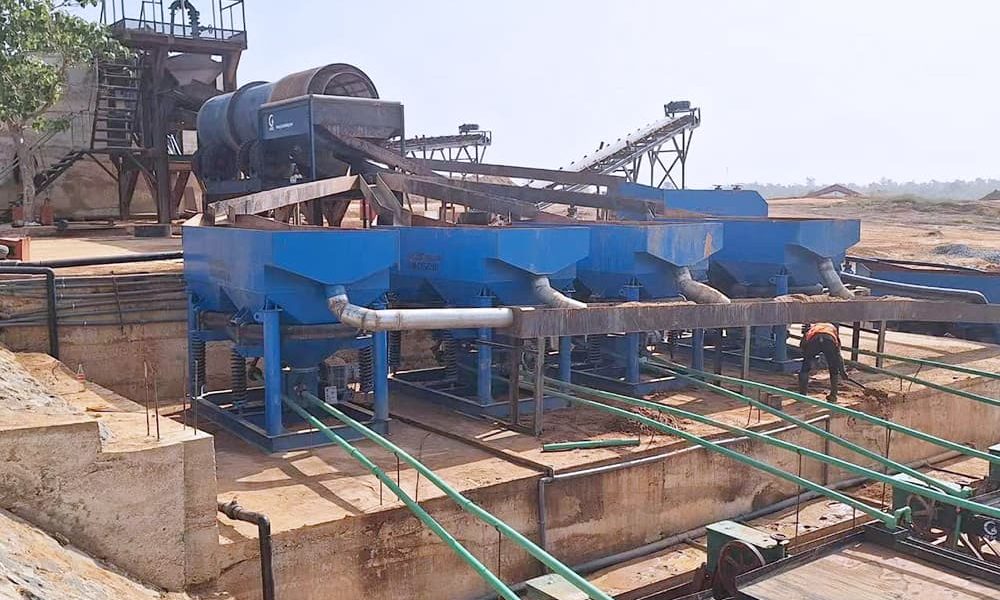
The JXSC company provided a full set of 100TPH alluvial tin ore processing plants to Nigeria. The whole plant equipment includes a feeder, trommel scrubber, jig separator, shaking table, three-disc dry magnetic separator, spiral dewatering machine, dewatering screen, and belt conveyor.
Process Description
Raw ore conditions and customer’s requirements:
1) Raw materials contain sticky clay.
2) Tin concentrate particle size 0-10mm which accounts for 60% of raw materials (0-2mm account for 80% and 2-10mm account for 20% of concentrate ore).
3) Maximum ore feeding size is 400mm.
4) Processing capacity is 100 tons per hour.
5) Customer requires dewatering tailing ore.
6) Customers require magnetic separation after gravity separation.
According to the above ore conditions and the customer’s requirements, we have designed the most effective process flowchart for this tin plant.
Process flowchart description:
1. Washing system
Raw materials are evenly fed into a trommel scrubber by a vibrating feeder for washing off the clay and screening out oversized waste stones. The vibrating feeder is equipped with a grizzly bar, and a gap of 70mm to remove over 70mm of big waste stone. The trommel scrubber is equipped with two layers of screen 2 mm and 10mm, to sieve out 0-2 mm, 2-10mm, above 10mm waste stone.
Above 70mm big waste stones from the vibrating feeder and above 10mm small waste stones from the trommel scrubber are sent to far places by belt conveyor.
2. Gravity separation by jig separator and shaking table
0-2mm slurry ore from Trommel scrubber auto flow to jig separator by gravity for primary concentration tin concentrate. Tin concentrates from the first stage of jigs are sent to shaking tables for further upgrading. In order to improve the recovery rate, middling of shaking tables is sent to the second stage of shaking table for again process to recover more tin concentrate.
2-10mm from trommel scrubber auto flow to another jig separator by gravity for primary concentration tin concentrate. Its tin concentrate goes to the secondary stage of the jig separator for fine separation, in order to improve tin grade. This is required by the customer.
3. Magnetic separation
This customer has a high requirement for tin concentrate grade, so at last all 0-2mm tin concentrates are sent to three disc dry magnetic separators for further removing other impurities and improving tin grade.
4. Tailing dewatering system
All tailings from jig separators are sent to a spiral dewatering machine for dewatering to make the tailings kind of dry and can be sent by belt conveyor. The tailing water can be recycled and reused in this plant.
All tailings from shaking tables are sent to the hydrocyclone, overflow from the cyclone is clear water, and underflow goes to the dewatering screen for further dehydration. Over the screen is a kind of dried tailing sand, under the screen is mud water which goes to the settling pond.
The whole process flowchart includes four parts: washing system, gravity separation system, magnetic separation, and tailing dewatering system. After processing by this plant, finally customers can get a very high grade of tin concentrate. At the same time, tailing water can be recycled and reused in this plant. So this is a very efficient plant.