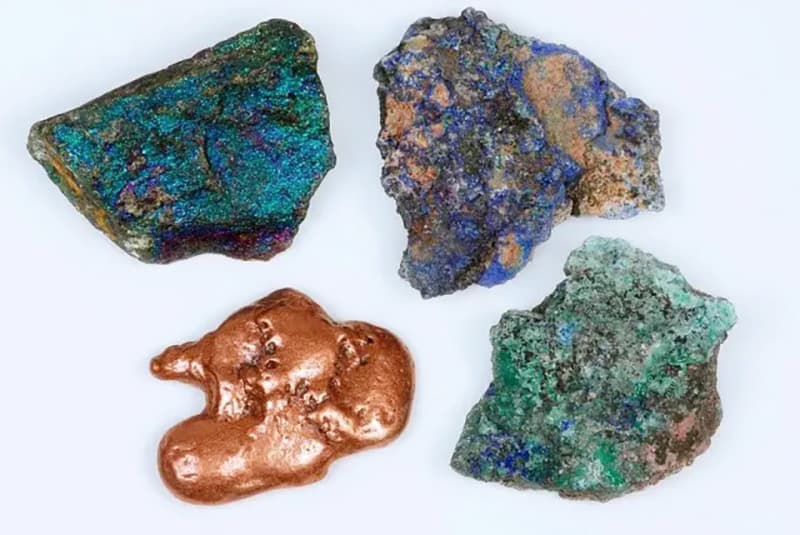
Copper Beneficiation refers to a series of physical and chemical processes that extract and concentrate copper minerals from raw ore, ultimately producing high-grade copper concentrate suitable for smelting and refining. Beneficiation is a critical step in copper production, enabling low-grade ores (typically containing 0.2-2% Cu) to be upgraded to 20-40% copper content, meeting industrial requirements for downstream metallurgical processes and achieving economic utilization.
1. Occurrence Types of Copper Minerals and Basic Beneficiation Methods
1) Copper minerals exist in nature primarily in three forms:
- Sulfide Copper Ores: Such as chalcopyrite (CuFeS₂) and chalcocite (Cu₂S), accounting for over 70% of global copper resources, with good floatability.
- OxideCopper Ores: Such as malachite (Cu₂CO₃(OH)₂) and azurite (Cu₃(CO₃)₂(OH)₂), which have strong surface polarity and poor floatability.
- Native Copper: High purity but limited reserves.
2) Basic Beneficiation Methods for Copper Ores
Depending on ore characteristics, three primary methods are used:
- Flotation: Separates minerals based on hydrophobicity differences adjusted by reagents, achieving 85-95% recovery rates.
- Gravity Separation: Utilizes density differences, suitable for coarse-grained ores but ineffective for fine particles.
- Magnetic Separation: Separates magnetic gangue minerals like magnetite.
Table 1: Comparison of Beneficiation Methods for Different Copper Ores
Ore Type | Suitable Method | Concentration Grade (Cu%) | Recovery Range |
Sulfide Copper | Flotation | 20-40% | 85-95% |
Oxide Copper | Sulfidization Flotation/Leaching | 15-30% | 70-90% |
Mixed Ores | Selective/Mixed Flotation | 18-35% | 80-92% |
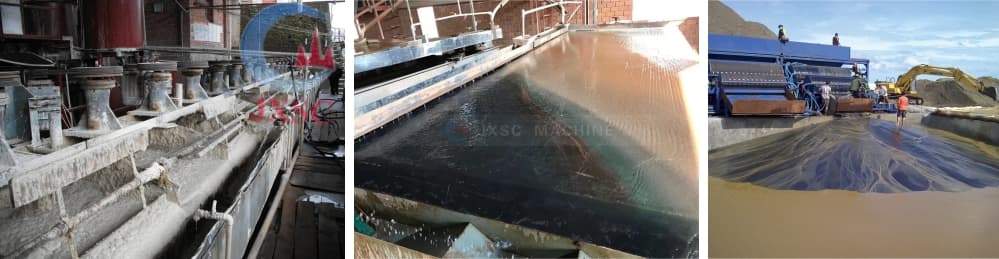
2. Copper Beneficiation Processes and Key Equipment
1) Preprocessing
Pre-treatment is the foundation of beneficiation, consisting of:
● Crushing & Screening: Three-stage closed-circuit process (jaw crusher for coarse crushing + cone crusher for medium/fine crushing) to reduce ore size to 12-15 mm.
● Grinding & Classification: Closed-circuit system with ball mills and hydrocyclones, achieving 70-85% -200 mesh fineness.
● Classification Optimization: Modern plants use high-efficiency hydrocyclones, improving classification efficiency by over 20%.
2) Flotation Process for Sulfide Copper Ores
A typical sulfide copper flotation flow includes:
● Slurry Conditioning: pH adjustment to 10-12 (lime suppresses pyrite).
● Reagent System:
– Collectors: Amyl xanthate + black drug combo (50-150 g/t).
– Frothers: MIBC or pine oil (10-30 g/t).
● Flotation Circuit: One roughing, two scavenging, three cleaning stages. Flotation columns now replace mechanical cells, improving concentrate grade by 2-5%.
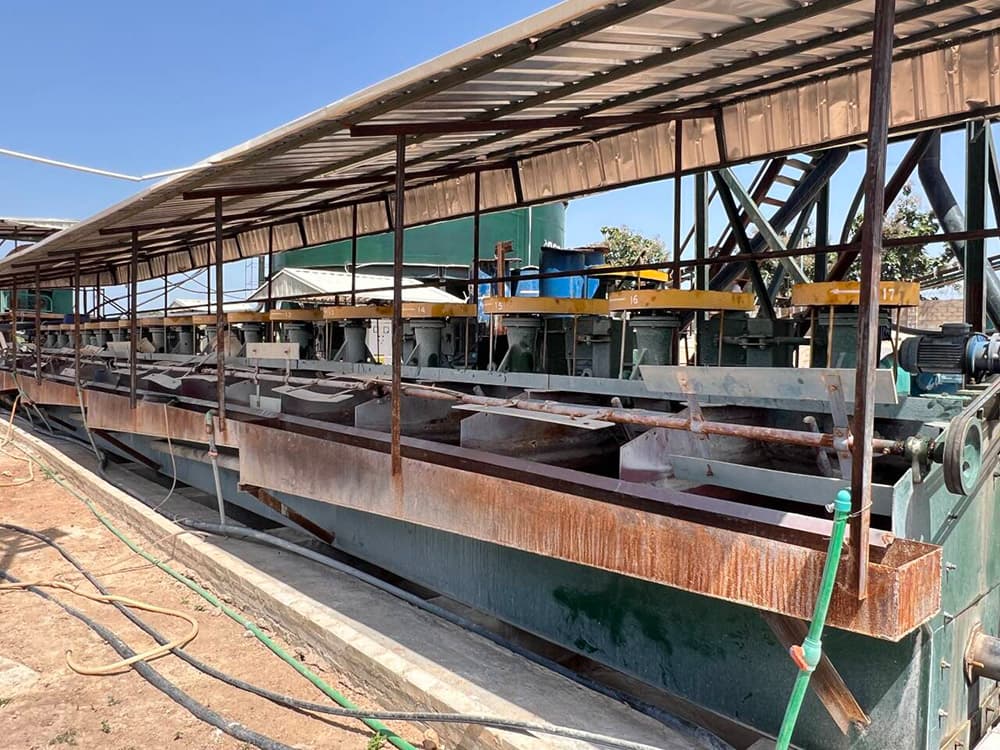
3) Oxide Copper Ore Treatment
Challenging oxide ores require combined processes:
- Sulfidization Flotation:Na₂S sulfidization followed by xanthate flotation for malachite.
- Leach-Solvent Extraction-Electrowinning (L-SX-EW):
– Heap leaching: For 0.3-1% Cu ores (50-70% recovery).
– Agitation leaching: High-grade ores (over 90% recovery).
- Ammonia leaching:For alkaline gangue ores to reduce acid consumption.
3. Advances in Beneficiation of Complex Copper Resources
1)Porphyry Copper-Molybdenum Separation
Porphyry deposits supply 60% of global copper. Key innovations:
● Regrinding of Bulk Concentrate: Fineness -45 μm ≥90%, enhancing Cu-Mo separation.
● Novel Depressants: STY composite depressant (1200 g/t) + lime (4500 g/t), replacing cyanides.
● Flotation Columns: Microbubble columns increase Mo grade to 57% in concentrates.
2) Copper-Nickel Ore Separation
Main approaches:
●Direct Selective Flotation: For Cu/Ni >2 ratios; simple but low Ni recovery (~65%).
● Bulk-Separation Flotation:
-Bulk Cu-Ni flotation (pH 9-10).
-Ni depression in bulk concentrate (Na₂S + activated carbon).
●High-Grade Matte Process: For finely disseminated ores, reducing energy consumption by 30%.
3) Recovery of Associated Gold and Silver
Optimization measures:
● Grinding Optimization: Liberation of Au/Ag-bearing minerals.
● Reagent Adjustment: Low-cyanide (5-10 g/t) or non-toxic depressants (DT-2#).
● Gravity-Flotation Hybrid: Shaking tables for coarse gold; Ag recovery increased from 50% to 65% in some mines.
4. Emerging Trends in Flotation Reagents: Sustainability & Innovation
1) Key Equipment Selection
● Crushing: Cone crushers for plants >1000 t/d.
● Grinding:
–Coarse grinding: Grate-type ball mills (prevent overgrinding).
–Fine grinding: Overflow ball mills + hydrocyclones.
● Flotation: KYF-40 aerated cells for roughing; XCF-16 for cleaning.
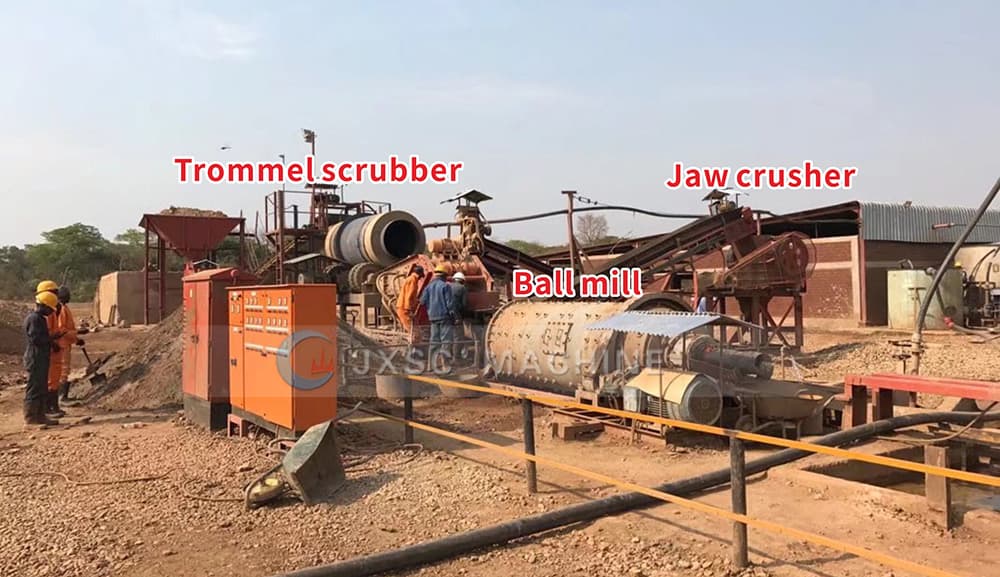
2) Case Study: Troubleshooting at a 4500 t/d Plant
● Issue: Recovery dropped sharply at 187 t/h throughput.
●Root Cause: Hydrocyclone pressure fluctuations due to undersized spigot (original Φ75 mm).
● Solutions:
–Installed Φ90 mm spigot.
–Optimized steel ball ratio (Φ100 mm balls: 85%).
–Adjusted reagent addition points.
● Result: Cu recovery restored to 92.7%, achieving design targets.
5. Future Technological Directions
Copper beneficiation has evolved into a comprehensive system adaptable to diverse deposit types, with future advancements focusing on four key priorities: efficient separation of complex polymetallic resources, large-scale industrial adoption of eco-friendly processes to minimize environmental impact, integration of intelligent control systems for plant automation and optimization, and full-component resource utilization to recover valuable byproducts from tailings. These innovations address the growing demand for sustainable mineral processing while maximizing economic returns from increasingly challenging ore bodies.