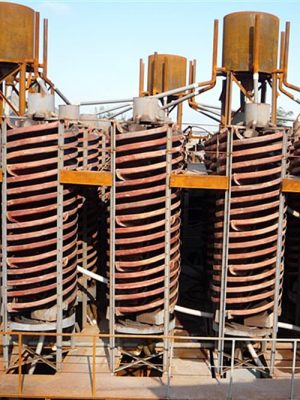
Turnkey Solutions
Silica Sand Processing Plant
The silica exists in natural silica sand and silica quartz stone. It accompanies other impurity minerals, like mica, feldspar, and iron-aluminum metal oxide minerals. The impurities reduce the value of quartz sand and affect product quality. Therefore, to meet the needs of industrial applications, it is necessary to carry out operations such as impurity removal and purification of silica sand. Silica sand is a common non-metallic mineral raw material that can be purified through mineral processing to produce high-purity silica sand. It is widely used in industries of glass, ceramics, metallurgy, casting, and refractory materials.
Process Description
Silica sand purification processing
The silica sand process includes several processing steps, including scrubbing, magnetic, and gravity separation to remove mineral impurities from the raw quartz sand and obtain high-purity silica sand with particle size and impurity content that meet the requirements. The treatment method for natural silica sand is as follows.
1. Scrubbing and classification
The attrition scrubber utilizes the mechanical force of the scrubbing machine and the stripping force between sand particles to remove the iron films, bonding, and mud impurities on the surface of silica sand, further crushing the unconsolidated mineral deposits.Through classification operations to achieve further purification of silica sand.
2. Spiral chute gravity separation
When the raw material contains a small amount of heavy mineral impurities (such as zircon), since it lacks magnetism and has higher specific gravity than quartz, the gravity separation solution effectively removes such heavy mineral impurities. When the raw material mortar rotates and slides along the spiral chute surface, various minerals will separate under the dual effects of gravity and centrifugal force according to the specific gravity. The larger the difference in mineral-specific gravity, the higher the degree of separation.
3. Magnetic separation
Magnetic separation is one of the effective methods for removing iron impurities from raw materials. It usually uses a strong wet-magnetic separator for the weak magnetism of minerals such as hematite, limonite, and biotite. Silica sand containing magnetite impurities uses weak-magnetic separators or medium-magnetic separators for separation.
Silica quartz stone process
Silica quartz stone will go through a crushing and grinding stage before entering the purification stage.
1. Silica quartz stone crushing and screening process
The raw silica quartz stone enters the jaw crusher for primary crushing. The material from the jaw crusher enters the circular vibrating screen by a belt conveyor for screening. The qualified materials under the screen enter the next stage, and the unqualified materials on the screen enter the spring cone crusher by another belt conveyor for two-stage crushing and screening. Before going to the crusher, the materials undergo metal detection and iron remover and then sent to the crushing and grading equipment to form a closed loop, which improves crushing and screening efficiency.
2. Silica quartz stone grinding process
The crushed silica goes to a grinding machine for grinding to separate it from impurities as much as possible and achieve optional particle size. The specific process is as follows: after the crushing process, the material enters a belt conveyor to the powder bin for storage, and a vibrating feeder transports the material to a ball mill for grinding. Qualified materials enter the slurry tank. Pump the slurry with a slurry pump to the next stage for washing and grading.
Related Case
Ore type: 80% of the material is 0.1-0.6mm silica sand containing iron. This plant adopts gravity and magnetic separation solutions.
Process
- The raw ore size is under 5mm. First, the truck unloads the silica sand to the hopper, and the belt conveyor feeder under the hopper transports the silica sand to the attrition scrubber for washing and crushing the block material.
- The silica sand from the attrition scrubber enters the trommel screen to wash and screen out 0-0.6mm and over 0.6 mm silica sand.
- The 0-0.6mm silica sand enters two spiral washing machines and gets overflow and underflow material. Overflow material goes to a slurry tank, and underflow material enters the Classification tower (thickening cone+hydraulic classification drum+ trommel screen)
- The classification tower separates overflow material, silica sand under 0.1mm, silica sand 0.1-0.6mm, over 0.6mm. Overflow material, silica sand under 0.1 mm goes to the slurry tank. 0.1-0.6mm silica sand enters the spiral chute for separation.
- The concentrate from the spiral chute enters the plate magnetic separators to remove iron and other magnetic minerals. After magnetic separation, the silica sand enters the dewatering screen for dehydration and gets dry 0.1-0.6mm silica sand.
Equipment includes hopper + belt conveyor feeder, attrition scrubber, trommel screen, belt conveyor, spiral washing machine, classification tower (thickening cone+hydraulic classification drum+ trommel screen), slurry pump +tank, spiral chute, plate magnetic separator, dewatering screen.