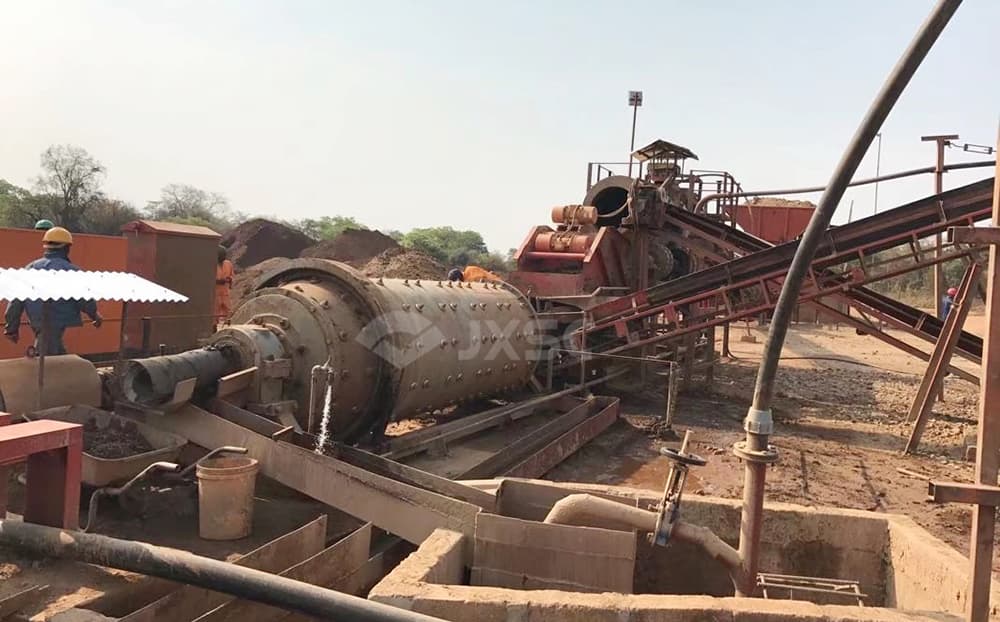
In mining, ore mill grinding stands as the core and indispensable link, and its effect has a direct and critical impact on the subsequent sorting efficiency and economic benefits. Based on the application of modern technology and the accumulation of rich practical experience, this article summarizes the common problems in the grinding process and their professional solutions.
1. Low grinding efficiency
Problem manifestation:
● The processing volume decreased, and the unit energy consumption (kWh/t) increased significantly
● The particle size distribution of the grinding product became wider, and the proportion of qualified particle size (-200 mesh) was lower than the design value
Cause analysis:
1. Unreasonable ratio of steel balls (medium): the initial loading ratio of large balls is too high or the ball supplementation system is unscientific
2. Changes in ore properties: fluctuations in ore hardness (BWI), particle size or grindability index (Wi)
3. Mill parameter imbalance: the speed does not reach 75%~88% of the critical speed, and the filling rate exceeds the reasonable range of 25%~40%
Solutions:
1. Medium optimization:
● Use Bond ball diameter formula to calculate the optimal ball diameter:
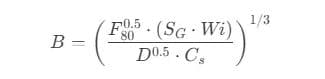
(F80: 80% screened particle size, SG: ore specific gravity, Cs: mill speed percentage)
● Implement precise ball replenishment system, the amount of balls added per shift = initial ball loading × (1-medium wear rate)
2. Online monitoring and adjustment:
●Install vibration sensors and power monitors to adjust mill load in real time
●Use online particle size analyzer (such as Malvern Insitec) to control cyclone parameters in a closed loop
2.Product particle size is unqualified
Problem manifestation:
●The content of coarse particles (+0.15mm) exceeds 10% or the proportion of over-crushing (-0.038mm) is greater than 30%
Cause analysis:
1. Failure of classification equipment: wear of cyclone sand settling nozzle leads to classification efficiency <40%
2. Grinding concentration is out of control: slurry concentration >75% or <65% (conventional grinding concentration should be controlled at 68%~72%)
3. Ore is over-crushed: grinding time is too long or medium size is too small
Solutions:
1. Improvement of classification system :
● The replacement cycle of the cyclone sand nozzle is shortened to 15 days
● A high-frequency fine screen (sieve hole 0.1mm) is used to form a joint classification with the cyclone
2. Accurate concentration control:
● Install a gamma-ray densitometer to automatically adjust the amount of water replenishment, and the concentration fluctuation range is ±1%
● Add dispersant to sticky ores (such as sodium hexametaphosphate, dosage 0.1~0.3kg/t)
3. Over-crushing prevention and control:
● Use stage grinding (coarse grinding + re-grinding), and increase the size of steel balls in the coarse grinding section by 10%~15%
● Introduce a tower mill to treat the fine grinding section to reduce the mud rate
3. Severe equipment wear Heavy
Problem manifestation:
● Liner service life <6 months, steel ball consumption >1.2kg/t
● Equipment unplanned downtime frequency >2 times/month
Cause analysis:
1. Improper material selection: high chromium cast iron liner hardness <58HRC or impact toughness <8J/cm²
2. Slurry is highly corrosive: pH <6 or sulfide content >3% leads to aggravated electrochemical corrosion
3. Installation process defects: liner gap >5mm causes slurry scouring
Solutions:
1. Upgrade of wear-resistant materials:
● Use niobium (Nb)-containing micro-alloyed liner (hardness ≥62HRC, life 50% longer)
●Use forged low-chromium alloy steel balls (unit consumption reduced to 0.8kg/t)
2. Corrosion protection:
●Add lime to the slurry to adjust the pH to 8.5~9.0
●Spray tungsten carbide coating on the lining surface (thickness 0.3mm, corrosion resistance increased by 3 times)
3. Accurate installation:
●Use laser alignment instrument to control the lining installation gap <2mm
●Use polymer filling glue to seal the joints
4. Excessive energy consumption
Problem manifestation:
●Ball mill power consumption >12kWh/t, accounting for more than 40% of the total energy consumption of the concentrator
Cause analysis:
1. Ineffective power High proportion: mill transmission efficiency <90%, large friction loss
2. Excessive ball loading: filling rate >40% leads to useful power ratio <65%
3. Poor ore grindability: Bond work index Wi >15kWh/t
Solutions:
1. Energy-saving technology transformation:
● Use permanent magnet direct drive motor (efficiency increased to 96%)
● Install inverter to achieve soft start and speed optimization
2. Medium filling optimization:
● Determine the optimal filling rate (usually 28%~32%) through DEM (discrete element method) simulation
● Use intelligent ball replenishment system (error <±2%)
3. Ore pretreatment:
● High-pressure roller mill pre-crushing (product -5mm proportion > 80%)
● Microwave pretreatment (energy consumption reduced by 30%)
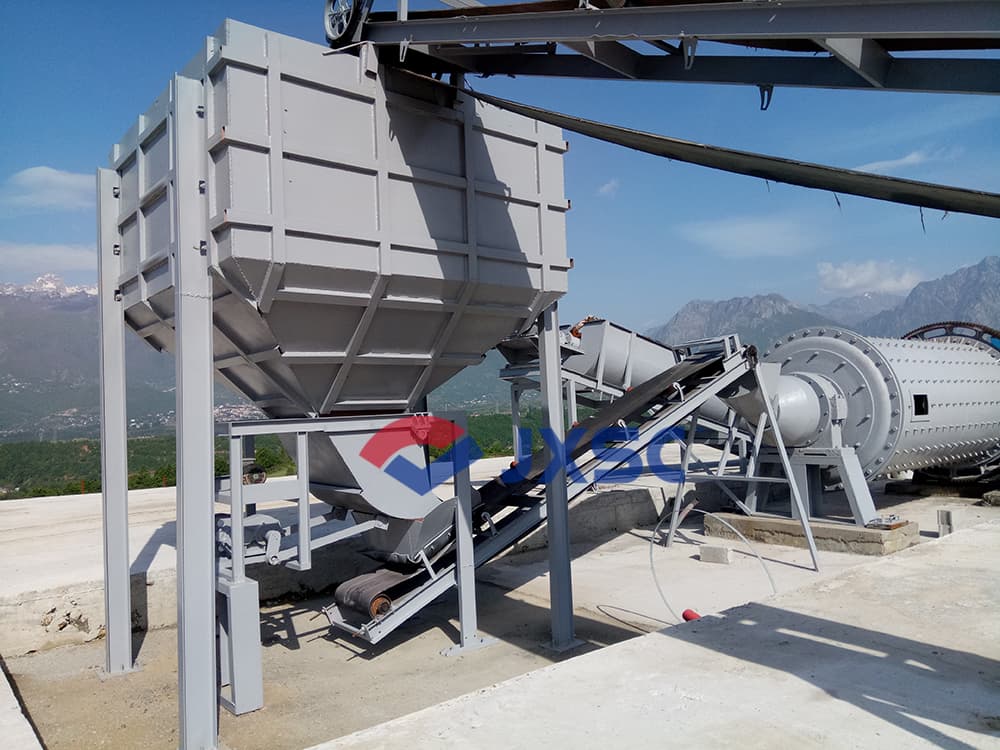
5. Large fluctuation of slurry concentration
Problem manifestation:
● Concentration fluctuation range > ±3%, cyclone classification efficiency decreased by 20%
Cause analysis:
1. Unstable ore feed: belt scale accuracy error > 2%
2. Lag in water replenishment control: manual adjustment response time > 5 minutes
3. Ore moisture change: original ore moisture content fluctuation > 2%
Solutions:
1. Intelligent control system:
● Using PID algorithm to automatically Adjust the amount of water replenishment (control cycle <10 seconds)
●Install a microwave moisture meter to monitor the moisture content of the ore in real time
2. Equipment upgrade:
●Replace a high-precision nuclear scale (error <0.5%)
●Use a pneumatic control valve (adjustment accuracy ±0.5%)
6. Typical case reference
Case: A copper mine
●Problem: The mill processing capacity dropped from 135t/h to 110t/h, and the -200 mesh content dropped from 68% to 55%
●Solution:
1. The steel ball ratio was adjusted from Φ100:Φ80:Φ60=30:40:30 to 40:35:25
2. The diameter of the cyclone sand settling nozzle is reduced from 100mm to 85mm
3. Add dispersant (sodium hexametaphosphate 0.2kg/t)
●Effect: The processing capacity is restored to 130t/h, the -200 mesh content is increased to 70%, and the power consumption is reduced by 1.2kWh/t
Future technical direction
1. Digital twin system: Real-time simulation of the mill operation status through 3D modeling, predicting the liner life error <3 days
2. Intelligent grinding expert system: Based on machine learning algorithm, realize self-optimization of process parameters (response time <30 seconds)
3. Ultrafine grinding technology: vertical mill (such as VXP Mill) achieves -10μm ratio> 90%, energy consumption <25kWh/t
The optimization of the grinding process needs to be systematically considered from the three aspects of “ore properties-equipment parameters-process control”. It is recommended that enterprises establish a grinding efficiency KPI system (such as mill operation efficiency ≥85%, ton ore cost ≤ design value 110%), and conduct regular process audits and equipment health assessments to achieve stable and efficient production.
JXSC has 38 years of experience in the mining industry, and many experienced engineers provide professional technical support to customers. We focus on providing turnkey solutions and full equipment sales services for mining. Over the years, we have served hundreds of customers at home and abroad. Please send us your mining information. JXSC can provide more accurate suggestions based on your specific situation.
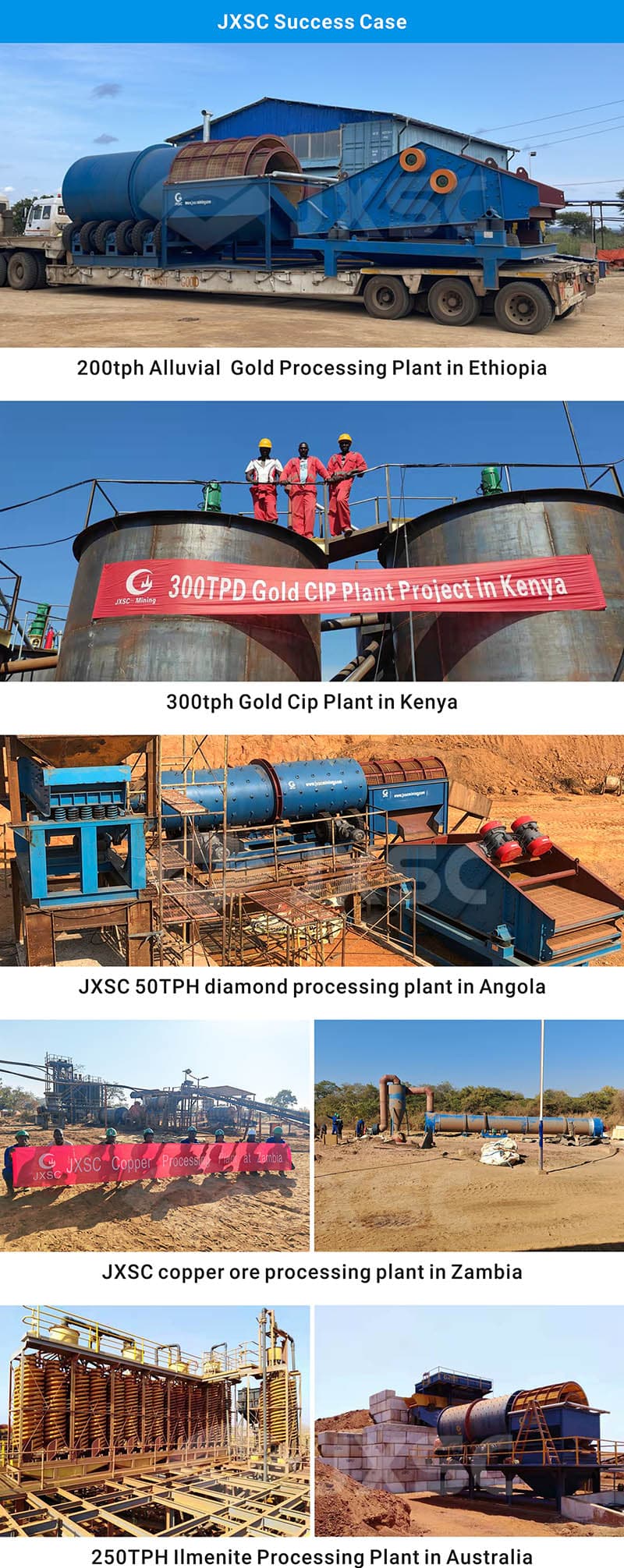