Raymond Mill
Widely used in the medium and fine crushing operations in industries such as metallurgy, mining, chemical, cement, construction, refractory materials, and ceramics.
Capacity: 0.15-9 t/h
Applicable materials: fluorite, calcite, feldspar, talc, marble, limestone, ceramics, and glass.
Description
Raymond mill, also known as Raymond grinder or Raymond machine, is a highly efficient and space-saving equipment compared to ball mills. It performs internal operations for feeding, grinding, and discharging of powders, eliminating dust pollution. It is an excellent alternative to ball mills for ore grinding.
In addition to standalone use, Raymond mills are often combined with other equipment to form independent powder grinding systems. This includes cyclone collectors, dust collectors, bucket elevators, vibrating feeders, jaw crushers, blowers, and main grinding machines. We provide a range of powder grinding equipment from single units to complete systems.
Advantages
- High production efficiency and fine and uniform finished powder.
- High sealing performance, no dust pollution.
- Centralized control electrical system, easy operation.
- Can be matched to form an integrated powder production system, mature machine usage methods.
Principle
Principle
Grinding: Raw materials are fed into the main machine through a feeder. The grinding area is mainly composed of grinding rings and grinding rollers that rotate at high speed next to the grinding rings. The raw materials are ground into powder under the pressure of the grinding rollers and grinding rings in the grinding area. The material after grinding is blown up by a fan and passes through a separator. The particles that meet the requirements are separated and the remaining particles return to the grinding chamber for further grinding.
Finished product conveying system: The discharge valve is installed at the lower end of the powder collector and pulse dust collector. The finished product is discharged from the valve and outputted through a screw conveyor or scraper conveyor, and then sent to the finished product silo through a bucket elevator or other conveying equipment.
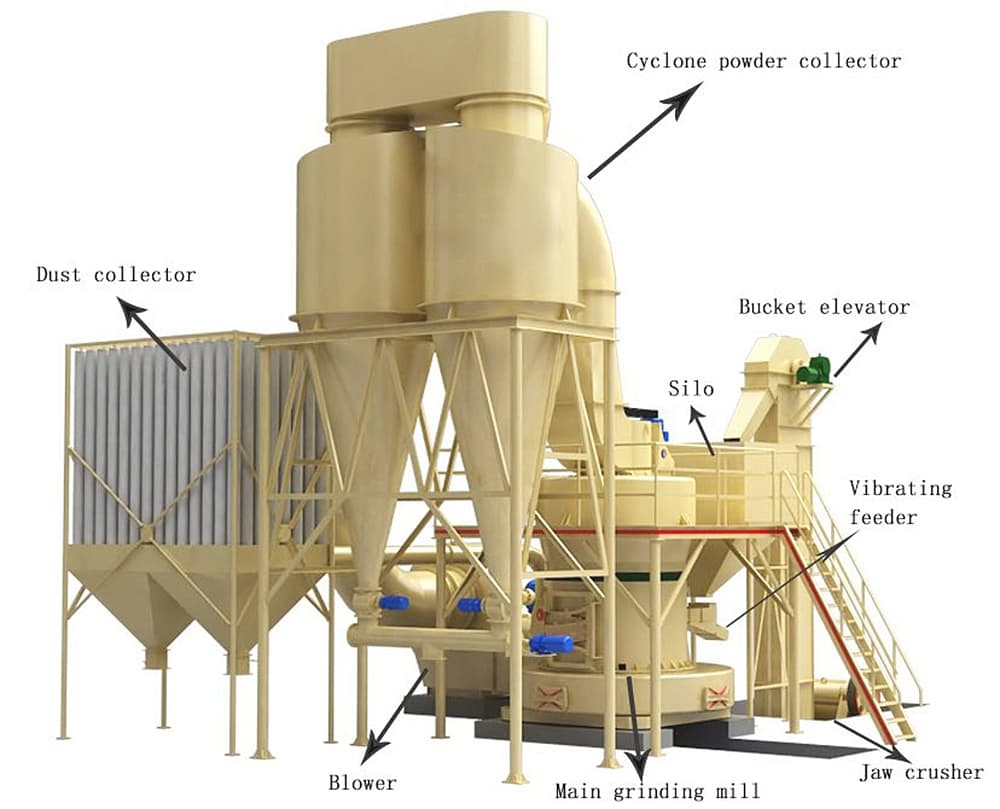
Specification
Model | Grind roller | Grinding ring | Feed size | Output size | Capacity | Motor power | Overall dimension | |||
| Q’ty | Dia. | Height | Outer Dia. | Height |
|
|
|
|
|
3R1410 | 3 | 140 | 100 | 495 | 100 | <8 | 0.613-0.044 | 0.15-1.2 | 14.1 | 3340*2200*3200 |
3R2115 | 3 | 210 | 150 | 726 | 150 | <15 | 0.613-0.044 | 0.28-1.8 | 28.2 | 4480*3100*3970 |
3R2615 | 3 | 260 | 150 | 865 | 150 | <15 | 0.613-0.044 | 0.35-2.8 | 35.7 | 5000*4100*4850 |
3R2715 | 3 | 270 | 150 | 884 | 150 | <15 | 0.613-0.044 | 0.40-3.4 | 42.7 | 5050*4150*4900 |
3R3015 | 3 | 300 | 150 | 965 | 150 | <15 | 0.613-0.044 | 0.45-3.7 | 55 | 5200*4200*4950 |
4R3016 | 4 | 300 | 160 | 990 | 160 | <20 | 0.613-0.044 | 0.6-4.5 | 55 | 5250*5000*5500 |
4R3216 | 4 | 320 | 160 | 1073 | 160 | <25 | 0.613-0.044 | 1.0-5.2 | 72.5 | 7700*7200*8800 |
5R4119 | 5 | 410 | 190 | 1400 | 190 | <30 | 0.613-0.044 | 2.0-9.0 | 157.5 | 7900*8800*9650 |