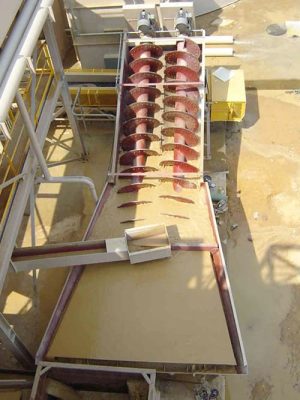
Turnkey Solutions
Kaolin Processing Plant
Kaolin is a general term for a group of clay minerals consisting mainly of kaolinite and halloysite, with a content of over 90%. It is mixed with pyrite, limonite, rutile, quartz, chalcedony, alum, etc. Kaolin has excellent process characteristics such as plasticity, adhesion, sintering, and fire resistance, so it has wide application in industries like ceramics, papermaking, rubber, plastics, and refractory materials. Kaolin includes hard kaolin, loose kaolin, and sandy kaolin according to the composition. Sandy kaolin is the common kaolin and generally adopts the wet beneficiation process.
Process Description
Wet process includes three stages: ore preparation, mineral processing, and final product processing. Mix the kaolin raw ore with water and dispersants in a mixing tank to make the slurry, purify the kaolin slurry with appropriate fineness, and remove large particles of sand and gravel. The beneficiation stage involves hydraulic classification, magnetic separation, and leaching to remove impurities.
1.Gravity Separation
The gravity separation and purification process includes trommel washing screening and sand washing classification. It mainly utilizes the density and particle size differences between kaolin and gangue minerals to remove lightweight organic material and high-density impurities containing iron, titanium, and manganese. To purify kaolin and reduce or remove the negative impact of impurities on its whiteness.
2.Separation
The hydrocyclone group achieves grading and removing some impurities, which has good application value. It is difficult to obtain the final kaolin product that meets the requirements through the gravity separation process. After gravity separation and purification, the qualified product will purified through calcination, magnetic separation, and leaching to get the final product.
2. Magnetic separation
The magnetic separation process will remove weak magnetic staining impurities such as hematite, siderite, pyrite, and rutile from kaolin. The weakly magnetic impurity particles removal from kaolin requires a high magnetic field induction intensity and magnetic field gradient. The development of magnetic separation technology and equipment upgrades have enabled effective magnetic separation and purification of non-metallic minerals such as kaolin.
Related Case
The raw ore is a loose material consisting of large and small stones and sand. The client requires a simple process design with an attrition scrubber and filter press machine, with no need for recovering tailing water.
The final kaolin products are used for manufacturing factories like bathroom utensils, ceramics, etc. There is no requirement for iron removal.Equipment includes the trommel screen with hopper, attrition scrubber, spiral sand washer machine, wheel sand washing machine, dewatering screen, slurry pump, hydrocyclone, cone thickener, plate filter press, and belt conveyor.
Process
1. The truck unloads the raw material to the hopper with 80mm grille bars to screen out sandstone over 80mm. The material under 80mm enters the trommel screen to wash and separate the 5-80mm waste and 0-5mm kaolin.
2. 0-5mm kaolin enters the attrition scrubber for washing and separating fine particles. The material from the attrition scrubber enters the spiral and wheel washing machine to clean mud and separate fine sand particles. The overflow from the sand washer and underflow from the dewatering screen go to the slurry tank. The underflow from the sand washer goes to the sand pile.
3. Pump the slurry to the hydrocyclone for separation. The overflow from the hydrocyclone enters the cone thickener, and overflow from the cone thickener goes to the clean water pool. The underflow enters the plate filter press to get the final product. The underflow from the hydrocyclone goes back to the sand washing machine for processing.