Roller Electrostatic Separator
Capacity:1-2 t/h
Applicable materials:It is often used for separating various minerals with different conductivity such as cassiterite, scheelite, zircon, monazite, andalusite, rutile, quartz, as well as scrap metal and non-metallic materials.
Description
Roller electrostatic separators separate particles based on their conductivity and charge. The main applications are in separating conductive and non-conductive materials, such as mineral processing, recycling, and environmental remediation. It can realize different materials’ purification, recovery, or concentration; providing an efficient and environmentally friendly solution for separating conductive materials. The multi-layer structure design of the roller electrostatic separator can complete rough selection, selection, sweep selection and mid-range ore re-selection at one time in the machine as needed.
Advantages
- Suitable for s a variety of materials separating, including minerals, plastics, and e-waste.
- The roller electrostatic separator does not involve water or chemicals and has excellent environmental benefits.
- It can effectively separate fine particles that are difficult to separate using other methods.
Principle
The working principle of the roller electrostatic separator is frictional electrification and electrostatic separation. The material to be separated is fed into a roller conveyor system, which rotates and transports the material during the separation process. Triboelectric charging occurs when the material contacts the drum, resulting in positive and negative charges on the different particles. These electrodes apply an electric field to charged particles, causing them to be attracted or repelled depending on their charge. The charged particles are guided into a separation chamber, where an electric field causes them to move in different directions, thereby achieving separation.
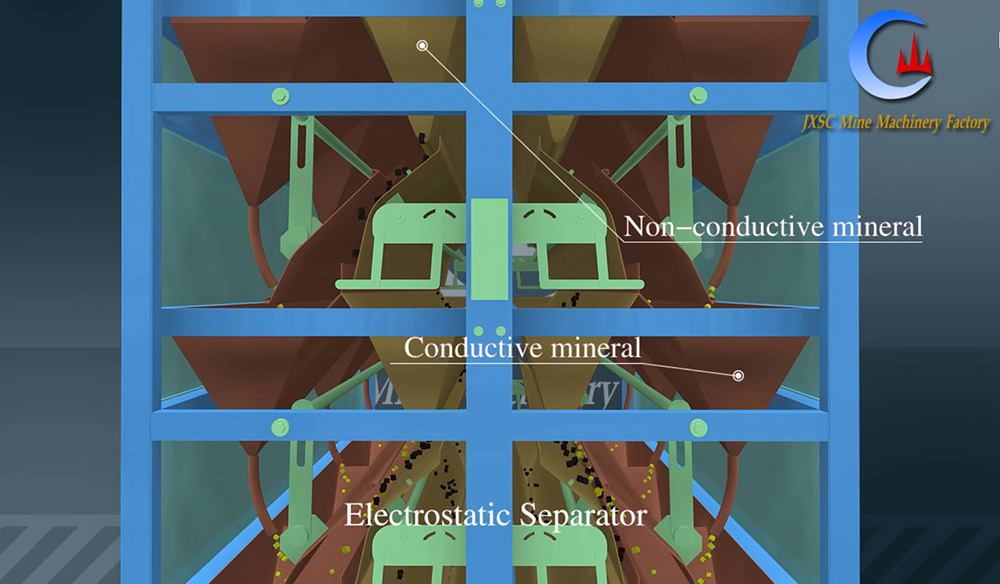
Specification
Model | JXSC-1615 | JXSC-1815 | JXSC-2215 |
Roller Size (mm) | 160*1500 | 180*1500 | 220*1500 |
Feeding size(mm) | 0-2 | 0-2 | 0-2 |
Double roller capacity(t/h) | 1 | 1.5 | 2 |
Four roller capacity(t/h) | 1.5 | 2 | 3 |
Double roller power | 1.5 | 1.5 | 1.5 |
Four roller power | 3 | 3 | 3 |