High Intensity Dry Magnetic Separator
Capacity: 0.01-150 t/h
Applicable materials: iron removal process of manganese ore, hematite, pyrrhotite, limonite, magnetite, feldspar ore, quartz ore and other minerals.
Description
High-intensity dry magnetic separators are powerful and innovative tools for efficiently separating magnetic materials in the mineral processing industry. Able to process large quantities of materials efficiently and quickly while improving the purity and quality of the final product. High-intensity dry magnetic separators are commonly used to separate weakly magnetic minerals such as manganese ore, magnetite, ilmenite, and chromite.
Advantages
- High magnetic field strength can effectively separate weak magnetic materials;
- It operates without water, low operating cost and environmentally friendly magnetic separation equipment;
- Adopting advanced magnetic circuit design and cooling system to provide high performance and low power consumption;
- Designed with customizable settings and automated controls to meet continuous production requirements.
Principle
High-intensity dry magnetic separators primarily utilize the powerful magnetic field generated by a series of rare earth magnets within the separator. The materials are fed into the vibrating feeder and evenly distributed on the conveyor belt. The conveyor belt then carries the material through a high-intensity magnetic field, where the iron particles are attracted and separated from the non-magnetic material. The magnetic particles are affected by a strong magnetic field, attracted and captured on the surface of the rotating drum, and then discharged into a separate container. The non-magnetic material, on the other hand, continues along the conveyor belt for further processing.
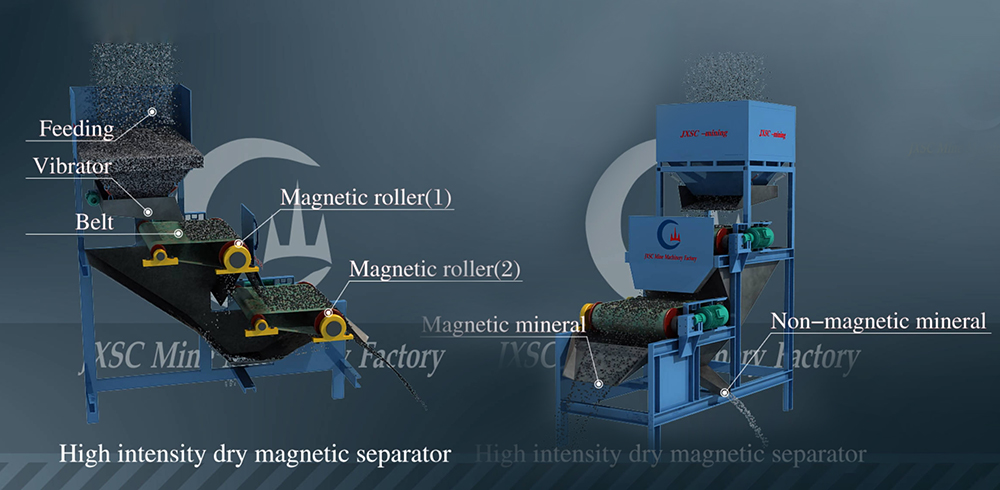
Specification
Model | Background Magnetic Field | Feeding Material Size | Feeding Material Density | Dry Ore Capacity | Pulp Throughput | Excitation Power | Swivel Power | ulsating Power | Swivel Diameter | Water Consumption | Host Machine Weight | Large Part Weight | External Dimensions |
(T) | (mm) | (t/h) | (m³/H) | (KW) | (KW) | (KW) | (mm) | (m³/h) | (t) | (t) | (mm) | ||
LH- 500 | 0.6-1.4 | 0-1 | 10-30% | 0.01–0.05 | 0.25–0.5 | 6–20 | 0.18 | 0.55 | 500 | 0.65–1.4 | 1.5–4 | 0.25–0.5 | 1800x1400x1320 |
LH- 750 | 0.6-1.4 | 0-1 | 10-30% | 0. 1–0.25 | 1–2 | 8–30 | 0.75 | 1.5 | 750 | 1.4–2.5 | 3.5–8 | 0.5–1.1 | 2000x1360x1860 |
LH- 1000 | 0.6-1.4 | 0-1.2 | 10-30% | 2–4 | 12.5–20 | 10–40 | 1.1 | 2.2 | 1000 | 8–12 | 7–15 | 2–3.3 | 2700x2000x2400 |
LH- 1250 | 0.6-1.4 | 0-1.2 | 10-30% | 5–10 | 20–50 | 12–50 | 1.5 | 3 | 1250 | 12–20 | 11–24 | 3.5–5 | 3200x2340x2700 |
LH- 1500 | 0.6-1.4 | 0-1.2 | 10-30% | 10–15 | 50–100 | 15.5–60 | 3 | 3 | 1500 | 20–30 | 20–34 | 5–7 | 3600x2900x3200 |
LH- 1750 | 0.6-1.4 | 0-1.2 | 10-30% | 15–20 | 75–150 | 23–72 | 4 | 4 | 1750 | 30–50 | 28–45 | 9–15 | 3900x3300x3800 |
LH- 2000 | 0.6-1.4 | 0-1.2 | 10-30% | 20–30 | 100–200 | 29–85 | 5.5 | 7.5 | 2000 | 50–100 | 39–60 | 13–20 | 4200x3550x4200 |
LH- 2500 | 0. 6-1.4 | 0-1.2 | 10-30% | 45–60 | 200–400 | 37–98 | 11 | 11 | 2500 | 100–150 | 83–125 | 18–32 | 5800x5000x5400 |
LH- 3000 | 0.6-1.4 | 0-1.2 | 10-30% | 80–120 | 350–650 | 48–110 | 18.5 | 18.5 | 3000 | 150–250 | 135–165 | 19–38 | 7600x6500x7200 |
LH- 3600 | 0.6-1.4 | 0-1.2 | 10-30% | 100–150 | 500–750 | 72–180 | 30 | 30 | 3600 | 200–400 | 150–250 | 25–50 | 7700x6500x7600 |