth minerals while aligning with environmental goals. Future advancements in intelligent control and green technologies will further enhance the efficiency and sustainability of beach sand resource development.
JXSC has 38 years of experience in the mining industry, and many experienced engineers provide professional technical support to customers. We focus on providing turnkey solutions and full equipment sales services for mining. Over the years, we have served hundreds of customers at home and abroad. Please send us your mining information. JXSC can provide more accurate suggestions based on your specific situation.