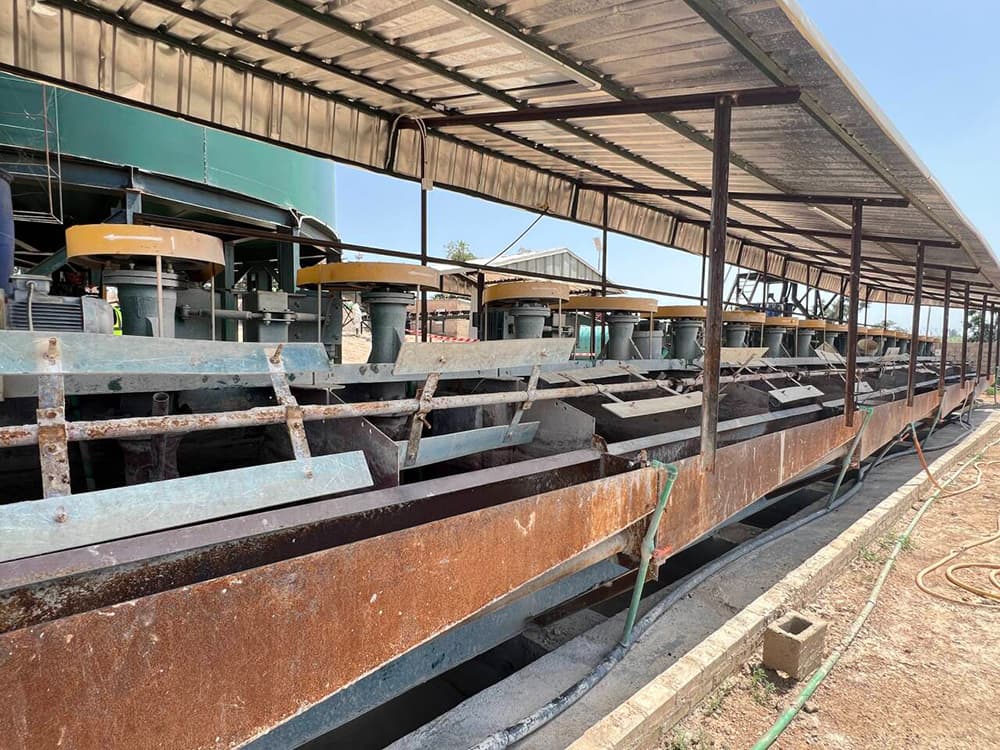
In mineral processing, froth flotation process has its efficient separation characteristics and has become one of the most commonly used beneficiation methods for copper ore flotation (such as chalcopyrite), gold ore flotation (containing gold sulfide), lithium ore and iron ore.
The principle of froth flotation process is based on the difference in hydrophobicity of mineral surfaces: in aerated slurry, hydrophobic minerals float up to form a foam layer by adsorbing bubbles, while hydrophilic minerals sink to the bottom, thereby achieving selective enrichment of target minerals. This physical and chemical separation mechanism is not only suitable for single metal extraction, but also can meet the separation needs of complex polymetallic ores.
This article will systematically analyze the four major froth flotation methods of direct flotation, reverse flotation, differential flotation and bulk flotation, from principle analysis, application scenarios to typical cases, to provide mining practitioners with a selection reference with both theoretical depth and practical value
1. Direct Flotation
Principle:
Direct flotation makes the surface of useful minerals hydrophobic by adding collectors, which are easily attached to bubbles and float to the surface of the slurry to form a foam layer, while the gangue minerals remain in the slurry. For example, in fluorite flotation, fluorite is preferentially floated as concentrate.
Direct flotation process:
Including crushing and grinding → slurry mixing and dosing (adjusting agent, collector) → flotation separation → dehydration and drying. For example, the positive flotation of siderite is divided into acidic process (neutral/weakly acidic medium, adding fatty acid collectors after desliming) and alkaline process (weakly alkaline medium, no desliming, using oxidized paraffin soap, etc.).
Application scenarios:
– High-siliceous phosphate ore (such as phosphate ore, MgO content <1%)
– Fluorite, magnesium oxide ore, spodumene (acid positive flotation)
– Fine-grained siderite (separation of iron minerals by surface hydrophobicity differences)
– Copper ore (low-grade ore-0.5% Cu, purified to 25% concentrate)
Advantages and limitations:
-Advantages: simple process, high impurity separation efficiency (such as reducing Fe and Al content).
– Limitations: large amount of reagents, such as a certain high-silicon bauxite positive flotation requires a large amount of fatty acid collectors, and the foam is viscous, making dehydration difficult.
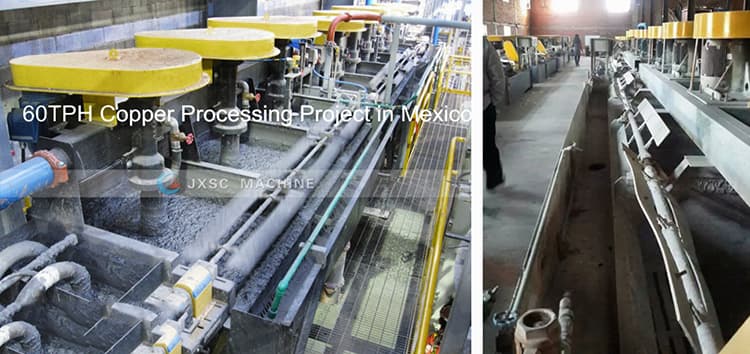
2. Reverse Flotation
Principle:
The inhibitor makes the surface of the gangue mineral hydrophilic, while the useful minerals sink hydrophobically, and the gangue floats up as a foam product. Typical applications include defluoridation of calcium from iron concentrate (reverse flotation to remove calcium gangue).
Reverse flotation process:
– Reverse flotation dephosphorization of iron ore, such as magnetite pre-enrichment to obtain rough concentrate by magnetic separation, and reverse flotation dephosphorization to remove apatite.
Application scenarios:
– Calcium phosphate ore (separation of dolomite gangue)
– Desiliconization of bauxite (reverse flotation of silicate gangue)
– Desulfurization and dephosphorization of iron ore (such as reverse flotation of magnetite)
Advantages and limitations:
– Advantages: normal temperature operation, energy saving, and easy filtration of concentrate. Such as bauxite reverse flotation reagent residue.
– Limitations: narrow applicability (poor effect on siliceous ores), poor selectivity of cationic collectors, such as low efficiency in laterite nickel ore sorting.
3. Differential Flotation
Principle:
In polymetallic ores, different useful minerals are floated in sequence, and other minerals are suppressed each time. For example, in lead-zinc sulfide ores, zinc is first suppressed to float lead, and then zinc minerals are activated.
Differential flotation process:
Typical lead-zinc ore: crushing and grinding → lead flotation (inhibitor suppresses zinc) → zinc activation flotation → tailings treatment.
Applicable conditions:
– Mineral dissociation is sufficient
– Large differences in mineral floatability (such as lead preferential flotation in lead-zinc ore)
– Coarse-grained impregnated ore (such as dense massive sulfide ore)
– High ore grade (lead-zinc ore),
Advantages and limitations:
– Advantages: stable process control and high concentrate grade.
– Limitations: large amount of inhibitor and high grinding cost.
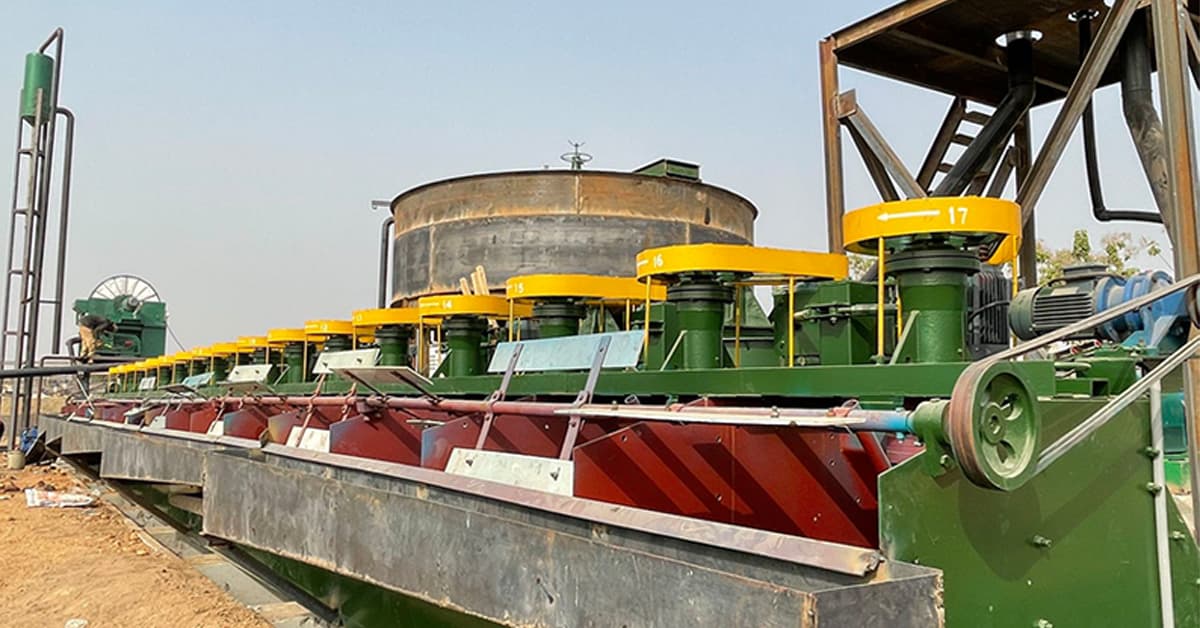
4. Bulk Flotation
Principle:
First float all useful minerals into mixed concentrates, and then separate them one by one. For example, copper-lead mixed concentrates are separated into copper concentrates and lead concentrates after regrinding.
Bulk flotation process:
Copper-molybdenum mixed flotation: A copper-molybdenum mine adopts “one-stage rough grinding-mixed flotation-rough concentrate regrinding-copper-molybdenum and sulfur separation-tailing sulfur selection-copper-molybdenum separation”
Applicable conditions:
– Low-grade ore (such as tungsten ore grade <1%)
– Tight mineral symbiosis (such as copper-lead sulfide ore)
– Fine-grained ore (reduce over-crushing)
Advantages and limitations:
– Advantages: save grinding costs and reduce equipment investment.
– Limitations: subsequent separation is difficult, and mixed concentrates have residual collectors.
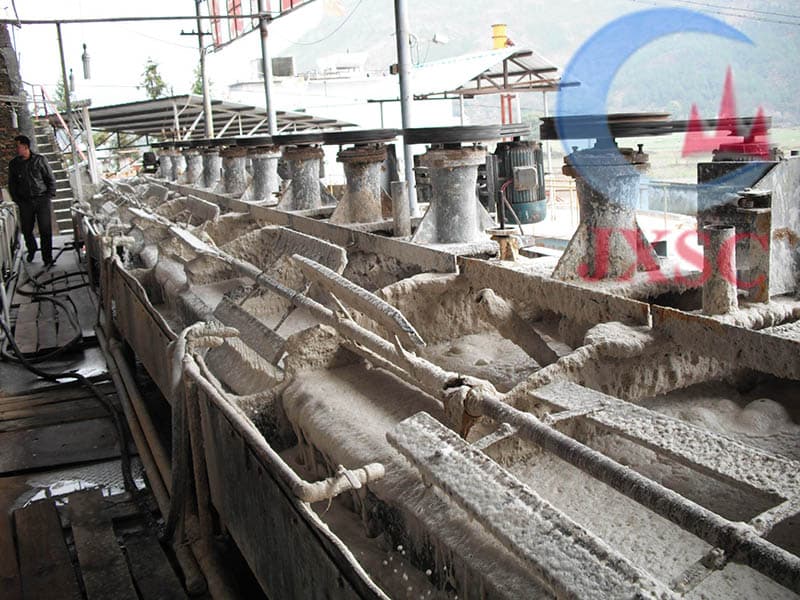
Combined process and technological innovation
1. collective-selective flotation
Combining priority and mixed flotation, such as preferential flotation of copper in copper-nickel ore and mixed flotation of nickel, taking into account efficiency and economy.
2. Equi-Flotation
Group flotation according to the difference in mineral floatability. Applicable to complex polymetallic sulfide ores, such as chalcopyrite and some easy-floating pyrite as the first group, and difficult-floating pyrite as the second group.
3. Direct-reverse flotation combined process
For example, phosphate ore is first reversely floated to remove calcium (dolomite) → then directly floated to remove silicon, solving the limitations of a single process.
Core factors in the selection of mineral processing technology
1. Ore properties: mineral embedded particle size, symbiotic relationship, floatability difference.
2. Economic cost: reagent cost, energy consumption, equipment investment.
3. Environmental impact: difficulty in tailings treatment, reagent toxicity.
4. Target product requirements: concentrate grade, recovery rate, impurity content.
Future development trend
1. Green reagent research and development: low-toxic/non-toxic inhibitors, such as starch derivatives instead of cyanide.
2. Intelligent control technology: real-time optimization of flotation parameters based on AI. Finland’s Outotec Courier system uses XRF online analysis to adjust reagent dosage in real time.
3. Joint process innovation: such as combining flash flotation with magnetic separation to improve precious metal recovery.
JXSC has 38 years of experience in the mining industry, and many experienced engineers provide professional technical support to customers. We focus on providing turnkey solutions and full equipment sales services for mining. Over the years, we have served hundreds of customers at home and abroad. Please send us your mining information. JXSC can provide more accurate suggestions based on your specific situation.
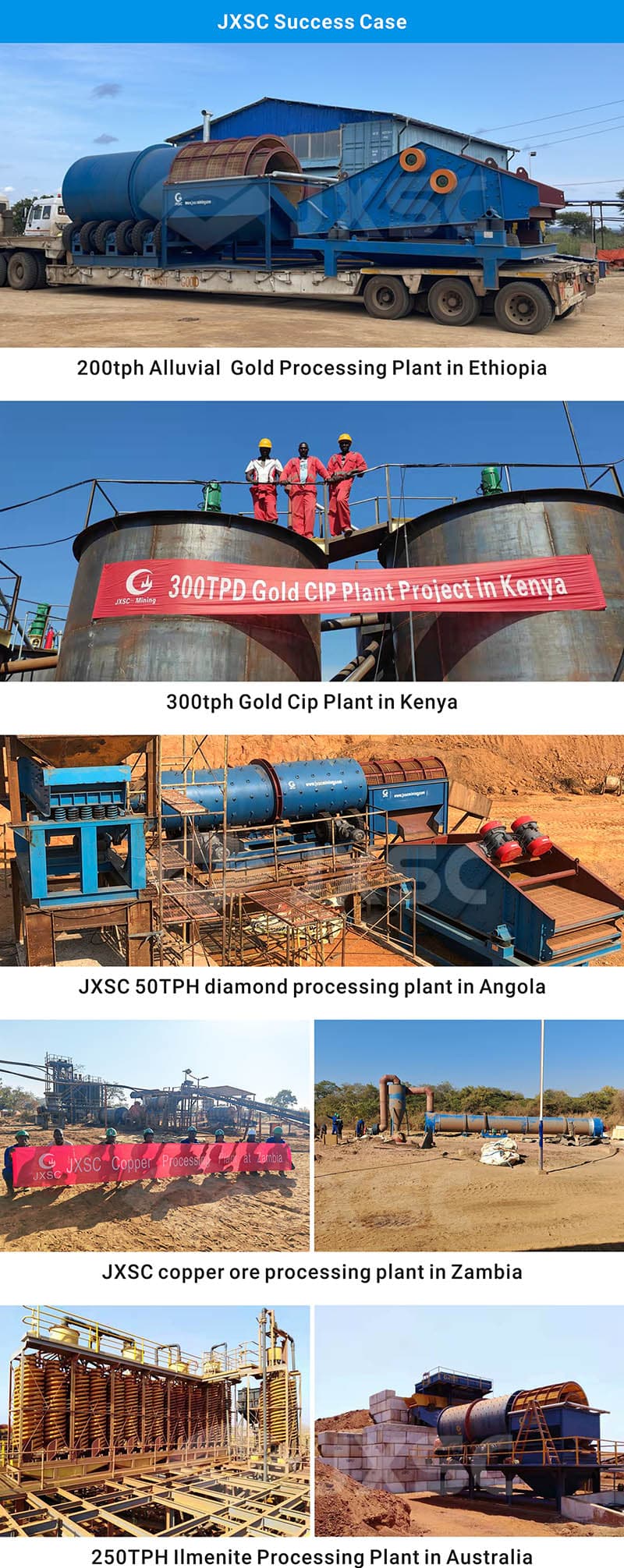