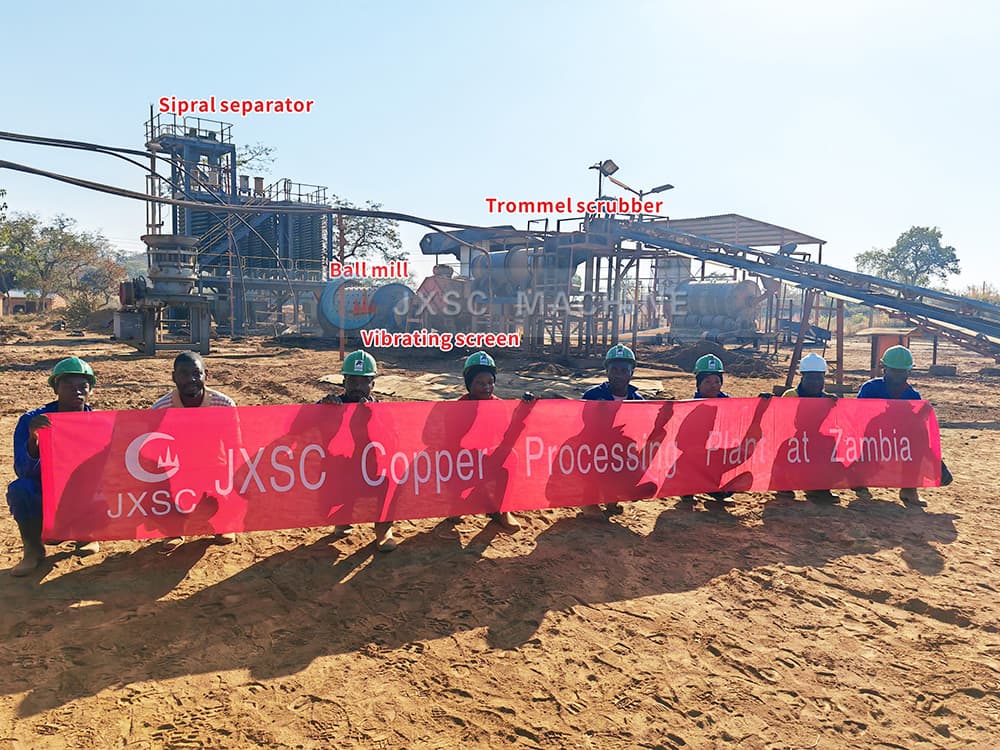
A modern mineral processing plant operates as an integrated production line that transforms raw ore into high-grade concentrate through precisely coordinated crushing, grinding, and separation stages. The mineral processing plant strategically combines physical and chemical beneficiation methods – including flotation systems and magnetic separation technologies – to efficiently remove gangue materials while maximizing valuable mineral recovery. This optimized multi-process operation enables the mineral processing plant to achieve dual objectives: producing standardized smelting-ready concentrates and improving comprehensive resource utilization rates. Through intelligent process coordination, the plant ensures consistent quality output while maintaining operational efficiency across all beneficiation stages.
1. Ore dressing preparation operation
(1) Crushing
The raw ore is first crushed by a jaw crusher or a gyratory crusher, then by a cone crusher or an impact crusher, and finally by a short-head cone crusher or a high-pressure roller mill. Some processes use closed-loop circulation, such as two-stage full closed-loop crushing. The ore that does not meet the standards after screening will be returned for re-crushing.
Function:
● Reduce the particle size of the ore, achieve “more crushing and less grinding”, and reduce the energy consumption of grinding.
● Use different mechanical forces, such as extrusion, impact, splitting, etc., to adapt to the hardness and characteristics of the ore.
Equipment selection:
● For coarse crushing, a jaw crusher can be selected, which has the characteristics of simple structure and large processing capacity.
● For medium and fine crushing, a cone crusher can be selected, which is suitable for efficient closed-circuit crushing; a high-pressure roller mill can also be selected, which is an energy-saving innovative equipment.
(2) Grinding and classification
The crushed ore enters the ball mill or autogenous mill for wet grinding, and is combined with spiral classifiers, hydrocyclones and other classification equipment to form a closed-circuit system. In this system, the coarse particles will return to the mill for re-grinding, and the qualified slurry will enter the sorting operation.
Process parameter optimization:
● By adjusting the ratio of media such as steel balls, steel bars, gravel and the speed of the mill, ensure that the mineral is separated into monomers.
● When wet grinding is used, the slurry concentration can be controlled at the usual 40-75% to reduce the over-crushing of the ore.
Function:
● Refine the ore to -200 mesh, that is, a particle size of about 74μm, so that the useful minerals and the gangue are fully dissociated.
2. Ore dressing process
Use the difference in the physical or chemical properties of minerals to separate useful minerals from the gangue to obtain concentrates, middlings and tailings.
(1) Flotation method
Principle: Change the hydrophobicity of the mineral surface through flotation agents such as collectors and frothers, so that the minerals are mixed with air in the flotation machine to form mineralized foam, thereby separating the target minerals.
Applicable scenarios:
● Applicable to non-ferrous metal ores and sulfide ores such as copper, lead, zinc, and molybdenum;
● Can be used for the fine separation of complex co-existing ores.
Equipment: Mechanical agitator flotation machine, aerated flotation machine, etc.
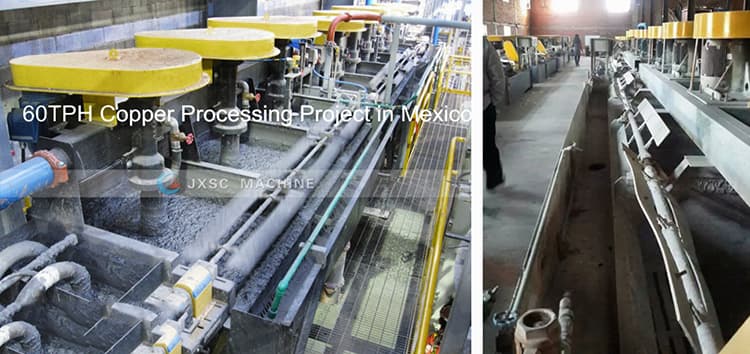
(2) Magnetic separation
Principle: Utilize the difference in mineral magnetism to separate magnetic minerals such as magnetite from non-magnetic minerals in the magnetic field of the magnetic separator.
Applicable scenarios:
● Applicable to magnetite, vanadium-titanium magnetite and rare earth ores in iron ore;
● For weakly magnetic minerals, strong magnetic field equipment is required for separation.
(3) Gravity separation
Principle: Based on the difference in mineral density, use equipment such as shaking tables, jigs, spiral chutes, etc. to separate by gravity in water or air flow.
Applicable scenarios:
● Applicable to ores with significant density differences such as gold, tungsten, and tin;
● Can be used for coarse particle pre-selection or tailings recycling.
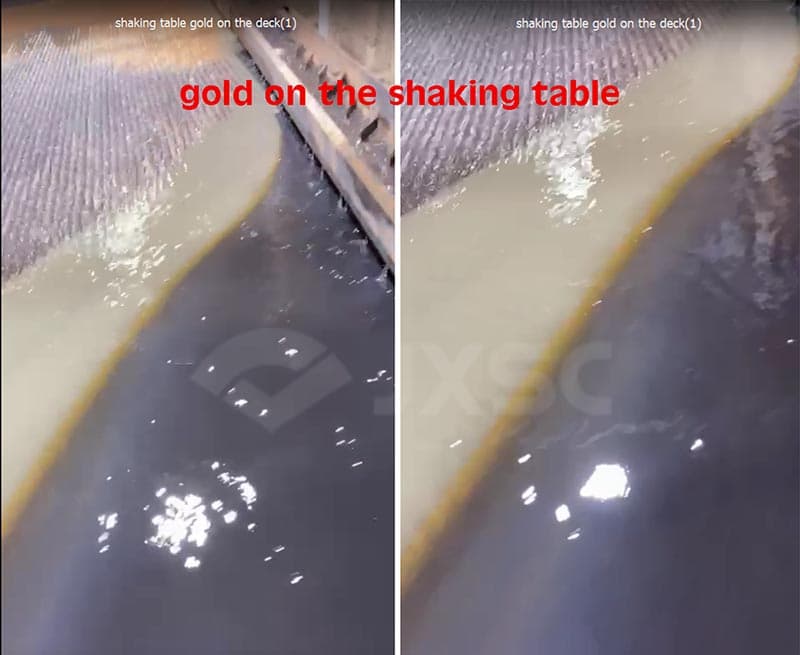
(4) Combined process
For example, the combined process of magnetic separation and flotation is used for iron ore desulfurization, and the combined process of gravity separation and flotation is used to treat complex polymetallic ores, so as to improve the separation efficiency.
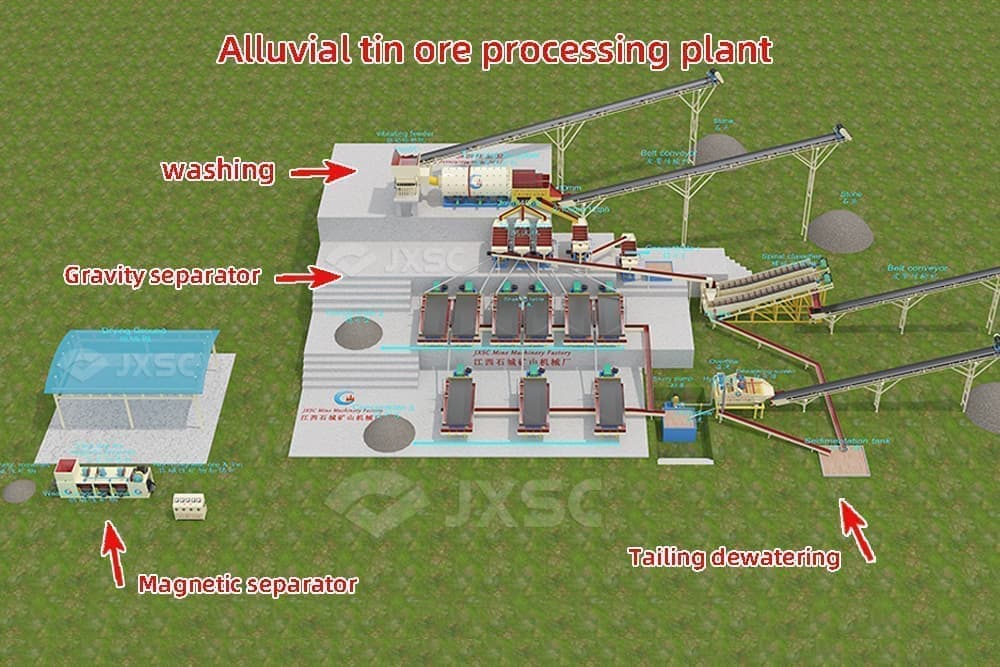
3. Tailings treatment
Reduce the moisture content of concentrate to facilitate transportation and smelting; recycle water resources and reduce environmental pollution.
(1) Concentration
Technology: Using high-efficiency concentrators with scrapers, hydrocyclones and other equipment for gravity sedimentation can increase the pulp concentration from 20-30% to 50-70%.
Advantages: Low energy consumption, suitable for processing fine-grained materials with a particle size of less than 0.3mm.
(2) Filtration
Technology: Using a cylinder filter for vacuum filtration and a plate and frame filter press for pressure filtration can further remove moisture to 8-16%.
Equipment selection:
● For fine-grained concentrates, a ceramic filter that can achieve low-moisture dehydration can be selected;
● For ultrafine powders with a particle size of less than 25μm, a filter press can be selected.
(3) Drying
Technology: Using a rotary dryer for direct hot air drying can reduce the moisture content to less than 10%.
Application scenarios:
● Used for transportation and antifreeze in cold areas;
● Used when users have strict requirements on moisture.
Limitations: High cost and high energy consumption, only used when necessary.
4.From Ore to Output: Process Flow in a Mineral Processing Plant
● Process:
Ore→crushing→grinding→sorting→concentration→filtration→drying→concentrate/tailings.
● Material management:
Reducing resource waste through closed-loop circulation such as grinding-grading, crushing-screening; tailings are pumped to the tailings pond, and water is recycled at the same time.
● Process diagram: Line flow chart: Use thin lines to indicate the material flow direction and mark the key parameters of each link; (As follows)
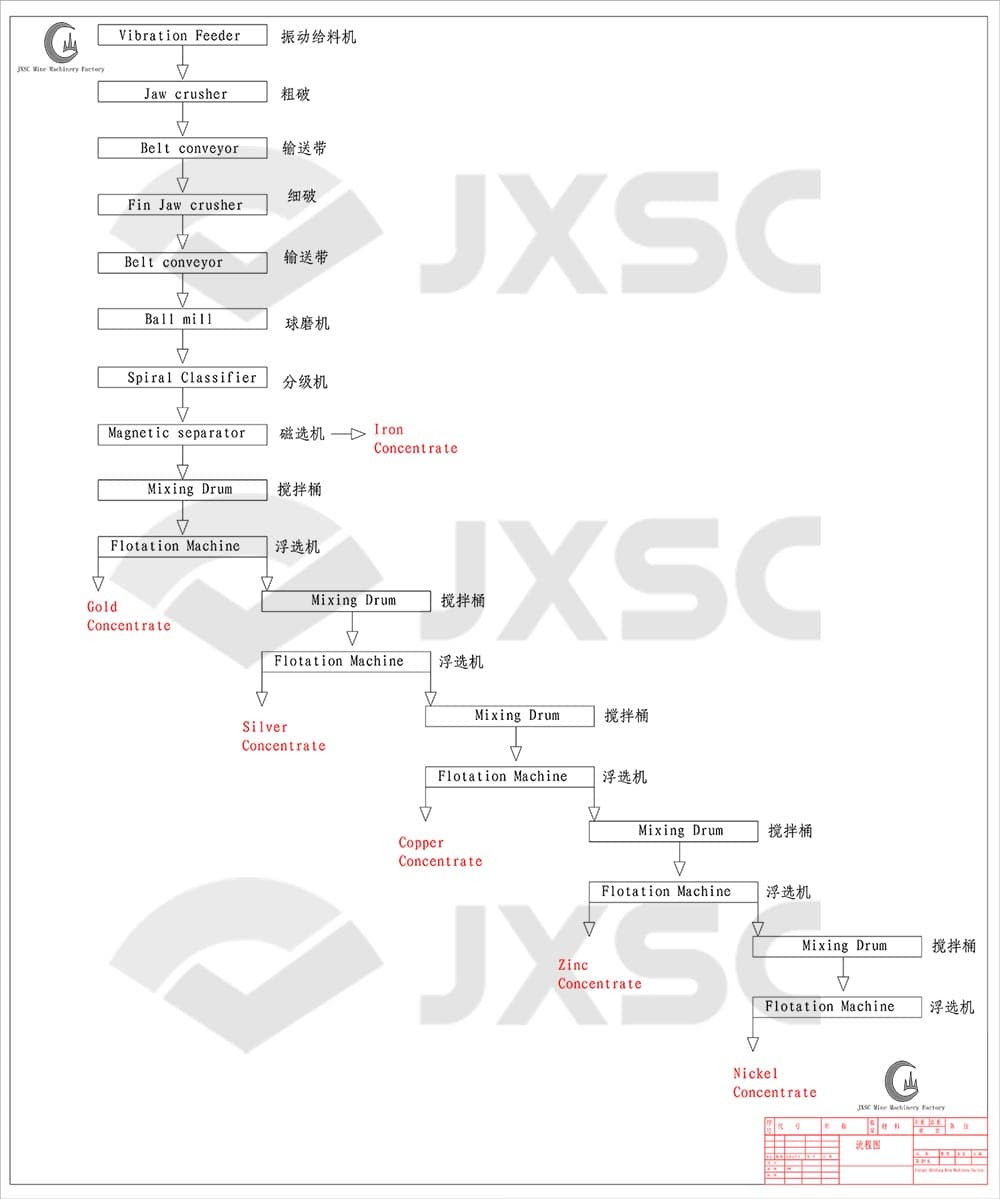
Equipment flow chart: Intuitively display the equipment connection and slurry path. (As follows)
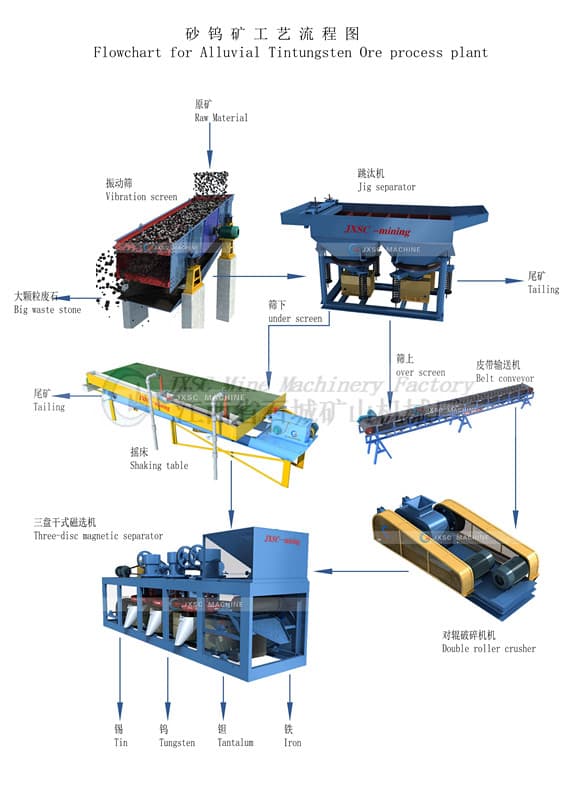
5. Technical and economic analysis
● Crushing-grinding: Accounts for more than 50% of the total energy consumption. Optimizing equipment selection and closed-loop design can significantly reduce costs.
● Ore dressing process: The cost of magnetic separation and gravity separation equipment is relatively low, while the cost of flotation reagents and maintenance is relatively high.
● Dehydration process: The two-stage method of concentration-filtration takes into account both efficiency and economy, and drying is limited to special needs.
JXSC has 38 years of experience in the mining industry, and many experienced engineers provide professional technical support to customers. We focus on providing turnkey solutions and full equipment sales services for mining. Over the years, we have served hundreds of customers at home and abroad. Please send us your mining information. JXSC can provide more accurate suggestions based on your specific situation.
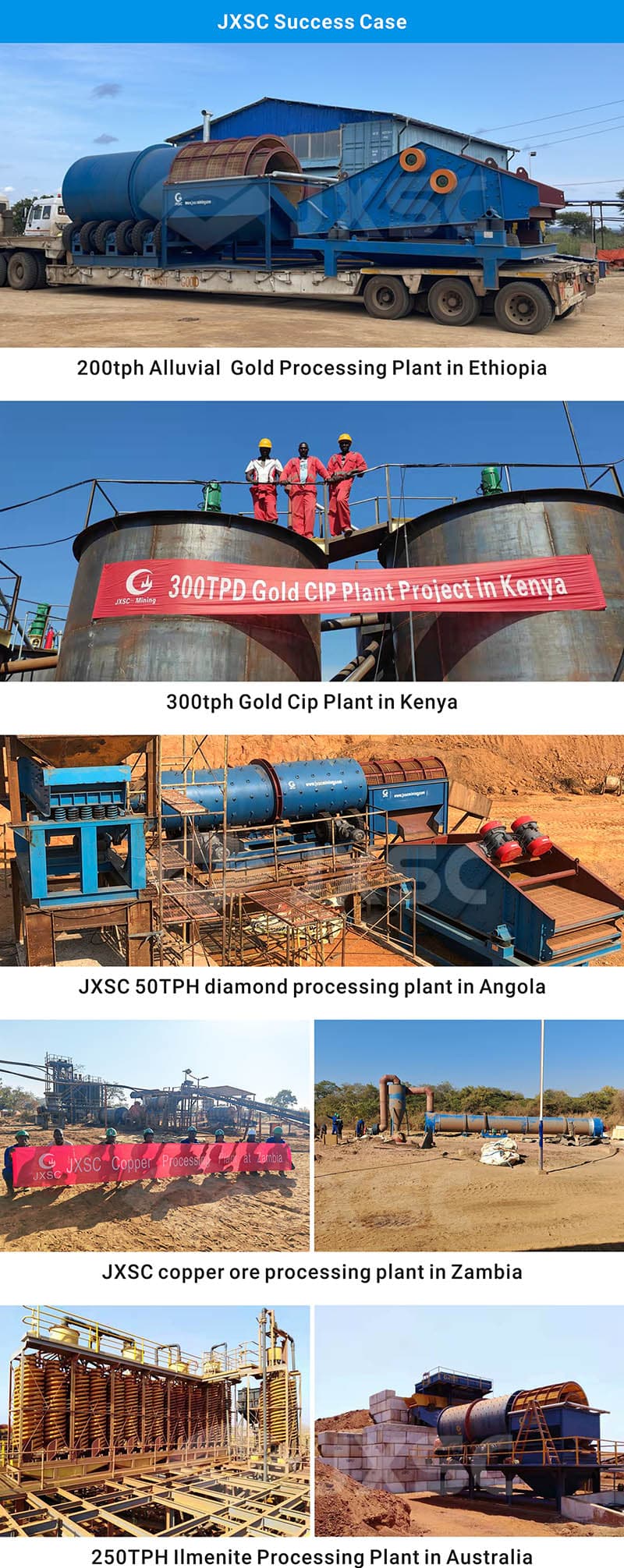