Tin processing plant
Tin is an important metal with anti-corrosion properties and is often used as an anti-corrosion layer for other metals.
An important source of tin is cassiterite (an oxide mineral). Most cassiterite comes from weathered alluvial deposits or placer deposits, as well as some rock tin ores. Extracting tin from cassiterite requires gravity separation and magnetic separation.
Another part of tin is extracted from its sulfides such as cylindrical cassiterite, silver-tin sulfide and lead-tin sulfide. When recovering this part of tin, flotation desulfurization treatment is required.
JXSC has designed tin ore processing plants for many customers. We can provide you with the most cost-effective tin beneficiation process and tin mining equipment configuration according to the characteristics of your ore.
Tin Mining Process
Tin ore and gangue have a large difference in specific gravity, so gravity separation is usually used for tin beneficiation plant. Sometimes, tin ore may contain other minerals such as magnetite and hematite, which cannot be separated by gravity separation, so it is necessary to use magnetic separation or flotation and other processes for further purification.
The following are some commonly used processes in tin beneficiation plant.
Crushing and grinding system: For rock tin ore, crushing and grinding are required before beneficiation, firstly to separate tin from gangue mineral monomers, and secondly to meet the feeding requirements of subsequent beneficiation equipment. Jaw crushers and hammer crushers are usually used to crush the raw ore. For ores with small or uneven tin distribution, grinding is also required to release tin. Ball mills are often used in this process.
Washing system: For alluvial tin ore, due to long-term weathering, it contains more clay, so washing and desludging are required. The main purpose of desludging is to dissociate and disperse the fine mud attached to the coarse particles to ensure the subsequent beneficiation effect. Trommel scrubber is usually used for washing, which can desludging and screening at the same time.
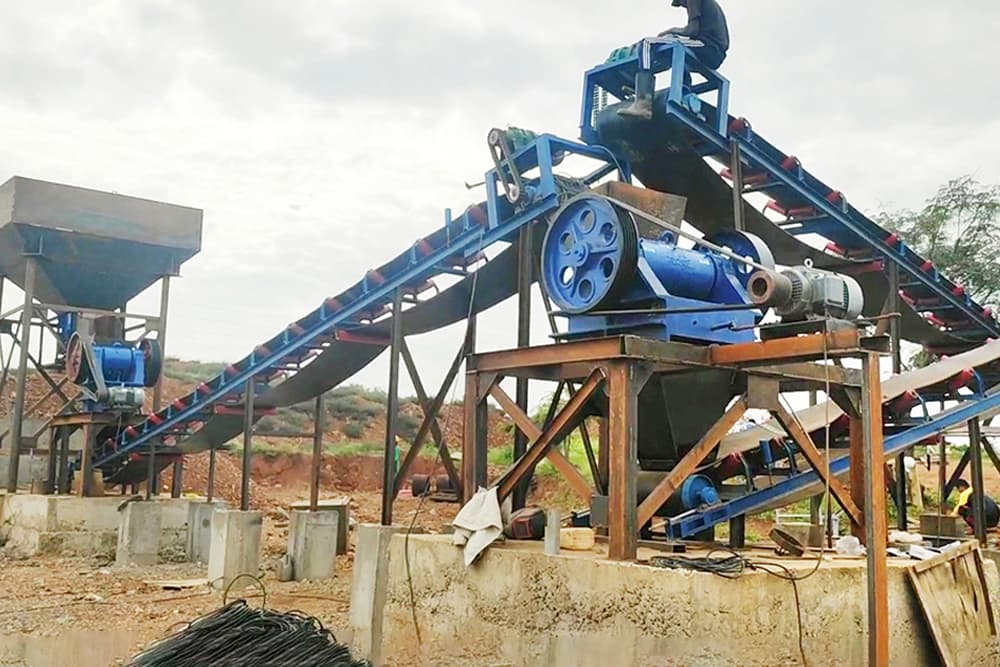
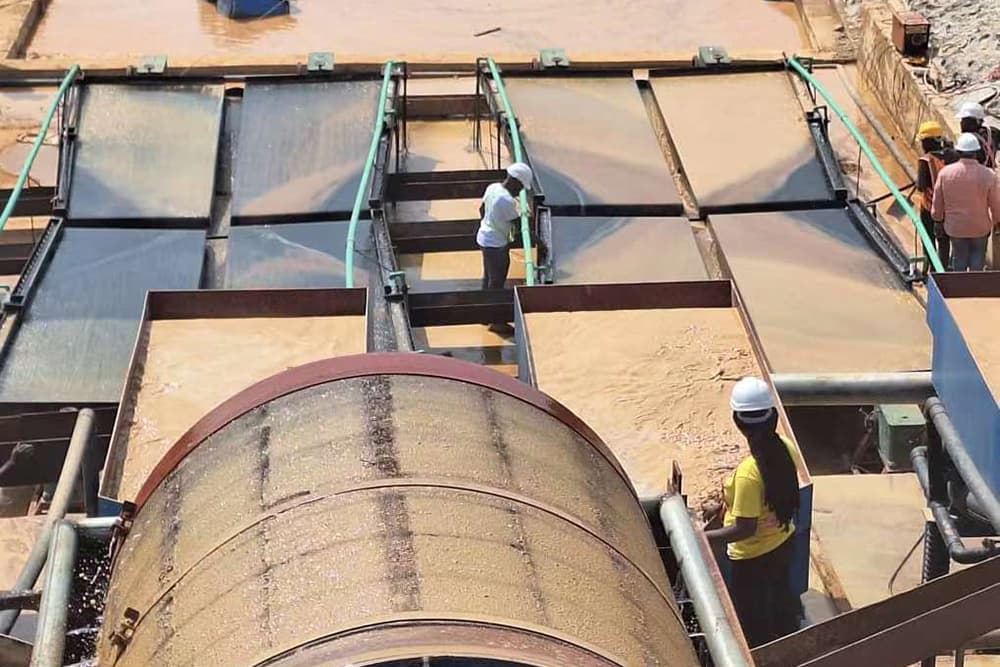
Gravity separation system: The gravity separation method uses the difference in mineral density to separate the dense tin mineral particles from the low-density gangue particles. It is usually divided into two stages: first, the jig separator is used to roughly select larger particles, and then the shaking table is used for fine selection to process and sort the finer particles. Sometimes, spiral chute is used for roughing, which has the advantages of small footprint and large processing capacity.
Magnetic separation system: Some tin ores are associated with various iron oxide minerals (such as magnetite, hematite and limonite, etc.), tungsten ore, etc. These symbiotic minerals cannot be separated by gravity separation, so the concentrate is subjected to magnetic separation after gravity separation to separate magnetic minerals and improve the grade of tin concentrate.
Flotation system: Tin ore is brittle and easy to muddy during crushing and grinding. It is difficult to recover tin from fine mud by gravity separation. Tin is easily captured by various fatty acids and soaps, so flotation is a good supplementary treatment method. The raw material for flotation is generally gravity tailings less than 0.04mm, and the ore mud less than 0.01mm needs to be removed first.
If the ore to be floated is vein tin ore, it is often associated with sulfide minerals of metals such as iron, arsenic, antimony, lead, copper, and zinc. At this time, the sulfide minerals should be first floated out with an activator for the sulfide minerals, and then the tin ore should be floated to prevent the sulfide from contaminating the tin ore concentrate.
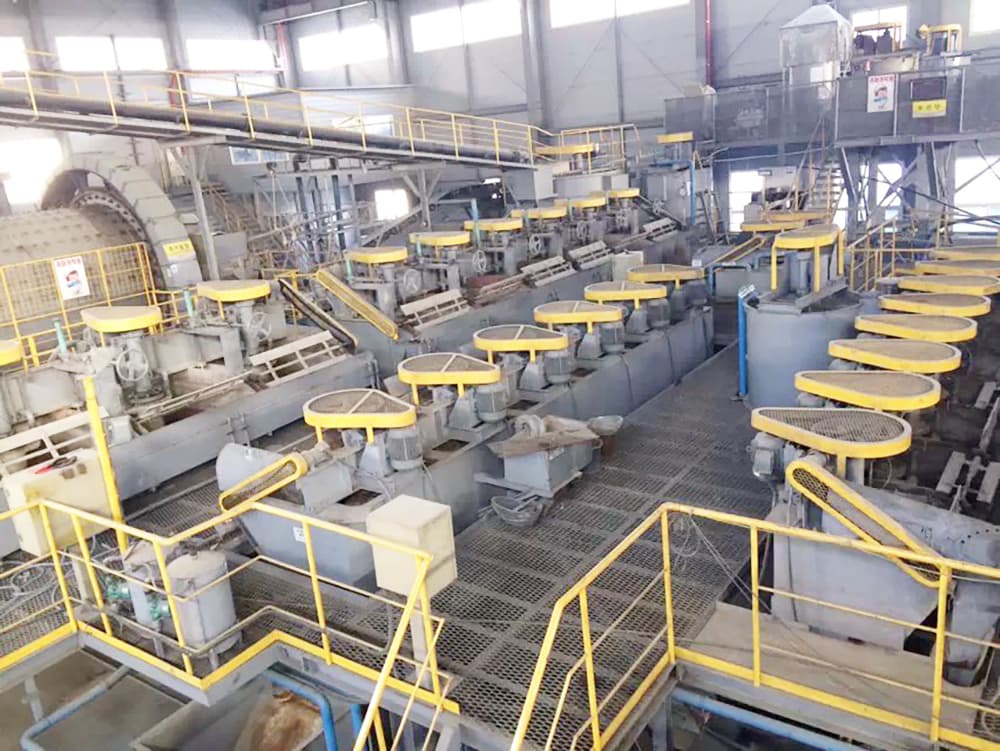
Extraction of Tin from Its Ore
Alluvial tin ore processing plant
- Washing
- Gravity Separation
- Magnetic separation
- Tailing dewatering
● Trommel Scrubber wash the clay in the raw ore and screens out the oversized waste rock.
● The washed ore is first roughly selected in the jig separator, and the concentrate below 2mm is sent to the shaking table for selection.
● The concentrate of the shaking table is passed through a three-disc magnetic separator to remove other impurities and further improve the tin ore grade.
● The tailings of the jig are dewatered by the spiral dewatering machine, and the shaking table tailings are dewatered by the dewatering screen to achieve the recycling of tailings water.
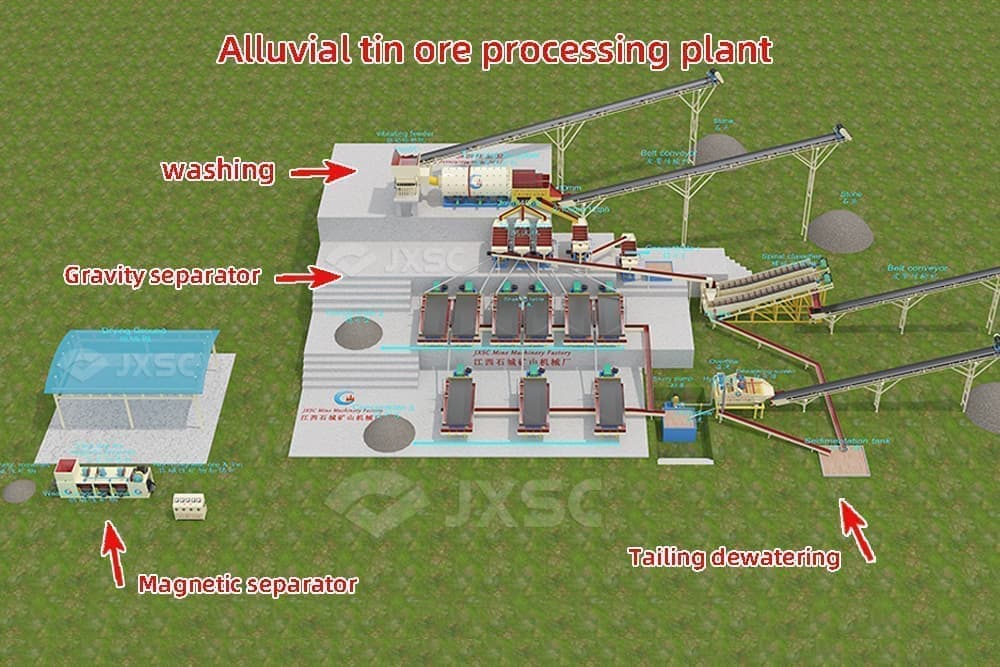
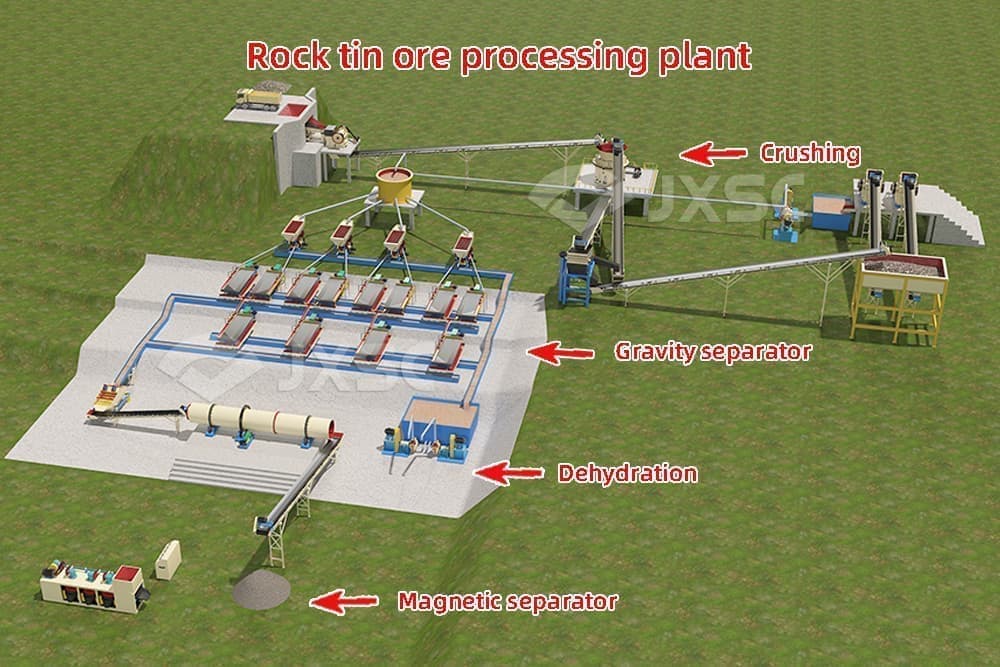
Rock tin ore processing plant
- Crushing
- Gravity Separation
- Dehydration
- Magnetic Separation
● The crusher crushes the raw ore, and the vibrating screen screens the ore that does not meet the crushing requirements and returns it to the crushing system for secondary crushing.
● After crushing, the material is sent to the jig separator for rough selection, and the jig separator concentrate is finely selected by the shaking table to obtain tin concentrate.
● The tin concentrate is dehydrated by the dehydration system. The dryer is used in the figure. In practice, the dehydration screen is also a commonly used dehydration equipment.
● The dehydrated tin concentrate is removed from the impurities by the magnetic separator to improve the tin ore grade.
Tin Mining Equipment
JXSC has designed efficient tin processing plant for many customers around the world. Please send us your mineral mining information. A technician will contact you immediately.
Why choose JXSC
Free design of gold ore beneficiation process. Provide ore sample testing services. Turnkey solution.
Products are produced in strict accordance with international standards. One year warranty, accessories provided.
Engineers provide on-site guidance on installation and commissioning of equipment.
Our Client
The JXSC company provided Nigeria with a full set of 100TPH alluvial tin ore processing plants. The plant equipment includes a feeder, trommel scrubber, jig separator, shaking table, three-disc dry magnetic separator, spiral dewatering machine, dewatering screen, and belt conveyor.
Raw ore conditions and customer’s requirements:
1) Raw materials contain sticky clay.
2) Tin concentrate particle size 0-10mm accounts for 60% of raw materials (0-2mm accounts for 80% and 2-10mm accounts for 20% of concentrate ore).
3) Maximum ore feeding size is 400mm.
4) Processing capacity is 100 tons per hour.
5) Customer requires dewatering tailing ore.
6) Customers require magnetic separation after gravity separation.
We have designed the most effective process flowchart for this tin plant according to the above ore conditions and the customer’s requirements.
Process flowchart description:
- Washing system
Raw materials are evenly fed into a trommel scrubber by a vibrating feeder to wash off the clay and screen out oversized waste stones. The vibrating feeder is equipped with a grizzly bar, and a gap of 70mm to remove over 70mm of big waste stone. The Trommel scrubber is equipped with two layers of screen, 2 mm, and 10mm, to sieve out 0-2 mm, 2-10mm, and above 10mm waste stone.
Above 70mm big waste stones from the vibrating feeder and above 10mm small waste stones from the trommel scrubber are sent to far places by belt conveyor.
- Gravity separation by jig separator and shaking table
0-2mm slurry ore from Trommel scrubber auto flow to jig separator by gravity for primary concentration tin concentrate. Tin concentrates from the first stage of jigs are sent to shaking tables for further upgrading. To improve the recovery rate, the middling of shaking tables is sent to the second stage of the shaking table to recover more tin concentrate.
2-10mm from trommel scrubber auto flow to another jig separator by gravity for primary concentration tin concentrate. Its tin concentrate goes to the secondary stage of the jig separator for fine separation, to improve tin grade. This is required by the customer.
- Magnetic separation
This customer has a high requirement for tin concentrate grade, so all 0-2mm tin concentrates are sent to three disc dry magnetic separators to remove other impurities further and improve tin grade.
- Tailing dewatering system
All tailings from jig separators are sent to a spiral dewatering machine for dewatering to dry the tailings and can be sent by belt conveyor. The tailing water can be recycled and reused in this plant.
All tailings from shaking tables are sent to the hydrocyclone, overflow from the cyclone is clear water, and underflow goes to the dewatering screen for further dehydration. Over the screen is a kind of dried tailing sand, and under the screen is mud water that goes to the settling pond.
The whole process flowchart includes four parts: washing system, gravity separation system, magnetic separation, and tailing dewatering system. After processing by this plant, customers can finally get a very high grade of tin concentrate. At the same time, tailing water can be recycled and reused in this plant. So this is a very efficient plant.