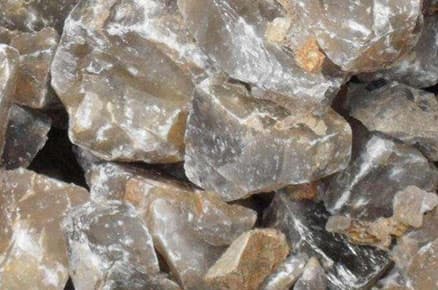
The main beneficiation processes for barite are hand selection, gravity separation, magnetic separation, flotation, calcination purification, and leaching purification. The beneficiation of barite ore associated with sulfide ore usually uses flotation or a gravity separation-flotation combined process to recover barite after removing the sulfide ore.
1. Hand selection
For high-grade barite ore, after coarse crushing, it can be manually sorted according to the color and gloss difference between it and the associated ore. This method is usually carried out through the belt for transporting ore after crushing. It is simple to operate and low in cost, with low equipment dependence, but it has high requirements for ore quality.
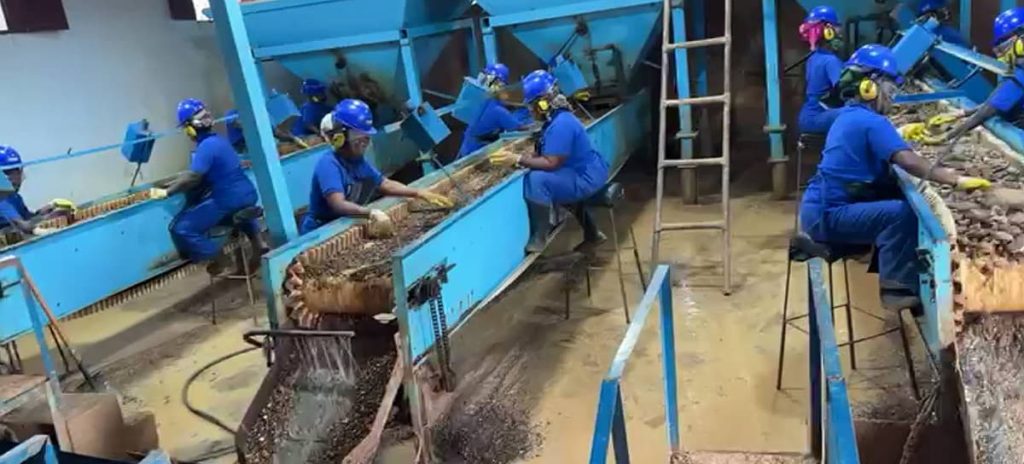
2. Gravity separation
After the original ore is washed, screened, crushed graded, and deslued, it can be re-selected by jigging, shaking table, spiral classification, or heavy medium to select barite concentrate.
Jigging machine: suitable for processing materials with a particle size of less than 30mm and ideal for the sorting of larger particle ores.
Shaking table: suitable for materials with a particle size of less than 2mm, with a high recovery rate, but a small processing volume.
Spiral chute: suitable for processing slurry with a particle size of less than 0.3mm, with a large processing capacity and a small footprint.
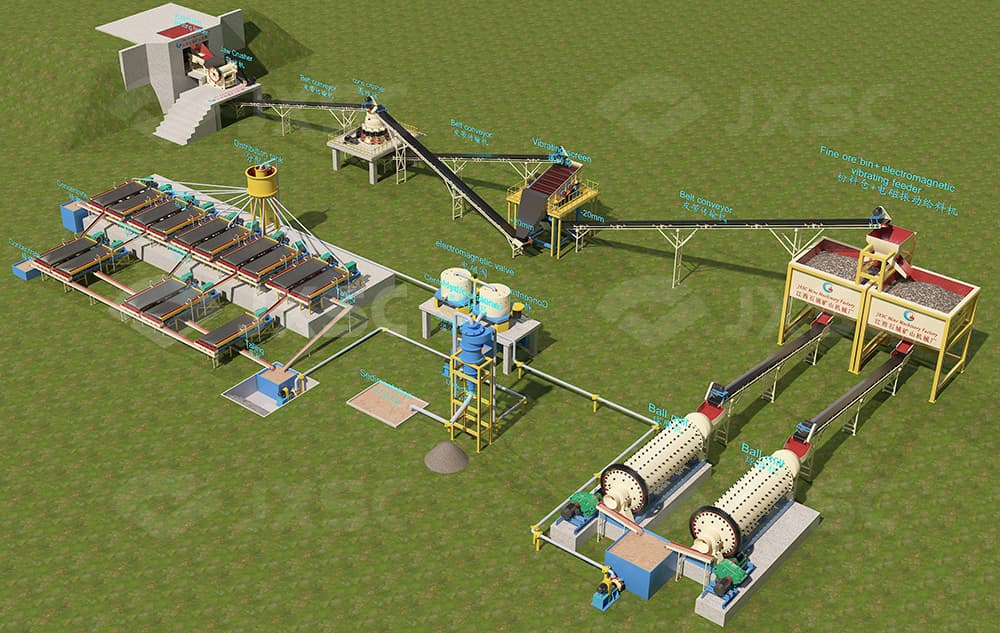
3. Flotation separation
Flotation uses the difference in the surface physical and chemical properties of barite and associated minerals for sorting. Because barite is often closely associated with minerals such as fluorite, calcite, and quartz, and its grade is low, the embedded particle size is fine, and the composition is complex, it is difficult to effectively separate it through traditional gravity separation processes. Flotation can handle a variety of complex embedded types.
Collectors are the key to the effective separation of barite minerals. Common flotation reagents are divided into two categories: anionic collectors (such as alkyl sulfonates and fatty acid sulfates) and cationic collectors (such as advanced amine salts). Due to the diversity of associated minerals, a single flotation reagent often cannot achieve the ideal effect, so a combination of reagents is usually used to improve the flotation effect. For the flotation separation of barite-fluorite ore, the use of inhibitors is a common solution in the industry, including polymerized carbohydrates, inorganic salts, and mixed inhibitors.
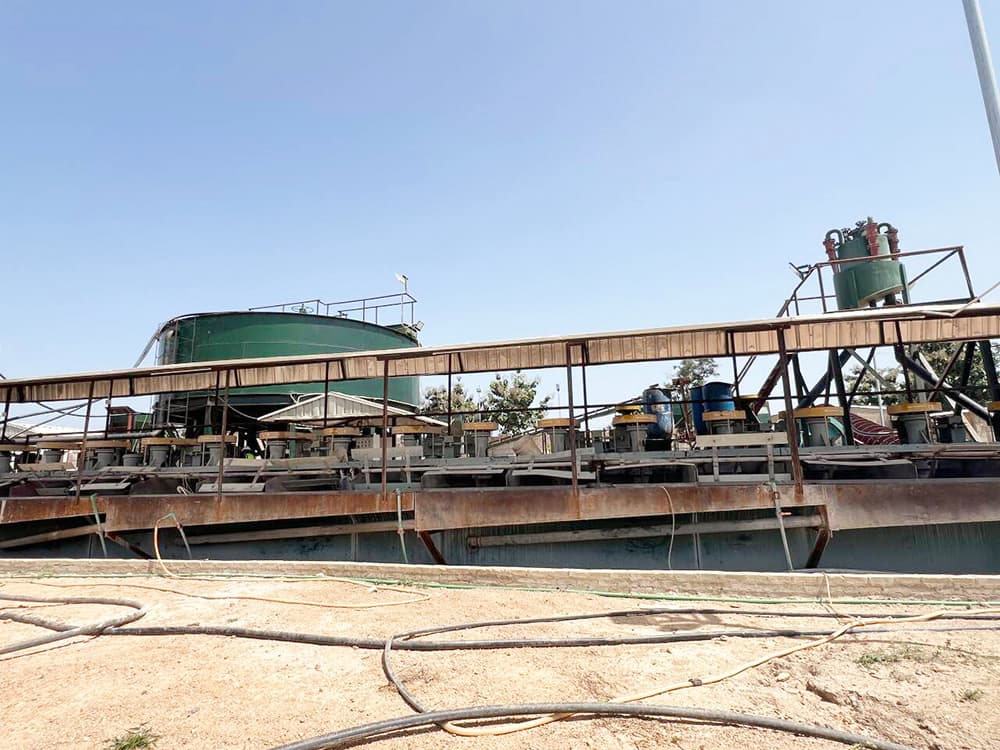
4. Magnetic separation
Magnetic separation is usually not used as the main separation method for barite, but focuses on pre-selection, mainly used to remove iron oxide mineral impurities in barite, such as siderite.
5. Calcination and purification
During the mineralization process, barite minerals may be mixed with impurities such as Fe2O3, TiO2, and organic matter. These impurities will affect the color and purity of barite and reduce its application value. By calcining, impurities that decompose or volatilize at high temperatures can be removed, thereby improving the whiteness and purity of barite.
6. Leaching and purification
Leaching and purification are mainly used to remove carbon and colored impurities in barite, which will affect the whiteness and application prospects of the concentrate. Common leaching and purification methods include acid leaching, redox method and organic acid complex method.
In actual production, the beneficiation and purification methods of barite should be reasonably selected according to the mine type, ore properties, mine scale and final use.
JXSC has 38 years of experience in the mining industry, and many experienced engineers provide professional technical support to customers. We focus on providing turnkey solutions and full equipment sales services for mining. Over the years, we have served hundreds of customers at home and abroad. Please send us your mining information. JXSC can provide more accurate suggestions based on your specific situation.
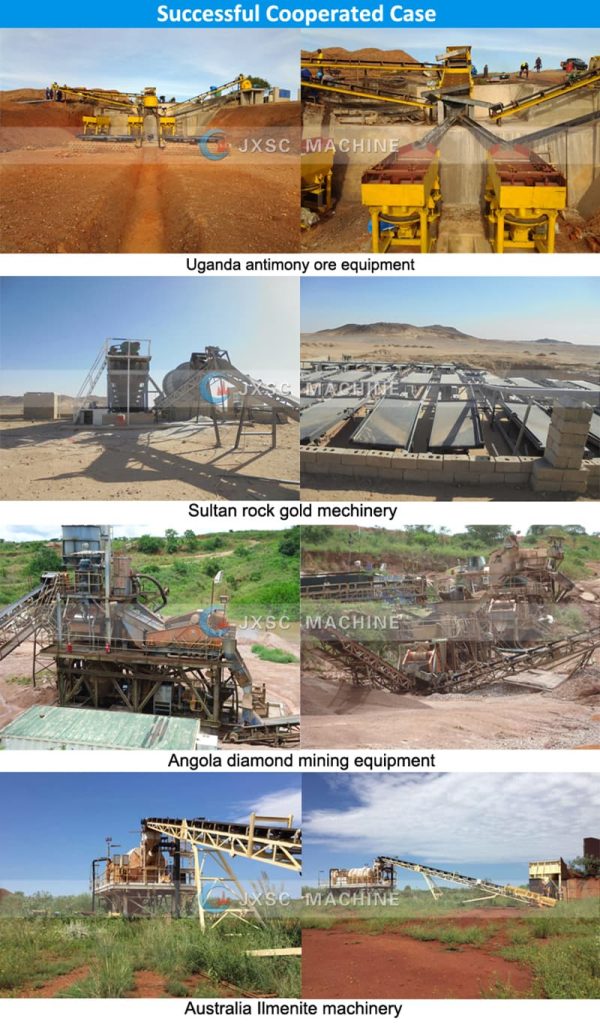