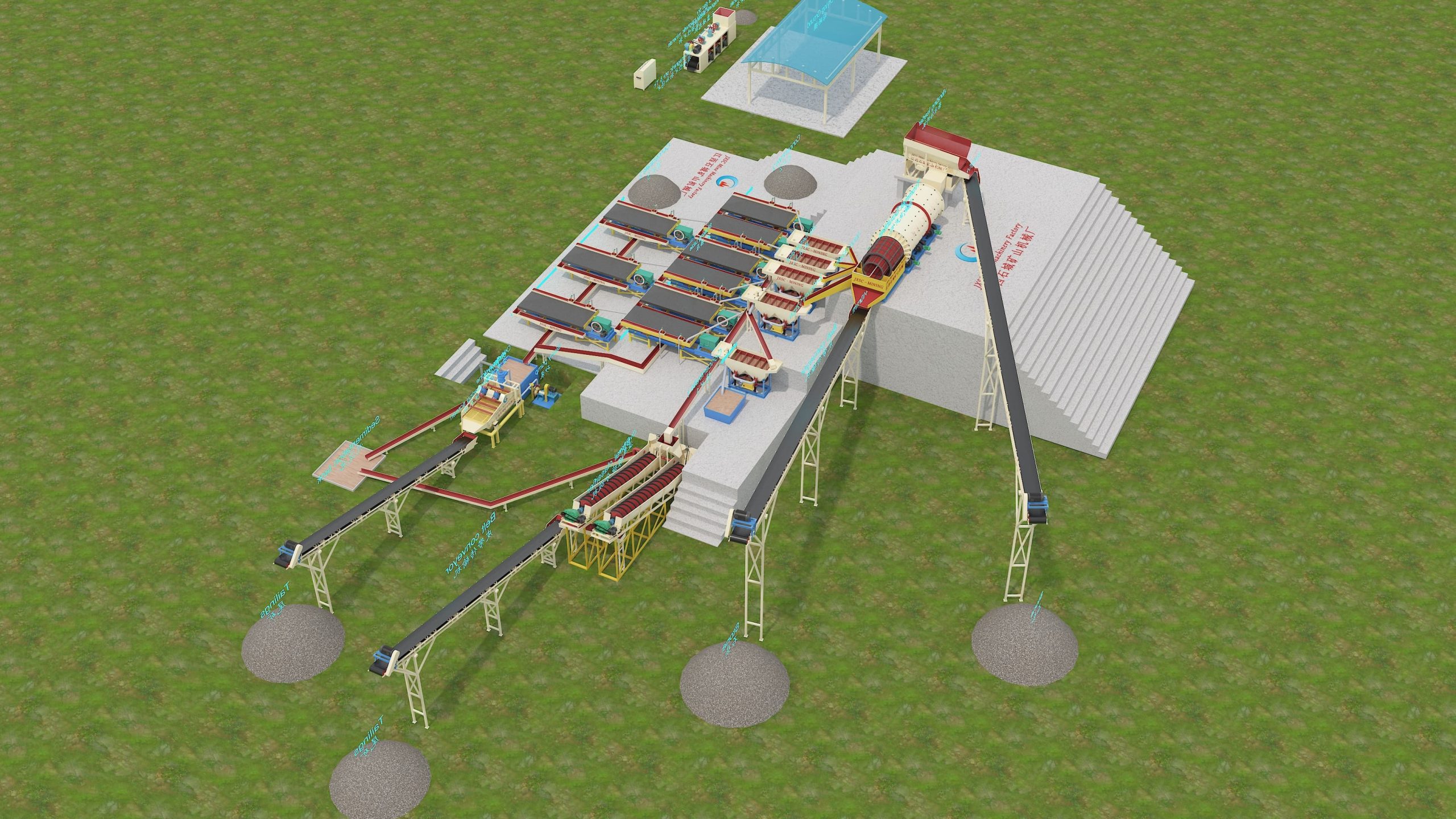
Iron ore is classified into several types based on its mineral composition and physical properties, which play a vital role in the effectiveness of mineral processing technology. The main types of iron ore are hematite, magnetite, limonite, and siderite, each of which has different properties that affect its processing and application in the steel industry.
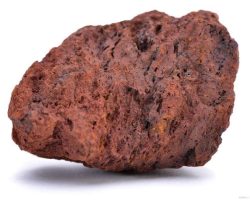
1. Hematite
Hematite is one of the most important iron ores. It is red or brownish red and often appears in granular or lumpy form. The iron content is usually between 60% and 70%. This iron oxide (Fe2O3) is highly regarded for its high purity and ease of processing. In mineral processing, hematite is usually separated by gravity separation and flotation to increase the iron concentration and reduce impurities.
Hematite processing:
Gravity separation: Due to hematite’s high density, gravity separation is a common preliminary beneficiation method. Gravity separation equipment includes shaking tables, spiral chute, etc. By utilizing the density difference between hematite ore and impurity minerals, purer hematite can be effectively separated.

Magnetic separation: Hematite has a certain magnetic property, especially after the hematite is ground, the magnetic property is enhanced. Hematite is separated from other non-magnetic minerals by a strong magnetic field.
Flotation separator: Flotation of hematite is mainly used to process low-grade ores or complex ores. Hematite can be selected by using flotation agents, adjusting the pH value of the slurry, and other conditions.
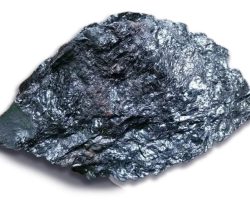
2. Magnetite
Magnetite is a magnetic iron oxide (Fe3O4) that usually has a slightly lower iron content, usually between 50% and 60%. The strong magnetic properties of magnetite make it particularly suitable for magnetic separation technology in mineral processing. Magnetite is usually found in fine-grained deposits, and its processing usually involves crushing, grinding, and separation to produce a high-grade concentrate. This concentrate can then be used in a variety of applications, including the direct reduction process of iron production.
Magnetite processing:
Magnetic separation: The main beneficiation method for magnetite is magnetic separation. Due to its strong magnetic properties, magnetite can be effectively separated from other non-magnetic minerals by magnetic separators. According to the particle size and properties of the ore, select appropriate magnetic separation equipment, such as strong magnetic separators or high gradient magnetic separators.
Flotation separator: For low-grade magnetite, flotation is also an effective beneficiation method. By adding flotation agents, magnetite can be floated and separated from other impurities. Commonly used flotation agents include fatty acids and hydroxyphosphates.
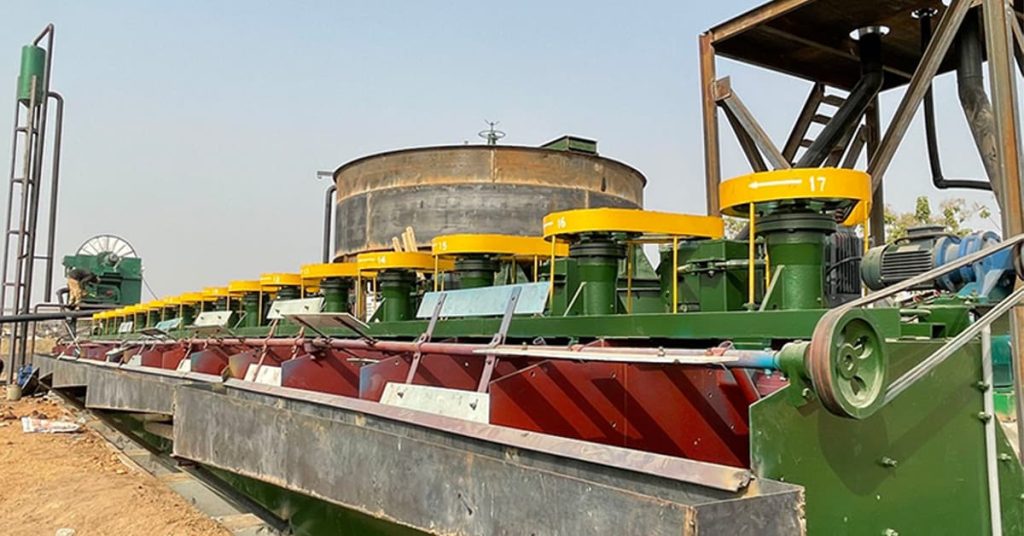
Gravity separation: Gravity separation can also play a role in the treatment of coarse-grained magnetite. Commonly used gravity separation equipment includes shaking tables and spiral chutes.
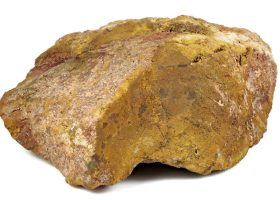
3. Limonite
Limonite is a hydrated iron oxide mineral with a relatively complex chemical composition and an iron content generally between 40% and 60%. Limonite is usually yellow-brown or dark brown, with a loose texture, and is commonly found in weathered iron ores and sediments.
Limonite processing:
Gravity separation: Due to the relatively low density of limonite, gravity separation is often used for preliminary separation. Equipment includes shaking tables and spiral chutes, which can be used to sort ore according to its particle size.
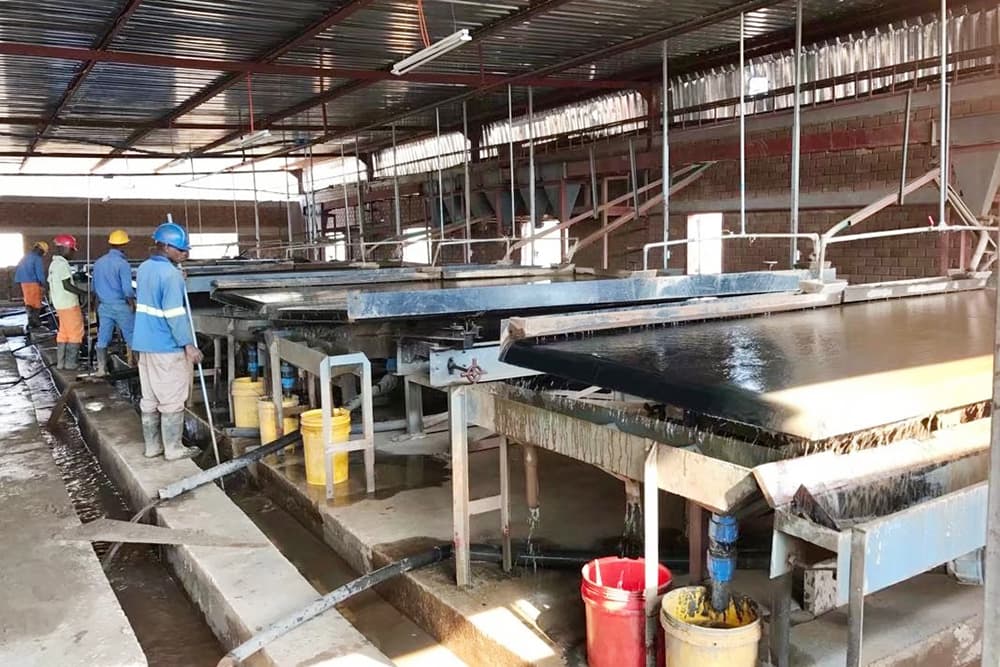
Magnetic separation: Limonite has weak magnetism, but it can still be separated magnetically in some cases. It is separated from other non-magnetic minerals by a high-gradient magnetic separator.
Flotation separator: Flotation is one of the important methods for limonite beneficiation. By adding an appropriate amount of flotation reagents, the recovery rate of limonite can be increased. Commonly used flotation reagents include anion collectors and cationic depressants.
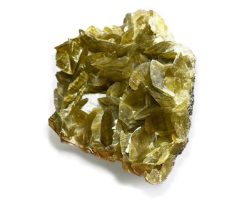
4. Siderite
The main component of siderite is FeCO3, and its iron content is generally between 48% and 62%. Siderite is brown or gray, soft in texture, and usually appears in sedimentary rocks. Because it contains a high carbonate ions content, siderite needs to be considered for its reducibility during smelting.
Siderite processing:
Gravity separation: Due to the high density of siderite, it can be initially separated by gravity separation, and the commonly used equipment are shaking tables.
Flotation separator: Flotation is one of the main methods for siderite beneficiation. Siderite can be effectively separated by adjusting the pH value of the slurry and adding flotation reagents.
Roasting: Due to the chemical properties of siderite, roasting is also a common method for siderite processing. Through high-temperature roasting, FeCO3 can be converted into Fe2O3, thereby increasing its iron content.
This article introduces several major iron ore beneficiation methods. In actual production, it is also necessary to conduct beneficiation tests on the minerals and select the most suitable beneficiation process based on the specific composition and proportion of the ore.
JXSC has 38 years of experience in the mining industry, and many experienced engineers provide professional technical support to customers. We focus on providing turnkey solutions and full equipment sales services for mining. Over the years, we have served hundreds of customers at home and abroad. Please send us your mining information. JXSC can provide more accurate suggestions based on your specific situation.
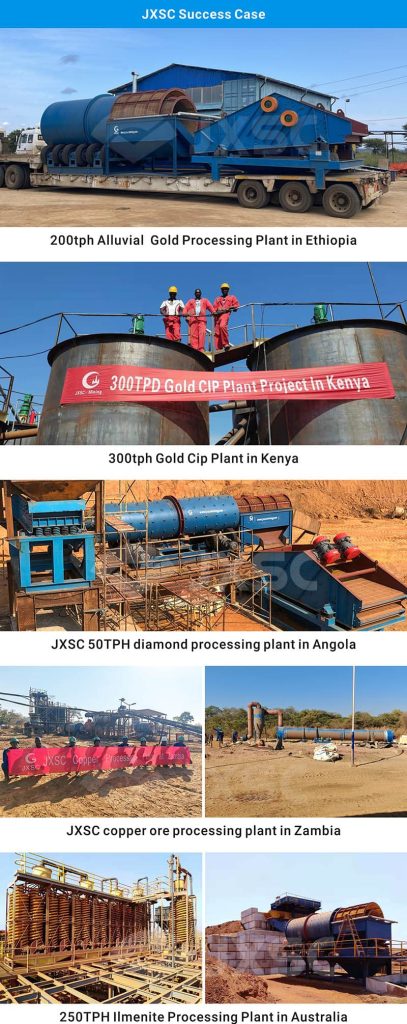