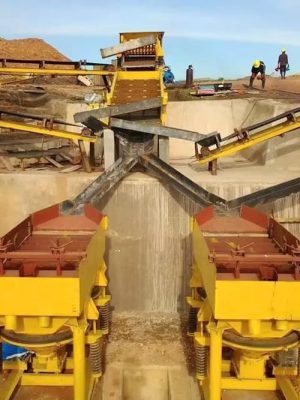
Turnkey Solutions
Tantalum Niobium Ore Processing Plant
Tantalum-niobium ore refers to the general name of minerals containing tantalum and niobium. Tantalum-niobium ore is often accompanied by a variety of metals. The ores commonly mined include tantalum-niobium ore, coltan, niobite(columbite), tantalite, tin-manganese tantalite, fine crystal, etc. Different ore properties require different beneficiation methods and equipment.
Beneficiation Process
Tantalum-niobium ore dressing plants are generally divided into rough selection and fine selection. Rough selection mainly uses gravity separation processes, but there are also cases where magnetic separation and flotation combined processes are used to obtain mixed coarse concentrates. Due to the complex composition and difficulty of separation of tantalum-niobium coarse concentrates, it often requires the use of one or two or more combinations of methods such as magnetic separation, gravity separation, flotation, and electrostatic separation to achieve the separation of multiple useful minerals.
Crushing
Rock Tantalum-niobium ore needs to be crushed, and equipment such as hammer crusher, jaw crusher and cone crusher are commonly used. Among them, the cone crusher is suitable for fine crushing work. In the fine grinding stage, a combination of rod mill, ball mill, vibrating screen and other equipment is usually used to form a closed-circuit grinding system to increase the release rate of ore.
Ore washing
For the extraction of sand tantalum niobium ore with large mud content and strong viscosity, the ore washing operation is crucial. Rotary Scrubber is usually used for ore washing treatment. Through cleaning, soil impurities in tantalum-niobium ore can be effectively removed to facilitate subsequent mineral processing.
Gravity separation
Since tantalum-niobium sand ore has a high degree of monomer dissociation, the gravity separation process can effectively remove a large amount of gangue minerals and obtain a mixed coarse concentrate containing tantalum-niobium, tungsten, tin and other minerals. Roughing plants usually use a variety of gravity separation equipment such as jig separator, spiral chutes, shaking tables and centrifugal concentrator for separation. The gravity separation method is pollution-free and low-cost, but the separation and recovery rate of sludge is low.
Magnetic separation
Both tantalum-niobium ore and tantalite are magnetic, but gangue minerals usually are not magnetic, so gravity separation and magnetic separation are often combined. The mixed concentrate is sent to the concentration plant. In order to improve the separation efficiency, it is generally pickled first to remove the influence of iron minerals on the mineral surface.
Flotation
Tantalum-niobium ore flotation method is often used in combination with gravity separation to process tantalum-niobium ore sludge, reduce the loss of tantalum-niobium ore, and improve the grade of concentrate. This method is based on the difference in physical and chemical properties of the mineral surface and is treated with flotation reagents, so that useful minerals are selectively attached to the bubbles to achieve the purpose of sorting.
100TPH tantalum niobium processing plant
The unit’s capacity can be customized. Pictured is 100tph. The raw material is alluvial and rock mixture type, containing clay.
Cleaning and beneficiation: The ore washing machine cleans and screens the ore. Particles smaller than 20mm are transported into the jig to obtain concentrates of 2 to 20mm.
Materials smaller than 2 mm enter the shaker to recover fine tantalum and niobium particles. The shaking table is divided into two stages, and the second stage further recovers the medium ore from the first stage to increase the recovery rate.
Crushing: The hammer crusher will crush the material larger than 20mm to less than 20mm, and then conduct mineral processing.
Dehydration: The tailings from the jigging machine and shaking table respectively enter the spiral sand washer and wheel sand washer for dewatering.