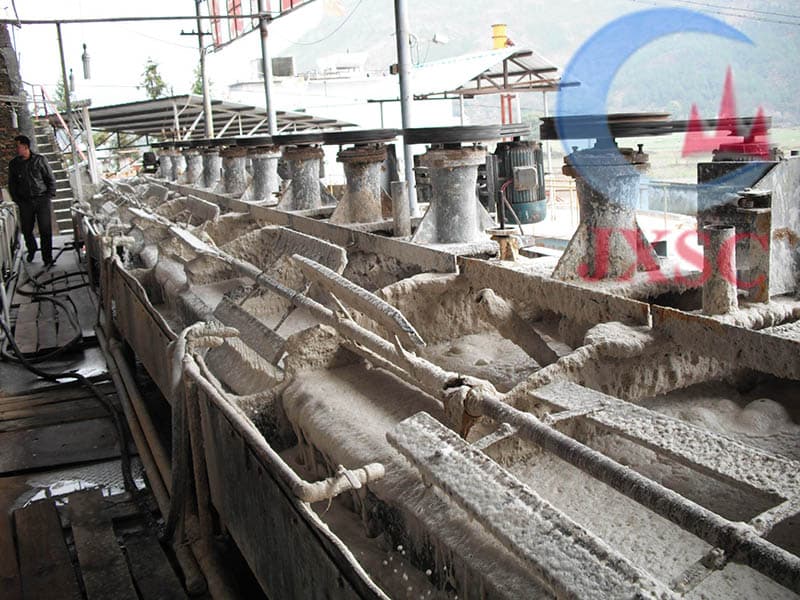
In the field of mineral processing, flotation is a core technology for separating minerals based on differences in their surface hydrophobicity. Flotation reagents, critical to this process, are categorized into collectors, frothers, and modifiers. Among these, flotation reagents directly influence separation efficiency by regulating the slurry environment and mineral surface properties. This article systematically analyzes the mechanisms and industrial applications of five major flotation reagent types—pH regulators, activators, depressants, flocculants, and dispersants—providing theoretical insights for optimizing mineral processing workflows.
1. pH Regulators: Precision Controllers of Slurry Acidity/Alkalinity
pH is a pivotal parameter in flotation systems, governing mineral surface charge, reagent adsorption, and chemical reaction pathways. Common pH regulators include lime, sodium carbonate, sulfuric acid, sulfur dioxide, and caustic soda.
1) Lime (CaO/Ca(OH)₂)
Limestone (CaCO₃) decomposes into quicklime (CaO) and carbon dioxide when calcined at 1200°C. Quicklime absorbs water to form hydrated lime (Ca(OH)₂), a white powder with low water solubility. In practice, hydrated lime is typically added directly to ball mills or pre-flotation agitation tanks. Alternatively, it may be mixed with water to form a lime milk slurry before being introduced into flotation cells. As a strong base, Ca(OH)₂ fully dissociates in water, producing a highly alkaline solution:
Reaction: CaO + H₂O → Ca(OH)₂ → Ca²⁺ + 2OH⁻
Lime, the most economical pH regulator, is widely used to suppress pyrite in polymetallic sulfide ores by raising slurry pH. Pyrite surfaces oxidize to form hydrophilic films of Fe(OH)₂ and Fe(OH)₃ at pH >7. Suppressed pyrite can be reactivated using sodium carbonate and copper sulfate or by lowering the pH to 6–7 with sulfuric acid.
2) Sodium Carbonate (Na₂CO₃)
Sodium carbonate (soda ash), a weakly alkaline salt, dissolves in water to release Na⁺ and CO₃²⁻ ions. Hydrolysis generates OH⁻ ions, stabilizing slurry pH between 8–10:
Reaction: Na₂CO₃ → 2Na⁺ + CO₃²⁻ → CO₃²⁻ + H₂O ⇌ HCO₃⁻ + OH⁻
In lead-zinc sulfide flotation, sodium carbonate is preferred over lime to avoid Ca²⁺ interference with lead mineral recovery.
3) Sulfuric Acid (H₂SO₄)
Industrial sulfuric acid (96–98% concentration) is a strong acid commonly used for slurry acidification. When diluted, it dissociates as follows:
Dissociation: H₂SO₄ → 2H⁺ + SO₄²⁻
Critical Safety Note: During dilution, concentrated sulfuric acid must be slowly poured into water (never water into acid) to prevent rapid heat generation, which can cause boiling and splashing of hot acid, posing severe burn risks.
2. Activators: Molecular "Keys" for Mineral Surface Modification
Activators enhance collector adsorption by altering mineral surface chemistry through four mechanisms:
Spontaneous Activation: Soluble ions (e.g., Cu²⁺ from oxidized copper sulfides) naturally activate minerals like sphalerite during grinding, complicating separation. Lime or sodium carbonate is added to precipitate these “unavoidable ions.”
Pre-activation: Oxidized pyrite surfaces are treated with sulfuric acid to dissolve oxide layers, exposing fresh surfaces for flotation.
Revival: Cyanide-suppressed sphalerite can be reactivated with copper sulfate.
Sulfidization: Metal oxides (e.g., oxidized lead/zinc ores) are coated with sulfide films using Na₂S, enabling xanthate-based flotation.
Common activators: Sulfuric acid (H₂SO₄), sodium sulfide (Na₂S), copper sulfate (CuSO₄), oxalic acid ((COOH)₂), and lead salts (Pb(NO₃)₂).
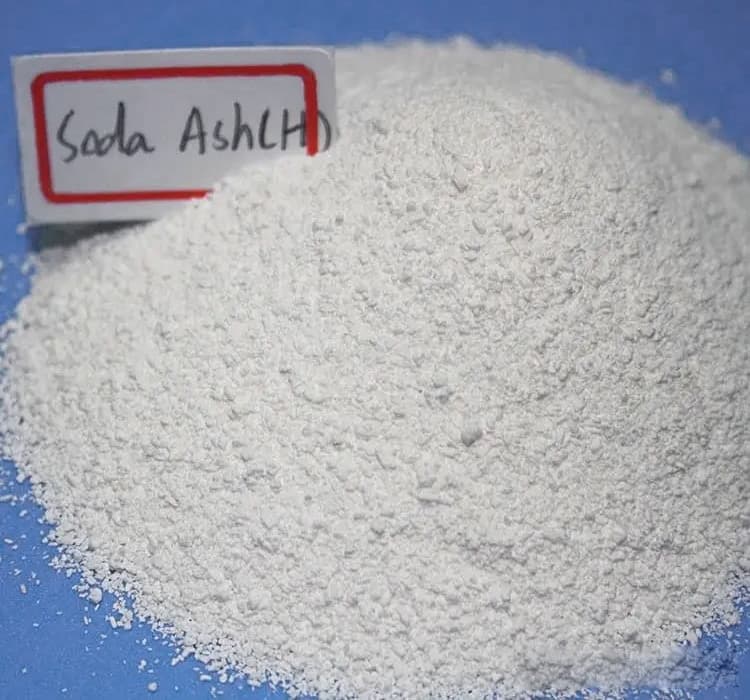
3. Depressants: Selective Molecular Barriers for Suppression
Depressants form hydrophilic layers on mineral surfaces to inhibit flotation. Key examples:
1) Sodium Sulfide (Na₂S)
At high dosages, Na₂S suppresses sulfides by forming hydrophilic hydroxide films. For example, in molybdenite flotation, Na₂S inhibits pyrite while molybdenite (naturally hydrophobic) remains unaffected.
2) Zinc Sulfate (ZnSO₄)
ZnSO₄ weakly inhibits sphalerite alone but synergizes with alkalis or cyanide for stronger suppression at elevated pH.
3) Sodium Cyanide (NaCN)
NaCN selectively depresses pyrite, sphalerite, and copper sulfides in priority flotation. Due to toxicity, alternatives like SO₂ or Na₂SO₃ are increasingly used. Notably, minerals suppressed by SO₂/Na₂SO₃ are more easily reactivated than those treated with NaCN.
4) Lime
Lime suppresses pyrite via CaSO₄/CaCO₃ surface films. Reactivation requires pH adjustment to 6–7 with sulfuric acid, followed by butyl xanthate addition.
5) Phosphinoguanidine (Phosnox)
Synthesized from P₂S₅ and NaOH, Phosnox is diluted to 0.5–1% before use as a depressant.
6) Sodium Silicate (Na₂SiO₃)
A versatile inhibitor/dispersant, sodium silicate adsorbs HSiO₃⁻ or H₂SiO₃ onto quartz and silicate surfaces, forming hydrophilic layers. Its efficacy depends on the SiO₂/Na₂O modulus (optimal modulus: 2.2).
7) Sodium Thioglycolate
Used in molybdenum refining to suppress copper impurities, reducing Cu content from 0.5% to <0.17%.
8) Oxalic Acid ((COOH)₂)
Effective for suppressing barite and garnet in fluorite flotation, ensuring high-purity CaF₂ concentrates (>95%).
9) Carboxymethyl Cellulose (CMC)
CMC inhibits magnesium silicates (e.g., pyroxene, serpentine) and improves nickel ore flotation selectivity.
4. Flocculants and Dispersants: Slurry Rheology Modulators
1) Flocculants
Polyacrylamide (PAM) accelerates fine-particle settling in thickeners, reduces filtration moisture, and treats tailings. For example, PAM reduces tungsten losses (0.6–0.8% WO₃ in overflow) in tungsten processing.
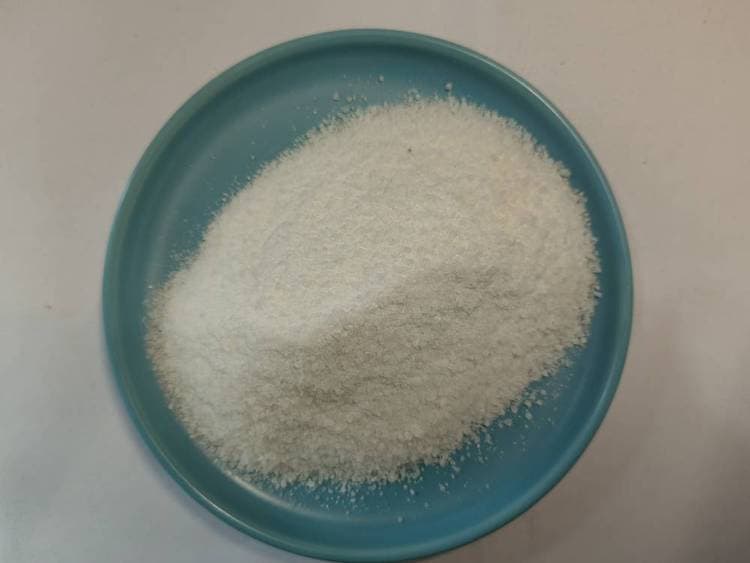
2) Dispersants
Sodium silicate disperses slimes, enhancing concentrate grades while doubling as a pH regulator and depressant.
5. Emerging Trends in Flotation Reagents: Sustainability & Innovation
Modern flotation reagents emphasize efficiency, low toxicity, and biodegradability:
Cyanide Alternatives: SO₂-air systems reduce wastewater COD by >60% .
Biobased Inhibitors: Modified starch and chitosan offer eco-friendly selectivity.
Smart Control: Real-time pH/potential sensors optimize reagent dosing, reducing costs by 15–20%.
Flotation reagents act as a “chemical toolbox,” where pH regulators set the stage, activators/depressants mediate surface interactions, and flocculants/dispersants optimize slurry behavior. Future advancements in green chemistry and automation will drive sustainable mineral processing.