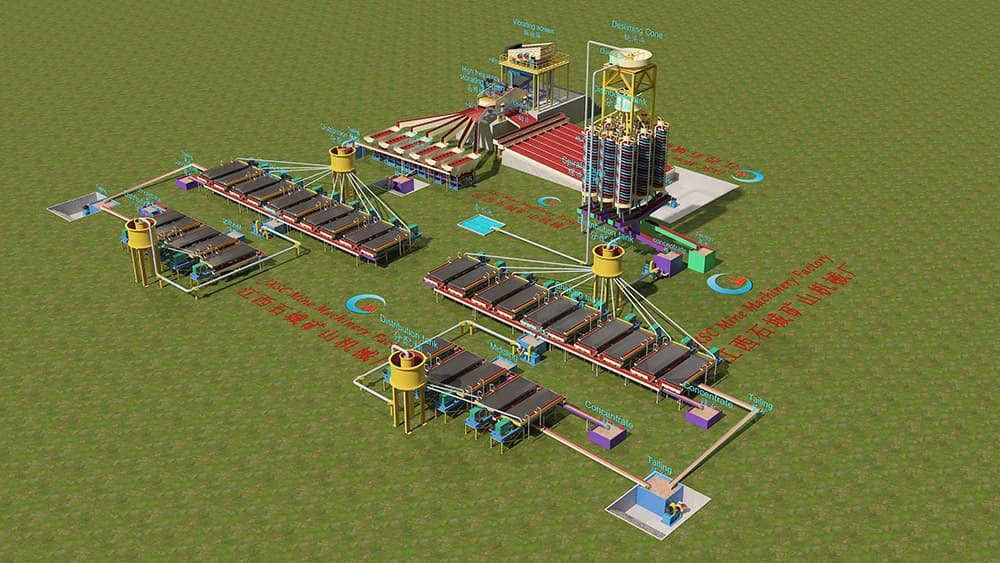
Wolframite is mainly composed of tungsten iron ore (FeWO₄) and manganese tungsten ore (MnWO₄), with high density (about 7.1 g/cm³) and brittleness. Wolframite has a high specific gravity, so generally, gravity separation can obtain a good recovery rate. At the same time, the particle size distribution of wolframite is wide in the natural state, and the recovery of fine-grained minerals is difficult. Therefore, special attention should be paid to particle size control in the gravity separation process.
Gravity Separation Process
Gravity separation mainly relies on the density difference of minerals to separate useful minerals from waste rocks through gravity separation equipment. Its basic principles include:
Gravity separation: Through slurry movement in the gravity field, mineral particles are separated according to their different densities, thereby achieving separation.
Fluid dynamics: In gravity separation equipment, factors such as water flow speed, slurry concentration, and particle movement trajectory will affect the separation effect.
In the processing of wolframite, gravity separation is widely used in roughing, concentrating, and other stages, which can effectively improve the recovery rate of tungsten and improve the grade of concentrate.
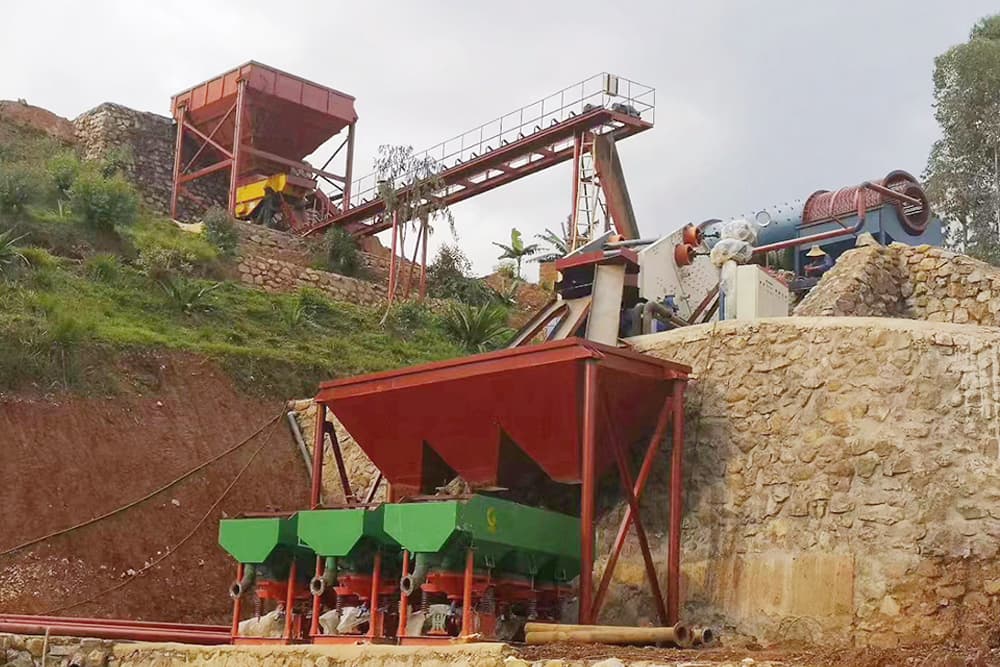
Wolframite Gravity Processing Plant
The process of the wolframite gravity processing plant mainly includes roughing, grinding, gravity, concentration, and fine mud treatment.
1. Roughing
The roughing stage is mainly pre-enriched by hand selection. Hand selection is a simple and effective beneficiation method that can perform preliminary sorting according to the appearance characteristics and physical properties of the ore. According to the different properties of wolframite ore, the beneficiation plant can choose forward hand selection, reverse hand selection or a combination of the two for roughing.
2. Grinding
Tungsten is brittle and easy to over-grind and over-crush during the grinding process. At this stage, the wolframite grinding equipment mostly uses rod mills, one is to avoid over-grinding, and the other is to ensure that the particle size of the grinding product is more uniform and meets the particle size requirements for gravity selection. The common wolframite gravity process grinding stage mostly adopts one-stage grinding, one-stage rod mill + medium ore mill, two-stage grinding, and other processes.
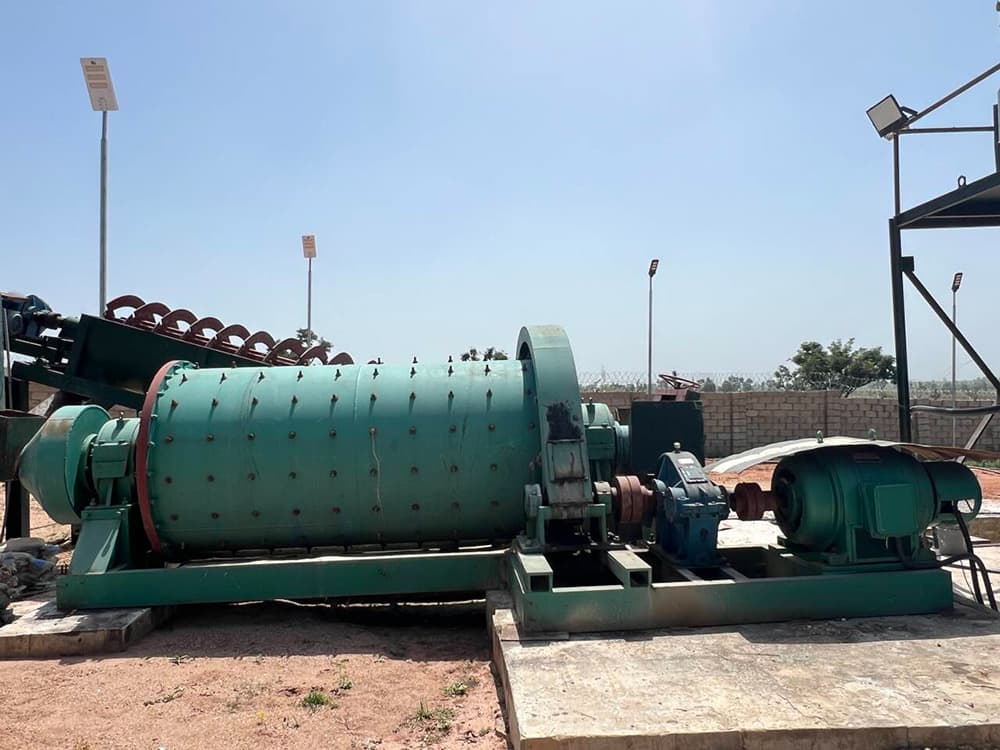
3. Gravity separation
The gravity separation stage is the core of the wolframite beneficiation process and is usually separated by jigging, shaking table, and spiral chute.
Jig separator: Suitable for coarse and medium-sized wolframite, it can separate minerals by combining the up and down movement of the moving screen with the water flow. The coarse-sized tailings of the jig enter the mill for re-grinding, and the fine-sized tailings enter the shaking table for separation.
Shaking table: Suitable for the separation of fine-sized minerals. The tailings of the shaking table are discharged, and the medium-sized ore enters the mill for re-grinding and re-selection.
The concentrates of the jig and shaking table enter the concentration.
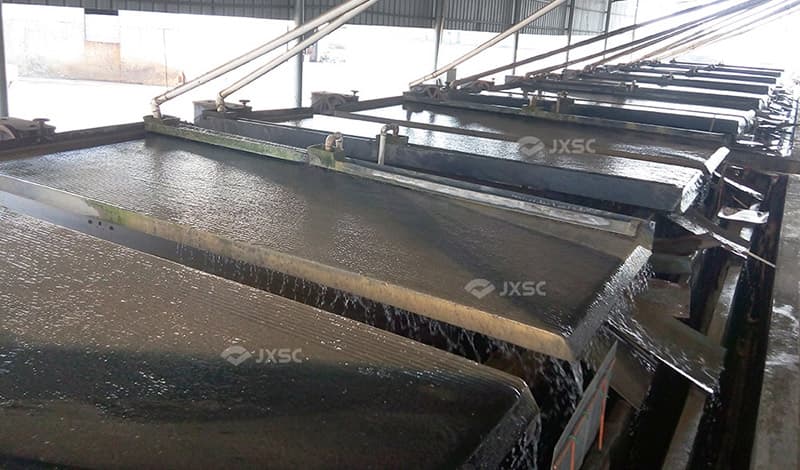
4. Concentration
The wolframite concentrate after gravity separation often contains other associated non-ferrous metals, which need to be refined to improve the quality. Concentration adopts a variety of separation processes such as floating gravity combined or floating gravity magnetic combined. The sulfide ore is removed by table flotation (a beneficiation method combining flotation and shaking table) and flotation of coarse and fine particles. The table flotation and machine flotation sulfide ore are combined to enter the flotation separation of sulfide ore. The table flotation and machine flotation wolframite are further re-selected to produce wolframite concentrate. If the wolframite concentrate contains scheelite and cassiterite, wolframite concentrate, scheelite concentrate, and tin concentrate are selected by re-selection flotation or re-selection flotation magnetic separation combined process.
5. Fine mud treatment
The fine mud treatment stage mainly includes desulfurization and the combined selection of multiple processes such as re-selection, flotation, and magnetic separation according to the properties of fine mud materials to recover tungsten minerals and associated metal minerals. Through a reasonable combination of processes, the recovery rate of resources can be effectively improved and the generation of waste can be reduced.
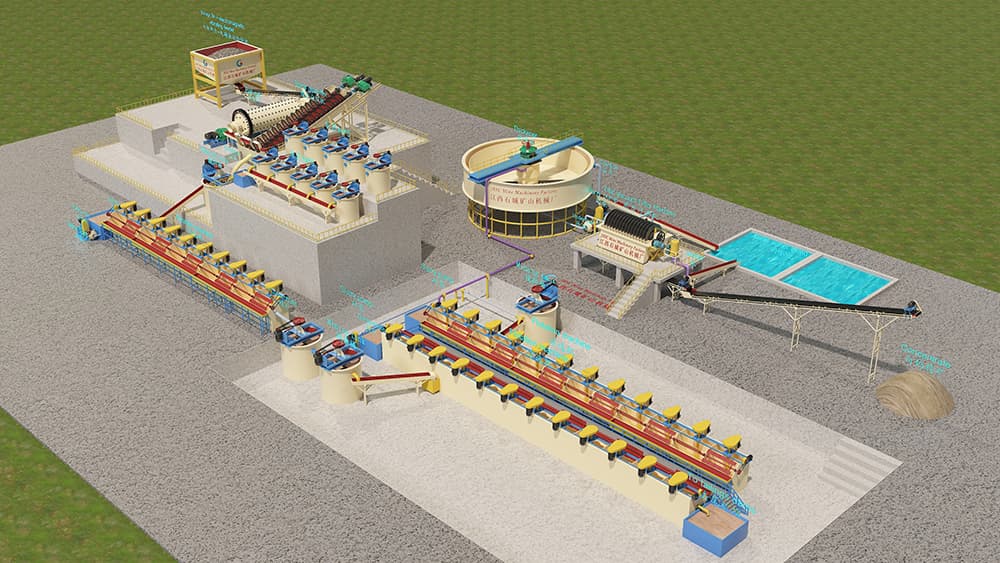
The re-selection process of wolframite plays an important role in the development of tungsten resources. By reasonably selecting and optimizing the processes and equipment of each beneficiation stage, the recovery rate and economic benefits of tungsten ore can be improved. In actual production, it is recommended to conduct mineral tests, combine the properties and separation particle size of wolframite, and select appropriate mineral processing equipment.
JXSC has 38 years of experience in the mining industry, and many experienced engineers provide professional technical support to customers. We focus on providing turnkey solutions and full equipment sales services for mining. Over the years, we have served hundreds of customers at home and abroad. Please send us your mining information. JXSC can provide more accurate suggestions based on your specific situation.
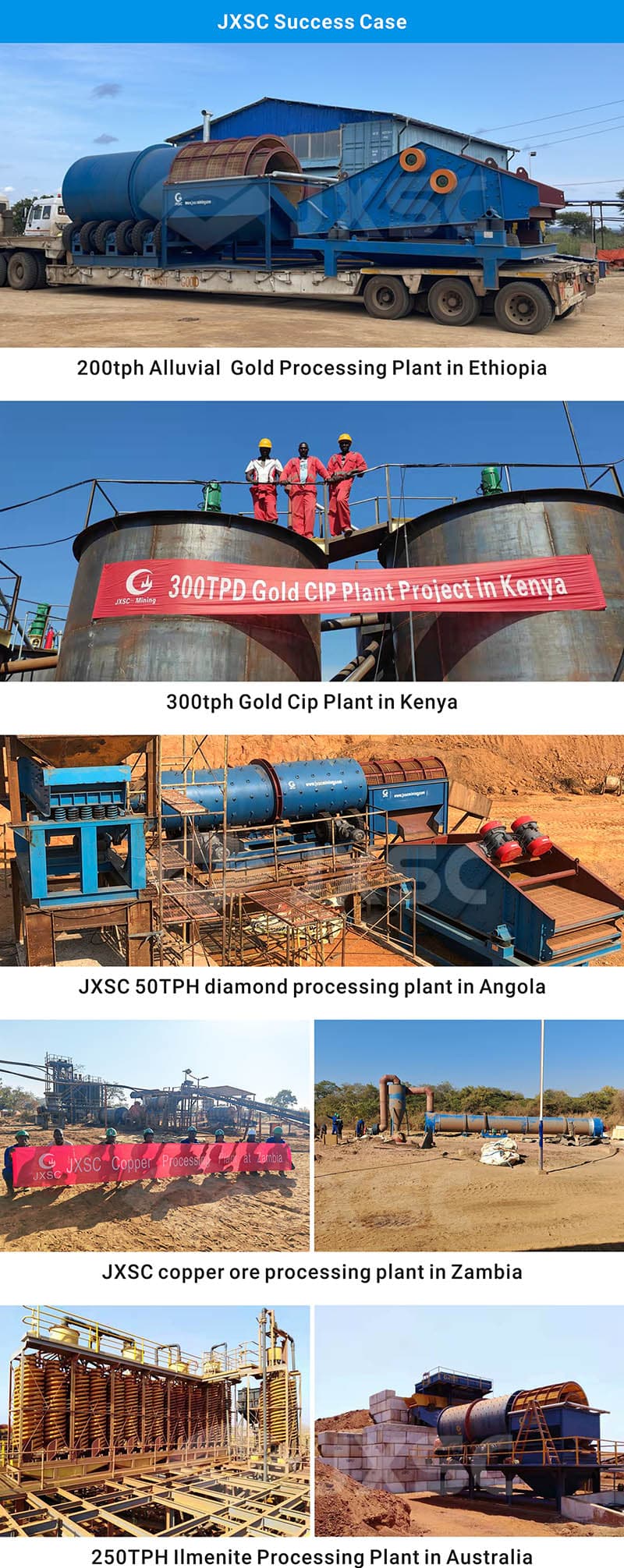